www.industry-asia-pacific.com
31
'16
Written on Modified on
SLIP RINGS – AT THE HEART OF MODERN PACKAGING APPLICATIONS
The packaging sector presents a variety of challenges for individual machine components depending on the application. Not only must production run without unscheduled interruption, placing reliability at a premium, but the correct speeds of operation for each individual aspect of the process must be maintained to ensure seamless and correct processing.
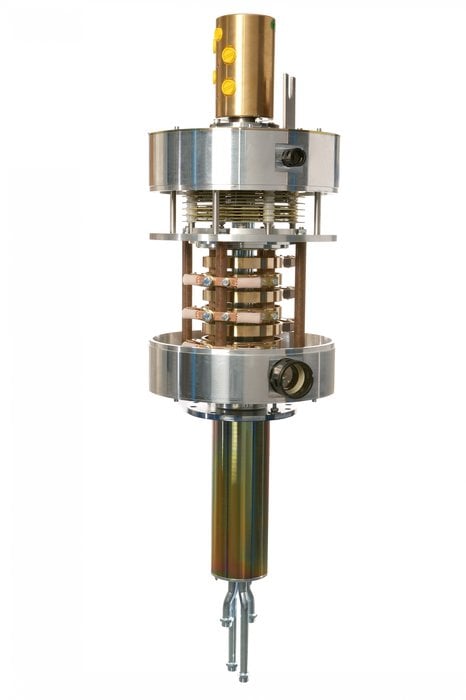
Typically, the slip ring comprises a stationary graphite or metal contact or brush which rubs against the exterior diameter of a rotating metal ring. As the ring turns, the electric current or signal is conducted through the brush to the metal ring making the connection. Additional ring/ brush assemblies can be located along the rotating axis if multiple electrical circuits are required.
Not only can slip rings improve mechanical performance and simplify system operation; they can also potentially eliminate the issues associated with damage-prone wires hanging from movable joints.
Their benefits are now enjoyed by machine operators across a broad spectrum of applications. In winders and rewinders used in the lamination of carton board, they transmit the power and encoder signals. They also power cutters and winders used in film production. Even the heat-sealing process on packets of sweets can be driven by a slip ring, while they are also found in tobacco product processing.
This versatility is of course an advantage but it makes correct specification and maintenance absolutely critical. The decision on the type of slip ring used will inevitably be governed by a range of factors. These include operating speed; the system current and voltage; dimensional space available; the IP, data and bus system in operation; and the presence of media such as water, oil or compressed air. Slip rings are typically made from copper or brass –and plated with either gold, silver or rhodium depending on the application requirements.
Various modified versions of slip ring are available depending on the specific application requirements.
Mercury-wetted slip rings boast low resistance and a stable connection but instead of a sliding brush contact they have a pool of liquid metal molecularly bonded to the contacts. During rotation the liquid metal maintains the electrical connection between the stationary and rotating contacts. However, the use of mercury poses safety concerns and is not an option in sectors such as food & beverage, pharmaceutical or anywhere else where contamination could be a serious threat. In these sectors, precious metal contacts should always be specified.
Carbon to copper slip rings, meanwhile, are best suited to higher rotation applications of up to 3,000 rpm, for example in equipment with twist cables.
Modular systems are also available which are ideal for transmission of information via an Ethernet or when working with sensitive analogue signals. Typical rotation speeds are up 20 rpm.
In applications where space is limited, or rotational speed is very low (no more than 5 rpm), a slip ring plate system or ‘pancake’ can be specified.
In a pancake slip ring the conductors are arranged on a flat disc as concentric rings centred on the rotating shaft. This configuration has greater weight and volume for the same circuits, greater capacitance and crosstorque, greater brush wear and more readily collects wear debris on its vertical axis. However, it offers reduced axial length for the number of circuits, and with a service life of up to 4 million cycles – which can be maintenance-free depending on the application – represents an attractive option in many applications, though it should be noted that 16A is the usual maximum current.
Pancake systems are attracting considerable research and development currently and systems offering faster rotation and at a higher current are likely to be introduced in the near future.
As with any production-critical component, working with a supplier such as Morgan who can develop a detailed understanding of an application and then recommend design and supply an appropriate solution is crucial.
For further information visit www.morganadvancedmaterials.com.
Ingo Carnott, Morgan Advanced Materials