www.industry-asia-pacific.com
17
'17
Written on Modified on
Morgan Advanced Materials predicts industry-wide adoption of alumina and silicon carbide components as electric vehicle market grows
A global manufacturer of automotive components is predicting widespread use of alumina and silicon carbide components in the electric vehicle market as OEMs face mounting pressure to reduce emissions and improve efficiency.
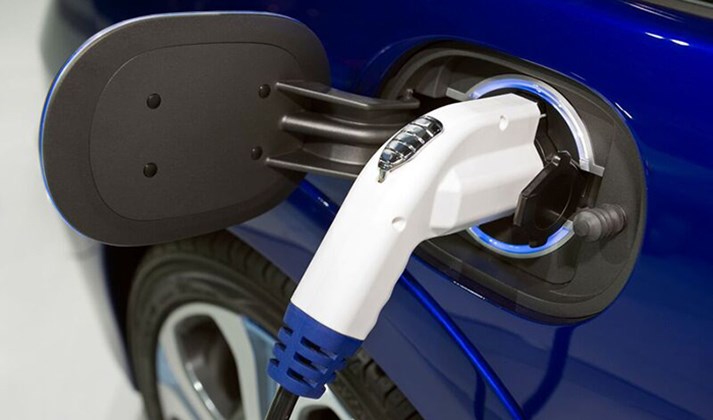
Morgan’s ceramic components are used in electric water pumps (EWP) for temperature control of the engine and battery components to ensure optimum performance and longevity. As a result, these pumps are being increasingly favoured in hybrid and full electric vehicles as well as petrol/diesel stop-start vehicles. This is because they are considered to be more efficient than their mechanical counterparts.
The use of alumina shafts and bearings, as opposed to steel, offers a number of advantages; predominantly on account of its superior wear resistance properties. Due to the fact that wear is reduced, the use of alumina ensures precision fit components, reducing vibrations and noise levels in line with the overall ‘feel’ of electric and hybrid vehicles. Moreover, alumina shafts and bearings are more durable and require less periodic maintenance. Depending on the application requirements, a combination of alumina shaft with silicon carbide bearings or alumina shaft with alumina bearings can be used. This choice depends on many application factors such as the cooling medium, rotational speed of the pump, materials in contact and the power rating. For example, silicon carbide bearings are preferred for large pump applications of 200W plus, typically found in larger vehicles such as electric buses and commercial vehicles.
Silicon carbide is proving to be a particularly useful material in mechanical seals for pump applications, demonstrating superior wear performance in temporary dry running conditions compared with traditional ceramic materials. This ensures that pumps continue to run smoothly for short periods without lubrication, ensuring that no damage is caused to the internal components, which can be an issue with other materials. This results in longer replacement cycles, reducing cost and minimising the likelihood of failure in operation. In addition to this, the chemical resistance properties of alumina and silicon carbide mean that it can comfortably withstand chemicals such as glycol, a cooling agent used in cooling pumps, in addition to abrasive debris, thus minimising the potential for leaks. Morgan’s proprietary materials have long been delivering a host of benefits including increased durability, chemical resistance and thermal stability in applications such as circulating pumps, automotive cooling/heating pumps, and vacuum pumps. Furthermore, tests have shown that performance in alumina shafts and bearings in automotive pumps will remain effective for in excess of 30,000 hours of continuous operation.
Arafath Jaleel, Technical Sales Engineer at Morgan Advanced Material’s Seals and Bearings Business, explained:” We have developed a range of materials with a proven capability to perform in demanding applications. We recognised a trend within the automotive sector and developed our portfolio of materials to better meet the future needs of this industry, namely requirements around increased energy efficiency, durability and increased wear resistance. With our extensive material science and pump application expertise, we are able to provide bespoke solutions to our customers from R&D stage to volume production. Furthermore, our high-volume manufacturing capability leaves us in a unique position to meet the production demands of tier two automotive manufacturers around the globe.”
For further information, please visit: http://morgansealsandbearings.com/en-gb/markets/automotive/