www.industry-asia-pacific.com
05
'22
Written on Modified on
VITESCO TECHNOLOGIES INCREASES SUSTAINABILITY IN MANUFACTURING WITH NEW LASER WELDING TECHNOLOGY
Vitesco Technologies uses state-of-the-art green lasers from TRUMPF for energy-saving welding of copper. Due to electrification in the drive, copper welding is currently a key manufacturing process. Green laser systems are energy-efficient and also reduce manufacturing effort. Copper welding with green lasers is already being used in a current electronics series project for the BMW group.
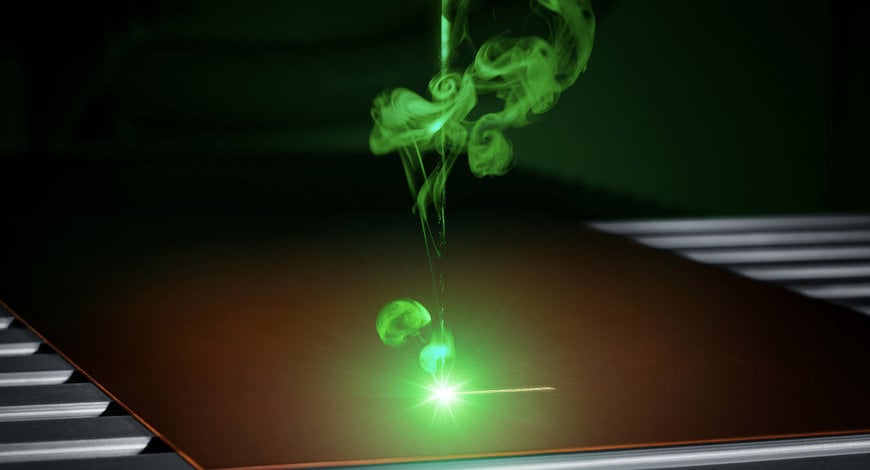
Vitesco Technologies, a leading international manufacturer of modern drive technologies and electrification solutions, is using innovative laser systems from its long-standing production engineering partner TRUMPF. With the introduction of the new green laser equipment for copper welded joints, Vitesco Technologies is among the pioneers in the serial use of this new solution. Compared with infrared laser systems – the standard in copper welding to date – the use of green lasers can reduce energy consumption by up to 20 percent, depending on the application, and thus the CO2 footprint per laser welded joint. At the same time, production becomes more sustainable by the fact that green laser systems cause virtually no copper spatter during welding, which otherwise means more effort during production.
Laser specialist TRUMPF has for the first time developed a green laser system of this type for industrial production, which operates in the visible light spectrum with a wavelength of 515 nm. Compared to the infrared laser welding technology with a wavelength of around 1030 nm used to date, the welding process with the green laser is more energy-efficient and controlled.
For the first time, the green laser is being used at Vitesco Technologies for the current production of sophisticated battery management electronics for the BMW Group. Already here, the energy consumption for the welding assembly could be reduced by 4 percent only by substituting the beam source.
“Our sustainable manufacturing with smaller CO2 footprint and very stable processes is a competitive advantage. Because for vehicle manufacturers, sustainability with the highest quality is strategically relevant. That is why the use of green laser systems is important for us." Thomas Stierle, member of the Executive Board at Vitesco Technologies.
Sustainable and innovative manufacturing technology: green lasers
Welding copper is a complex process. At the same time, the requirements for copper welded joints and their number in electrification products are increasing. Up to now, copper has been welded using infrared laser systems (IR lasers). This process is difficult to control, however, because the amount of energy absorbed by the copper during the welding process changes abruptly after a certain point. Initially, the copper reflects almost all of the laser radiation before the weld suddenly heats up. Complex measures are required to protect electronic systems from the copper spatter that can be generated in the process. Because of the initial high reflection and low energy absorption, IR lasers require a lot of power, which makes them less sustainable compared to green lasers.
“Green lasers are far more efficient for welding copper than IR lasers. The new systems require less electric power and still deliver an unprecedented stable, repeatable process with a precisely controlled depth of penetration into the copper,” explains Rainer Pühl, head of operations in the Electrification Technology business unit. Thanks to these features, green laser systems are currently being made into a company-wide standard technology option for certain applications.
“Welding copper is a task that is as frequent as it is challenging for us. Together with TRUMPF, we developed the new green laser application in three years." Rodrigo Peres, head of the battery product line at Vitesco Technologies.
Green laser systems with a power of 2 kW are currently being used to mass-produce highly integrated and highly complex battery management electronics for the BMW group.
“The green laser has great potential for many electrification products. In addition to electronics, this also applies to electric motors. Among other things, we can use the welding process on a highly efficient stator with 138 welding points per motor,” adds Pühl. One of the technological advantages of green lasers is that even particularly difficult welds can be mastered successfully with a high level of process reliability. “The green laser is a key investment in the future of sustainable mobility – beginning with manufacturing,” says Pühl.
www.vitesco-technologies.com