www.industry-asia-pacific.com
29
'16
Written on Modified on
Morgan Advanced Materials Announces Ceramic Acoustic Reflector Manufacturing Capability for Flow Metering
Morgan Advanced Materials has developed the capability to produce complex ceramic acoustic reflectors used in ultrasonic flow meters, drawing on pioneering research carried out in conjunction with Loughborough University, ensuring consistent measurement accuracy over a longer projected lifespan.
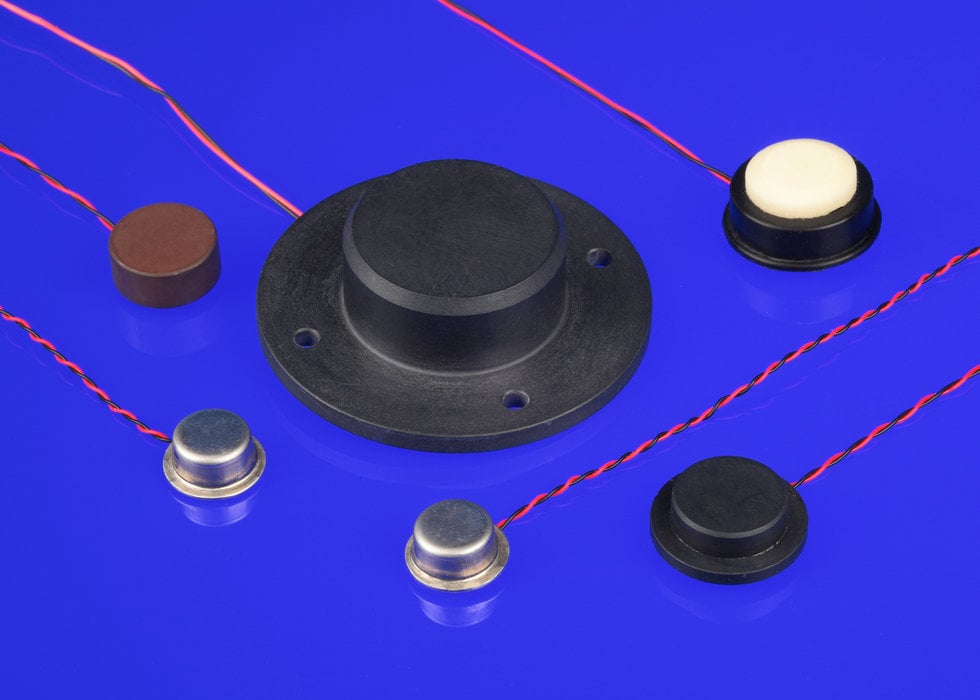
While stainless steel acoustic reflectors initially offer greater measurement accuracy, this has been found to decline quite significantly over a number of years. Conversely, ceramic wedges made using proprietary Alumina from Morgan (Hilox grade) do not experience a comparable decline in performance, offering greater measurement accuracy over the long term. After a period of ten years, the gap in performance between ceramic and stainless steel reflectors noticeably widens. Morgan is able to provide high sensitivity and wide bandwidth ultrasonic sensors for flow measurement, to increase this starting sensitivity further.
Morgan’s ceramic acoustic reflectors offer a variety of additional benefits over their stainless steel counterparts, the inert properties of the material make it safer in water processing while its lightweight composition reduces the overall weight of components without compromising on durability. Other benefits include improved surface smoothness and scale thickness, both of which enhance the accuracy of meter readings.
Drawing on its vast experience in application engineering, Morgan has discovered a pioneering approach to developing ceramic reflectors using injection molding technology, meaning it can now accommodate a wider range of bespoke designs with complex geometries to meet the requirements of industry. This method also allows Morgan to tune the sensors to the correct beam width and acoustic properties, ensuring maximum sensitivity by potentially reducing the turbulence of the water flow path around wedges. This is done by creating more complex shapes that can aid the fluid dynamics of the flow in the tube.
Charles Dowling, Business Manager at Morgan Advanced Materials, commented: “This development is the outcome of a unique collaboration between Morgan and Loughborough University and is a clear example of where we have pushed the boundaries in order to provide complete solutions for our customers. Longevity is a key challenge for many of our customers in industrial metering and we have optimised our ultrasonic sensors to deliver sustained performance over time compared to other materials. As a result our customers can feel reassured that their flow meters will remain accurate for longer.”
For further information, please visit: www.morgantechnicalceramics.com/ceramic-wedge