www.industry-asia-pacific.com
28
'15
Written on Modified on
Resilient, seawater-resistant drive systems for seafood factory conveyors
Mussels, clams, oysters and other shellfish must be served fresh and remain alive until the very moment they are cooked. Hence, factories specializing in these delicacies tend to keep fresh catches submerged in salt water before they are processed. In such facilities, all machinery used for cleaning, sorting, and packaging shellfish products is inevitably exposed to the seawater-infused environment. An aggressive atmosphere like that takes a heavy toll e.g. on regular conveyor drives. However, NORD DRIVESYSTEMS has recently introduced an innovative surface treatment to toughen drives for just such areas of operation.
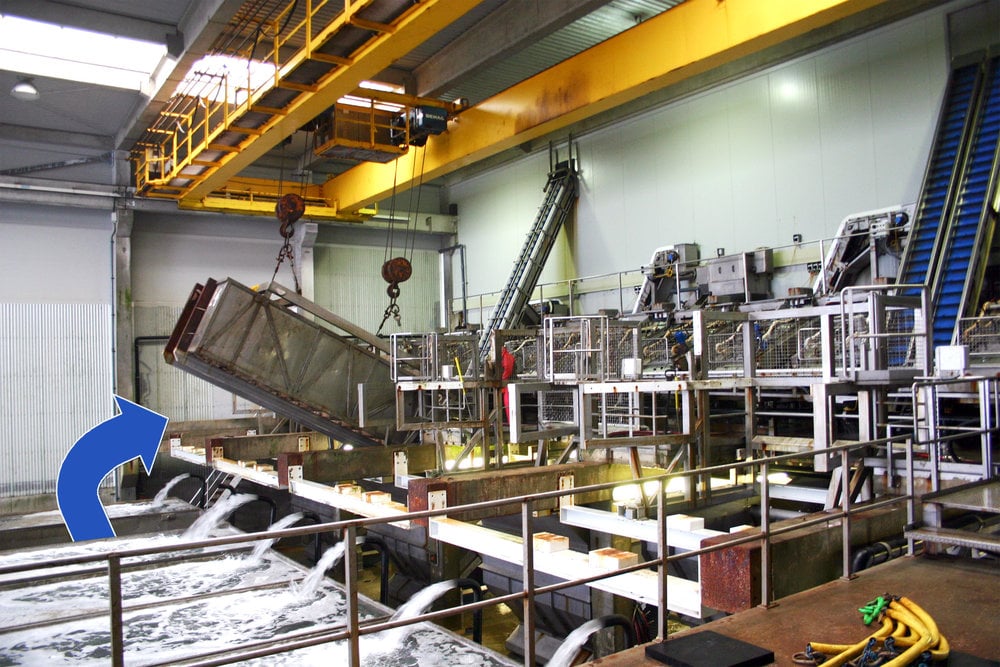
In Yerseke, a Dutch seaside village roughly one hour south of Rotterdam, shellfish has been the principal industry for almost a century and a half. Krijn Verwijs Yerseke B.V., a family business established here in 1880 as a breeding company for oysters, has developed over the course of time into one of the largest players in the European crustacean and shellfish market. Blue mussels are harvested in breeding grounds in the Netherlands, Ireland, the UK, and Germany. As these reach the factory directly by ship or in cooled trucks, they are put into large basins supplied with a constant flow of cooled, clean North Sea salt water. The containers are kept right next to the processing facilities inside the factory. The mussels then make their way through various stages in the factory: some further cleaning ensues, damaged and dead specimens are manually picked out, and the mussels are de-bearded. Soon enough, quality-controlled processed products can be packaged and sped away to the designated customer.
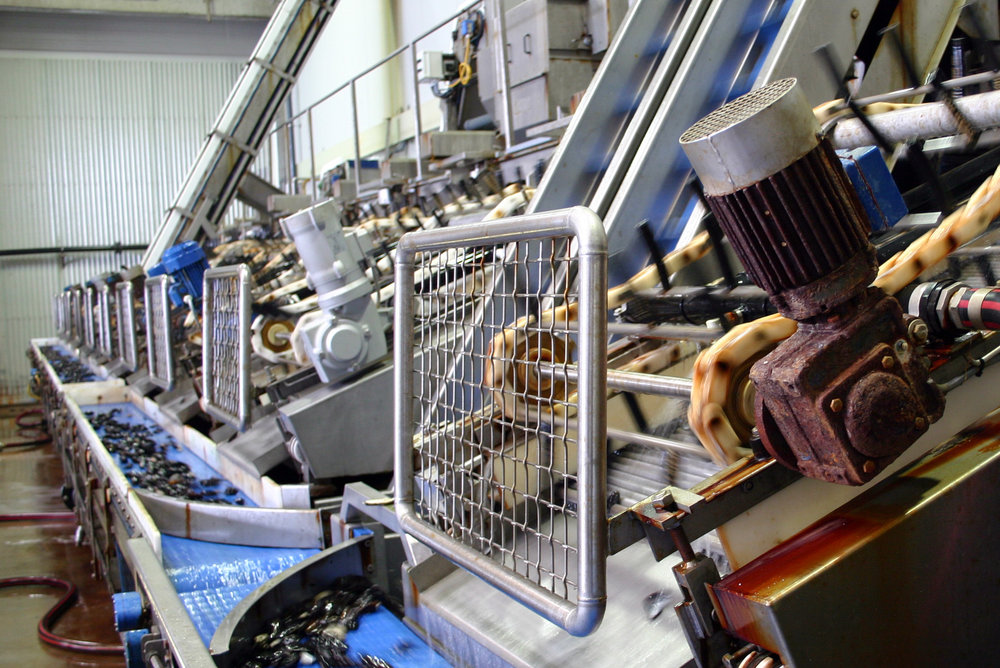
Illustration 2: There are hundreds of geared motors in the facility – Krijn Verwijs intends to gradually replace all with resilient NORD nsd tupH drives (second unit from the right)
Eaten away by salty air
Given the presence of the large containers full of salt water and the fact that the live mussels are conveyed wet as they come, every last corner of the factory is pervaded by a humid, salty atmosphere. This spells swift corrosion for all sorts of metal parts across process automation implements. In the case of the many 1.5 kW class geared motors driving the various conveyors, rusty spots first appear on brand-new systems in a matter of weeks. In the end, an ordinary drive unit’s life in this environment is spent after a year or two, and a new geared motor must be installed as a replacement. Little can be done to keep a drive in service much longer – with cast iron systems, even a protective coating or varnish is often eventually compromised e.g. by scratches, and will therefore only moderately delay the onset of corrosion. Stainless steel drives, the most obvious alternative, are unfortunately not suited to this application either, with the extra cost for such models not the only issue standing in the way. Practical cleaning routines are at stake as well: stainless steel units would require a significant cool-off period before every hose-down to protect them from excessive stress to the material, which would cause too much disruption to the factory operation as a whole. Dutch drive supplier Drive & Flow introduced Krijn Verwijs to a new approach to toughen drives for use in aggressive environments that was recently pioneered by NORD DRIVESYSTEMS, one of the global leaders in drive technology.
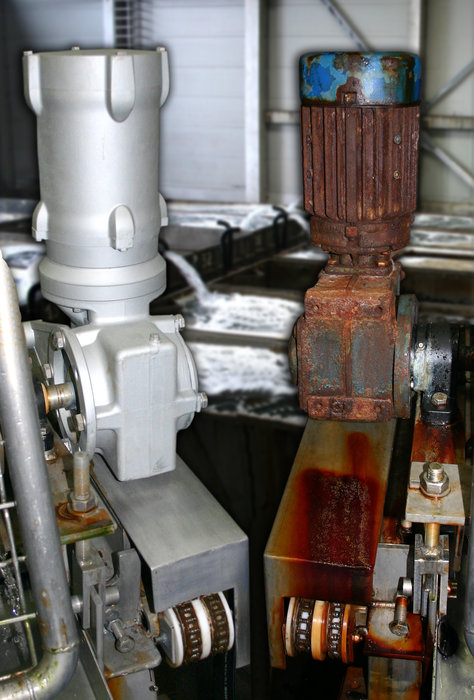
Illustration 3: While regular geared motors suffer severely in this environment (unit on the right, shown after about one year of use), NORD systems featuring nsd tupH surfaces evidently fare much better (unit on the left, shown after a few months in service)
Proven ingrained protection
NORD’s portfolio had been extended to include a broad range of drive systems with a specially treated aluminum surface promising to be much more durable under adverse conditions like the salty atmosphere at Krijn Verwijs. Though these geared motors come at a premium compared to the price of regular cast iron units, they will typically outlast the lifetime of a conveyor line as a whole, and therefore eliminate follow-up expenses for several replacement drives, not to mention all the necessary installation work. Test results proffered by NORD for drives with so-called nsd tupH surfaces already documented there was no visible corrosion after e.g. 1,000 hours of immediate exposure to salt spray. Krijn Verwijs opted to conduct their own hands-on testing nonetheless, all the better to ensure the real-life viability of this innovation. In spring 2013, the first nsd tupH geared motor was installed at the shellfish production facility. Its scratch-proof surface proved to be spectacularly resilient, showing hardly any sign of wear after several months of operation. “With standard cast iron geared motors, we had no choice but to swap out lots of units again and again and again, up to ten times during the usual service life of a conveyor line. Since there are so many drives in our factory, these replacements basically never stopped. It is such a relief that this new NORD solution means we no longer have to worry about drives all the time. In our factory, we expect nsd tupH systems to last at least five times as long as the old geared motors, if not longer,” says Bram de Visser, Technical Service specialist at Krijn Verwijs.
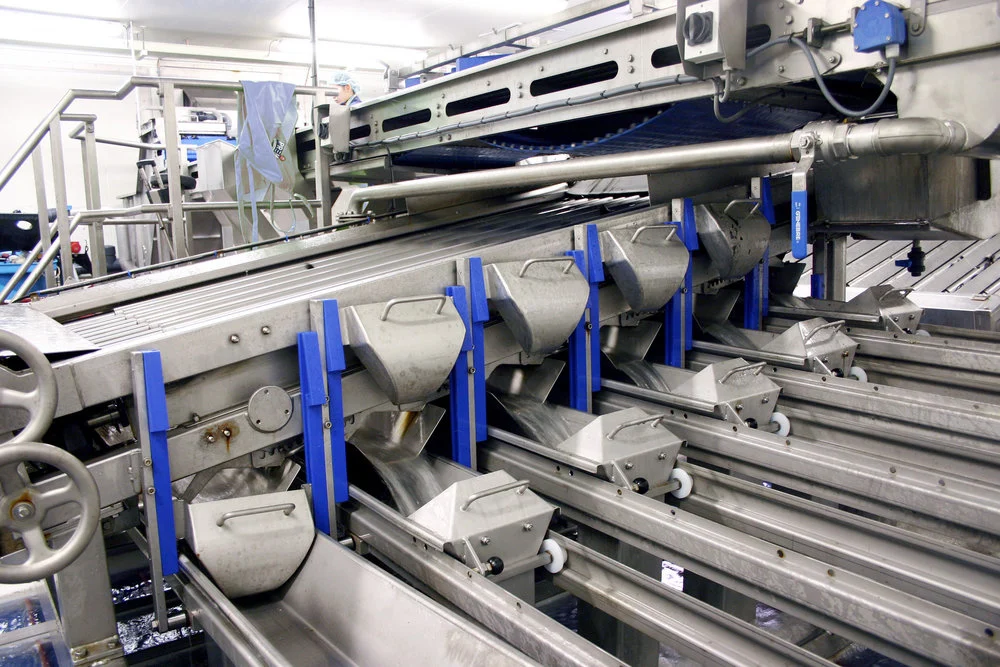
Illustration 4: After they are cleaned, products are sorted by size and weight
Imbued with superior resilience
The nsd tupH treatment is no application of a coating, but rather a surface conversion that produces a base layer that is permanently bonded to the substrate. Based on an electrolytic process, this treatment renders aluminum cases similarly unsusceptible to corrosion as stainless steel. The treated surface also becomes more than six times as hard as untreated aluminum alloy, and a thousand times as hard as paint. Featuring a very lightweight, compact, and self-draining design without indentations or dead spaces, drive systems with an nsd tupH surface can be easily washed down. They are impervious to e.g. common chemical cleaning agents used in many branches of industry – neither rinsing them with acids or alkaline solutions nor applying high-pressure cleaners will do any damage. Chipping obviously does not pose a problem either: unlike coatings, the nsd tupH treatment does not require any machining as a final step, so the aluminum surfaces are not exposed. On the other hand, for gear units featuring protective varnishes or e.g. a nickel or nickel/Teflon combination finish, there is always a risk that such layers may blister or peel off once they are scratched. In addition, the nsd tupH treatment is universally available for all NORD aluminum products. “The only complaint I have about nsd tupH technology is that it wasn’t available much earlier,” quips Bram de Visser. “That would have saved us so much time and money spent on maintenance and replacements.” A full transition is now underway in Yerseke: every drive that needs to be replaced at Krijn Verwijs in the months and years to come will eventually be swapped for an nsd tupH unit made by NORD. It will be a while until that process is completed, since the various conveyor systems in the seafood production factory are equipped with several hundred drives.
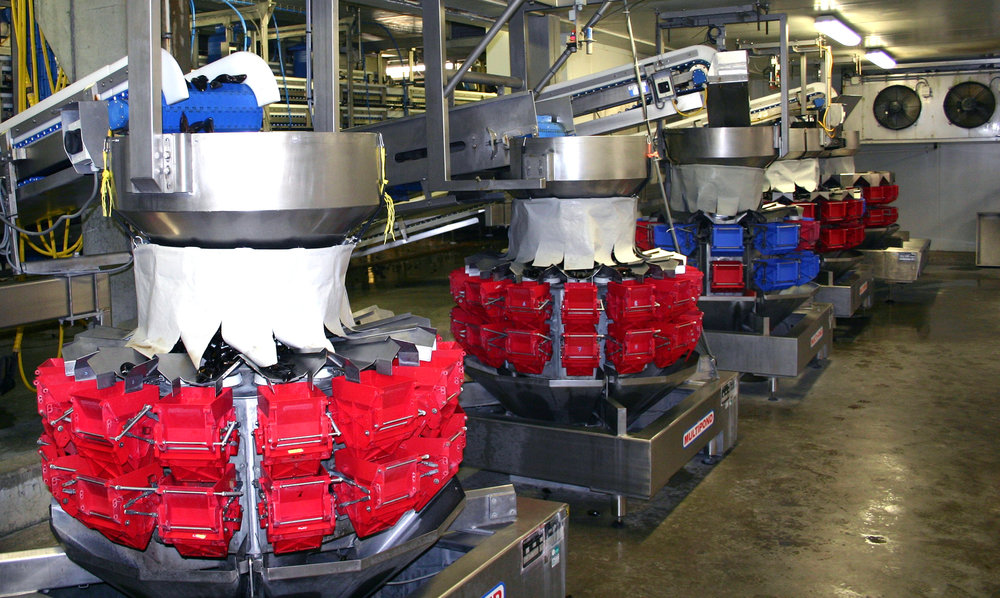
Illustration 5: Shellfish products leave the Krijn Verwijs facility either in wholesale packaging or retail trays