www.industry-asia-pacific.com
10
'16
Written on Modified on
MORGAN ADVANCED MATERIALS EXPANDS SILICON CARBIDE PRODUCTION CAPABILITY TO MEET EUROPEAN DEMAND
Morgan Advanced Materials, a global leader in the development and application of advanced material technologies, now has a dedicated volume silicon carbide manufacturing facility in Stourport, UK. This increased capacity has enabled the company to augment its sales in Europe and worldwide with these higher performing silicon carbide materials.
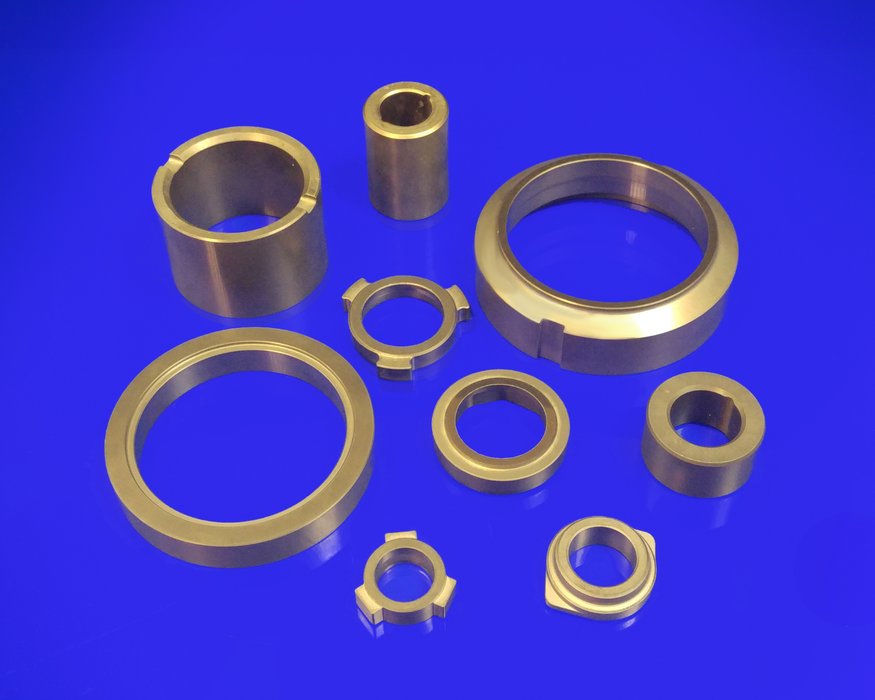
Global demand for silicon carbide in pump designs is soaring, largely as a result of the technical and cost benefits this ceramic grade can provide over other materials such as tungsten carbide and alumina. Morgan’s silicon carbide ceramics continue to give high performance when pumping contaminated, abrasive and corrosive fluids and provide excellent sealing at high pressures. They have a low thermal expansion coefficient and high thermal conductivity which contributes to its outstanding thermal shock resistance; this is particularly important if pumps have a risk of running dry. Overall pump reliability is increased and as a result companies experience less downtime, resulting in reduced operational costs.
The move to increase the silicon carbide manufacturing capability is a natural progression for Morgan, which has been manufacturing alumina ceramics for pump applications for the last 50 years. The company has recently completed investment in new kiln and manufacturing equipment, capable of firing and processing high volume silicon carbide products through a dedicated cell. This has enabled Morgan to form near press-to-size silicon carbide components up to 80mm (3.15 inches) in diameter, with detailed design features and precision dimensional tolerances.
The addition of graphite loaded silicon carbide material to Morgan’s range enables the business to help its customers to improve dry running performance in pump seals, as well as reducing the risk of seals failing in operation. Mechanical seals are an essential part of many pump systems in sealing the rotating motor shaft from the pumping fluid; they trap a thin film of liquid, which acts as both a lubricant and a seal. However, these pumps sometimes continue to run when there is no fluid present, resulting in increased friction and higher operating temperatures, which can cause the adjacent O-ring to degrade, and the seals to leak. The low thermal expansion efficient of graphite loaded silicon carbide, together with its high thermal conductivity, provides greater protection in these circumstances.
Chris Paine, Business Development Manager at Morgan Advanced Materials, commented: “This extensive investment enables us to offer seamless production of silicon carbide seal and bearing products, from raw materials to finished parts manufacture at one single site. This means that we can provide the requisite quality assurance for all our products while responding to global demand for high volume manufacturing capabilities.
“Silicon carbide is already a proven material for heavy duty pump products, providing greater wear resistance and improved performance over alternative materials. We are continuing to invest in our facility, and our research and development, to ensure we can continue to provide solutions to meet the engineering problems faced by customers.”
For further information, please visit: www.morgansealsandbearings.com/sic-production