www.industry-asia-pacific.com
10
'23
Written on Modified on
SME Aerospace Malaysia puts MAPAL tools to good use
The aircraft component structural supplier SME Aerospace approached MAPAL Malaysia with the request for an improved machining time for a titanium part. The latest generation of titanium tools and an improved machining strategy made it possible to achieve a time saving of over three hours per part.
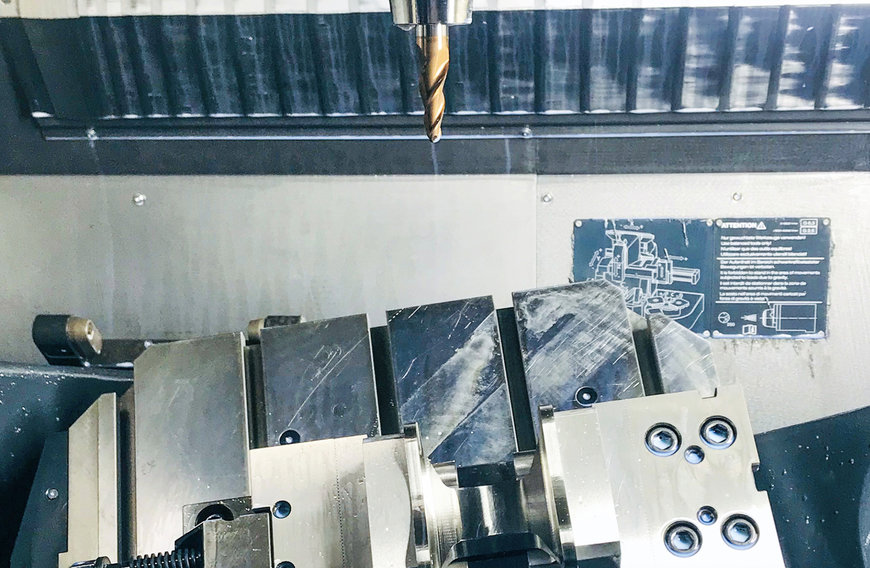
In Kuala Lumpur, SME Aerospace (SMEA) manufactures parts for major aircraft manufacturers, including Boeing and Airbus. The company does not produce prototypes but has focused entirely on the series production of parts. With typical lot sizes close to the hundreds, more than a million parts of very different sizes are produced each year. The company employs around 800 people in Malaysia and is very well positioned with modern machinery to achieve the required performance in manufacturing.
The cost pressure felt by businesses around the world has also hit the supplier in Malaysia. Most of the workpieces are made of aluminium. SME Aerospace can machine structural parts up to four metres in size on its machines.
At the moment, the supplier only produces few titanium parts, but wants to expand this area. For this, SMEA seeks to increase productivity in titanium machining in order to achieve a higher output on the machines. The company turned to MAPAL Malaysia to machine a special part. MAPAL’s Asian site has been up and running since 2008 and is also located in the greater Kuala Lumpur area. The subsidiary is managed by Kang Hum Lim, who took over the family-run business from his father. Most of the 17 employees have been with the company for a long time and are very knowledgeable in their trade.
The subsidiary offers MAPAL’s entire range of products and services, plus comprehensive technical support. In addition to sales, there is also an on-site manufacturing unit for solid carbide tools and a regrinding service. They work together with local companies for coating. Many of MAPAL Malaysia’s customers come from the automotive sector, but the aerospace industry is also playing an increasingly important role. MAPAL Malaysia could draw from the experience of Senior Sales and Application Engineer Kien Keng Mak for this project. Before joining MAPAL, he was employed for many years by a company that manufactures structural parts for the aerospace industry. For the new project with SME Aerospace, his programming skills on the Catia CAD/CAM system were particularly useful, as it correctly implemented the specified contours of the aerospace part to be milled from the solid on the machine.
Parts for the Airbus A320
The part for which SME Aerospace brought MAPAL Malaysia on board is a component for an Airbus A320. SMEA has already been producing about 40 parts per month for their customer for several years. At first glance, the part, which measures approximately 85 x 70 x 100 mm, looks like a brake caliper, but its machining is quite demanding with its sloping surfaces, various radii and transitions. To mill the part out of a titanium block, SMEA previously used solid carbide tools and tools with indexable inserts in a simple design. The manufacturer could not be satisfied with the processing time of 6:38 hours, and so SMEA evaluated another tool supplier.
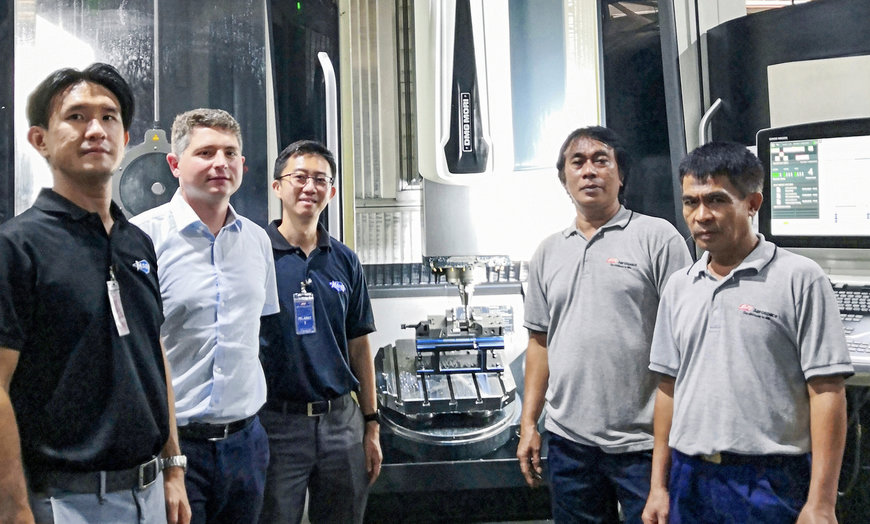
MAPAL Malaysia selected suitable tools and worked out a rough machining strategy. The technicians relied on the current tool portfolio for titanium machining, but also brought custom tools into play. Using the respective stored cutting data, they ran a simulation and calculated an expected machining time of 3:34 hours.
The Malaysian subsidiary then approached the titanium specialists at MAPAL’s headquarters in Aalen with this concept. There, they were amazed at the predicted time savings of almost 50 per cent. To verify the design, the TET-CAM team simulated the machining process again, with a particular focus on roughing, which made up about 65 per cent of the cycle time. In cooperation with the R&D department, machining strategies with solid carbide custom tools were developed and perfectly implemented in the CAD/CAM system Catia by MAPAL Malaysia. The project team says that this worked above all thanks to the excellent, open communication of all those involved. In this way, the specified contours of the part could be machined exactly from the solid.”
“We can only get the greatest possible customer benefit by running a simulation. Our TET-CAM team is the key to these kinds of projects here”, acknowledges Jens Ilg, who supports aerospace customers at MAPAL as Business Development Manager. “The team knows what the machine can do, what the machining should look like and how powerful our tools are.” In the end, the values from Kuala Lumpur and Aalen were very similar.
In Aalen, the tool concept was refined a little more, which further reduced the cycle time. For the tools, the manufacturer now also specified tool lives. Where possible, the solid carbide tools originally intended for roughing were replaced by tools with indexable inserts. This made it possible to minimise the number of tools that have to be sent to Germany for regrinding because of their complicated geometry. Indexable inserts can be recycled on site in Malaysia. This considerably increases sustainability in series production.
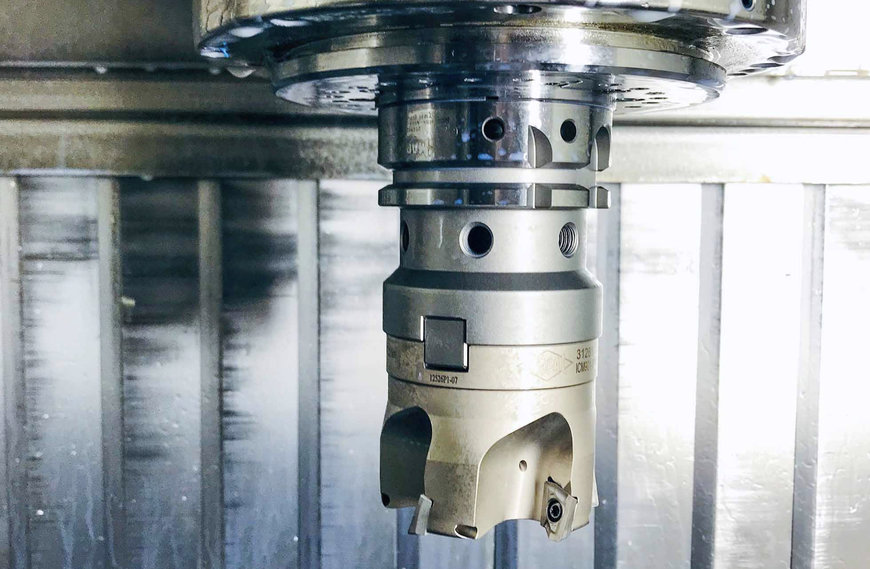
In order to reduce the machining time of the part by the predicted 50 per cent for the customer, MAPAL did not stop at replacing the previously used tools with high-tech tools for titanium. Instead, the specialists analysed the entire process and used clever programming tricks, tool features and machining strategies. The decision was made to machine in three clamping setups in order to prevent the part from deforming during milling. MAPAL Malaysia has designed the clamping fixtures for this itself. The matching chucks also came from MAPAL. They ensure that the coolant supply reaches the cutting edges perfectly and that there is reliable chip removal. Both are very important in titanium machining to avoid rapid tool wear. To be on the safe side, an external cooling system was included in addition to the internal coolant supply.
The MAPAL specialists completed the package deal for SMEA by programming the part directly on the customer’s computer, with the data of the machine on which the machining was to take place – a DMC 65 monoBlock.
In the first clamping setup, the surfaces for the bracket lever stop are milled and a dovetail is attached. The OptiMill-Tro-Titan is used for trochoidal milling of the pocket and is responsible for most of the cycle time savings. The side edge and various radii are machined with a raised head cutter and a taper milling cutter, each in a special design, in one clamping setup. Cutting angles, substrates and coatings are based on the knowledge MAPAL has gained in developing its standard tools for titanium. While tools with indexable inserts are used wherever possible for roughing, solid carbide tools are predominantly used for finishing in order to achieve clean surfaces. “We found a good combination of solid carbide and indexable insert technology for this project”, Ilg comments.
To ensure that nothing went wrong in the end, Global Project Engineer Markus Beerhalter supported the MAPAL Malaysia team during the commissioning. “Markus is our man for important and critical jobs in Asia”, says Ilg. “He has been with MAPAL for many years, knows tool applications and is very well connected.” Beerhalter was able to contribute his expertise in titanium machining on site. “With titanium, the noise during machining sounds very different”, he reports. “This is why, when optimising the cutting values, we also include the sound of the machining. Vibrations or poor cooling have a very negative effect on the tool life and the quality of the part. When an employee uses titanium tools for the first time, they find it a difficult to recognise this because the cutting values differ considerably from machining other materials.” Nevertheless, dummy material was used for commissioning to ensure that the five-axes machining runs without hindrances and that there really are no tool restrictions in the way. Series production could then start without producing rejects with the expensive raw material.
The machining time was finally reduced to 3:20 hours, which is an additional 14 minutes below the time agreed. SME Aerospace is very satisfied with this result as well as the support from MAPAL. Next, a very similar part is already being discussed, namely a stopper for aileron reversing.
www.mapal.com