www.industry-asia-pacific.com
18
'24
Written on Modified on
Keba explores how software features contribute to the safety of wind turbines
Using Keba's software, PitchOne, the "multi-profile run" feature enables a safe feathering run for the rotor blades with different dynamic profiles.
www.keba.com
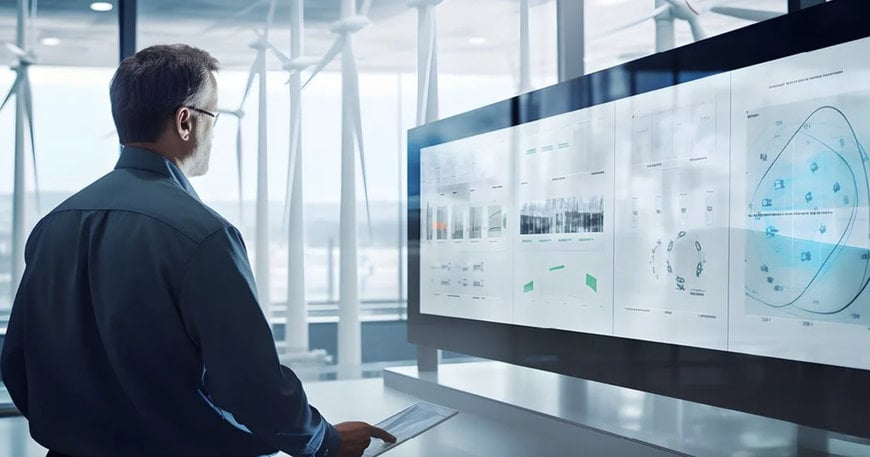
Software features can influence the load capacity of wind turbines during a feathering run by reacting intelligently to the respective situation. In addition, larger wind turbines bring new requirements that can be optimized by software enhancements.
A key component of the safety system of wind turbines is the pitch system, which is located on each of the three rotor blades. The pitch system control adjusts the rotor blades to the prevailing wind speed and thus ensures the optimum operating point of the turbine.
In addition to the task of maximizing the turbine's yield, the pitch system's much more important task is to guarantee safety. The pitch system takes over the braking function of the wind turbine and enables a feathering run to be carried out if this is necessary due to environmental influences or error messages. In the event of a feathering run, the system guarantees that the turbine is gently moved to the final position.
In which situations is a feathering run triggered?
There are different situations, also referred to as load cases, which require the triggering of a feathering run. A non-critical error message can be the failure of a temperature sensor, for example. The feathering run guarantees the protection of the entire system so that a fault diagnosis can be carried out. When a feathering run is triggered, the rotor blades must be turned out of the wind and brought into the safe 90-degree position, also known as the feathering position, in a matter of seconds. By turning the rotor blades out of the wind, the wind turbine is slowed down and thus reaches a safe state.
Examples of critical load cases can be strong, short-term changes in wind speed or load shedding due to failure or collapse of the power grid. When the wind is blowing and the turbine is in full operation, a power grid failure is particularly difficult for wind turbines. In such a case, the generator would no longer be able to supply energy to the grid. As a result, the rotor would quickly reach critical overspeed due to the loss of the braking effect. To prevent this, it is necessary to react very quickly and in a functionally safe manner.
In both cases, the feathering run guarantees the turbine operator the integrity of the turbine. At the same time, however, very strong forces act on the materials of the rotor blades and the tower. These forces cause increased stress, which can also lead to increased wear. This has a significant impact on the service life of the entire system. The systems currently available on the market do not differentiate between the causes of the feathering run. They therefore often intervene in the system with the largest possible control variable to protect the system, but also to protect the environment and therefore all of us. The wind turbines are therefore designed so that they always react to a worst-case scenario, even if it is a non-critical fault that needs to be checked
Intelligent software features can optimize the feathering run by allowing the pitch system to differentiate between different load cases and react appropriately. The material load can be reduced by a less extreme approach to the feathering run.
Pitch control has been the absolute standard for years when it comes to cost-efficient and robust blade adjustment of wind turbines.
Which software features play a role here?
To reduce material wear caused by the safety run, KEBA's software release for PitchOne enables profile adjustments during the safety run. With the new software features, PitchOne can respond safely to various load cases and trigger the safety run using up to four predefined profiles.
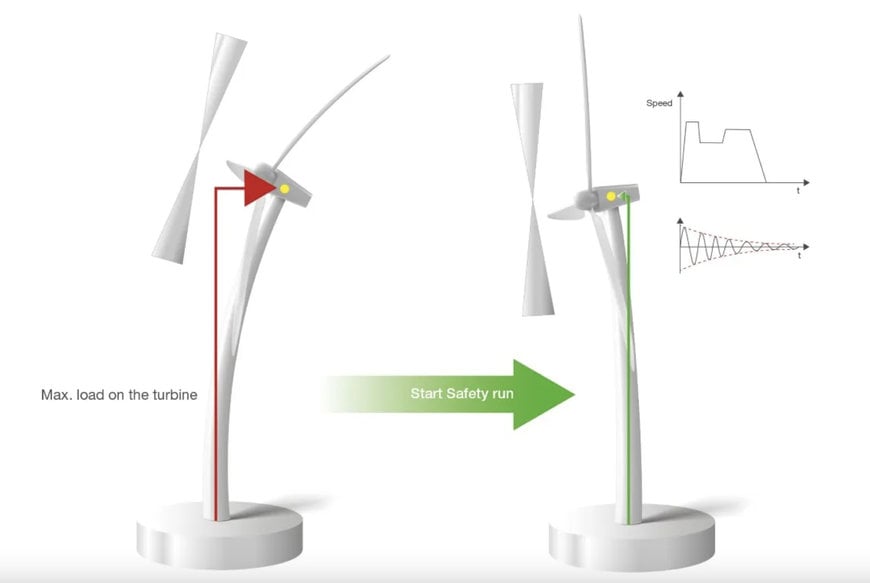
Reduction of the load during the feather run
What does this mean? The "multi-profile run" feature enables a safe feathering run for the rotor blades with different dynamic profiles: Different load cases therefore require different profiles. For example, the turbine control system selects a different profile for the individual rotor blades in the event of a serious fault, such as a power failure in windy conditions, compared to a feathering run resulting from a non-critical fault. We call these profiles dynamic because their speed and acceleration can be adjusted during the feathering run.
The decision, which profiles are selected, lies with the turbine control system, which makes a situation-specific decision for the fault situation.
What else accelerates the ageing process of wind turbines?
After the feathering run, a wind turbine is normally in the feathering position described above. This means that all three rotor blades are completely turned into the wind and no longer generate lift.
With larger wind turbines (from 4-5 MW), however, new difficulties may arise in the feathering position. For example, it is possible that there are environmental conditions that can cause a rotor blade to oscillate. There are certain wind-dependent situations that trigger the oscillation of a blade, which in turn causes the other blades to start moving as well. This is particularly critical as the turbine control system is in "sleep mode" after the end of the feathering run and there is no active monitoring of the blades.
For this behavior, the software in PitchOne provides for a deviation from the feathering position by adjusting a rotor blade. We are talking here about the final position mode, which provides for the safe end position to be approached after the feathering run and thus ensures the safety of the wind turbines before shutdown. This prevents unnecessary fatigue loads from occurring.
Conclusion: More functional safety through intelligent software
The software features of the PitchOne system play a crucial role in reducing material stress by optimizing the feathering runs of wind turbines. By introducing dynamic, multi-profile feathering runs, the pitch system can react to different load cases in a situation-specific manner, which reduces material fatigue and wear. In addition, the final position mode ensures that the rotor blades are brought into a safe final position after a feathering run to prevent unwanted movements of the rotor blades. By continuously developing the software of our PitchOne product family, we ensure functionally safe operation with the highest TÜV certification (level PLe KAT. 3 at system level).
www.keba.com