ACTIA ASSERTS ITS INDUSTRIAL FOOTPRINT AND INVESTS IN THE FACTORY OF THE FUTURE
It is in this context and to address the new challenges of its ecosystem that ACTIA is pursuing the transformation programme for its showcase industrial site: ACTIA Colomiers. This site already has a high level of industrial excellence combined with a very high level of certification and is part of a Factory of the Future approach which aims to continue the transformation plan initiated in 2015 by modernising, digitalising, automating, and securing this industrial tool.
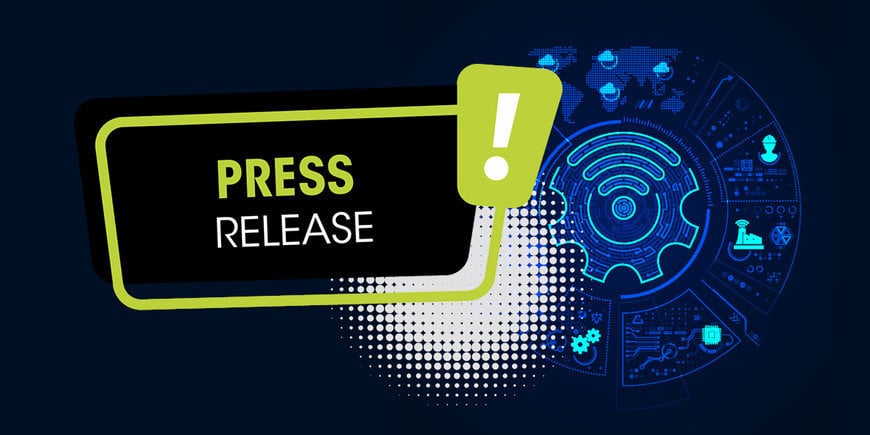
The current projects are also evidence of a forward-looking ambition:
The renewal of mass production ;
- The flow line set-up of complex production runs ;
- The configuration of the production area related to the space sector ;
- The acceleration of the World Class Manufacturing (WCM) excellence programme.
THE SYNERGY OF TECHNOLOGICAL AND INDUSTRIAL KNOW-HOW
ACTIA has been designing and developing its products in the group’s design offices ever since it was created. These are located in the direct vicinity of its production sites. ACTIA therefore manufactures the products developed by the 1,200 employees in the R&D teams.
The synergy of technological and industrial know-how strengthens the group’s operational agility in a market which is tending to reduce time-to-market and introduce new products, and which is experiencing a great deal of disruption related to geopolitics, the climate, health, or thesemiconductor supply chain crisis.
PRODUCING COMPLEX PRODUCTION RUNS.
To meet the demands of new markets such as New Space, ACTIA must be able to design and produce product batches in medium or small production runs with multiple variants.
The aim is to adapt production and assembly lines to product lines that may be smaller in quantity but are highly complex with a large number of variants. This requires a faster and reliable new product introduction (NPI) process.
The industrial vision of complex production remains the same within the ACTIA teams: to use flow production and, as in mass production, to improve the use of data already available in order to connect people, resources and systems. ACTIA is therefore strongly focused on digitalising its production methods.
FACTORY OF THE FUTURE : TOWARDS “PLUG AND PRODUCE”
Prior to the components crisis, ‘on-demand’ manufacturing was gradually replacing the building up of buffer stocks. This was in response to the reduction in time-to-market for new electronic products.
In an environment of component shortages, this agility is always put to the test and subject to the unreliable supply of electronic components, forcing a very rapid change in production on the same line.
This agility is based on the almost instantaneous transmission of data. It allows for greater responsiveness and optimised production: perfectly in line with market and customer requirements and regardless of the supply environment.
The challenge is to adapt the product, to customise it, while maintaining a single production line. So ACTIA is aiming for “plug and produce”, i.e., flexible production based on digitised and modular production units.
ACTIA’S DIGITAL MANUFACTURING
Accelerating industrial digitalisation within the ACTIA group gives structure to both the organisation and its methods in order to better position it at the core of the key objectives: customer satisfaction and industrial competitiveness. Digitalising the production chain is therefore at the heart of the interface between ACTIA and its customers. This is a necessary step to improve operational efficiency.
ACTIA DEPLOYS SIGNIFICANT DIGITAL TOOLS.
The adopted technologies help to optimise production as close as possible to needs and to anticipate constraints. Investments in digital tools are focused on collaborative platforms.
Following PLM (Product Line Manufacturing) deployment and ERP migration connected to the PLM, ACTIA is configuring an NPI (New Product Introduction) tool which is a major component of the MES (Manufacturing Execution System).This system is the driving force behind the Connected Factory and ACTIA’s next large-scale Factory of the Future digitalisation programme.
The MES programme will be based on:
- A Data Lake: which allows all production data, products, machines, people, etc. to be made available in real time.
- Artificial Intelligence: which is supplemental, in order to provide not only analyses and KPIs, but also predictions regarding flow and even problems which the production staff can use and, above all, avoid.
- The automation of certain processes, with the introduction of robots, AGVs (Automated Guided Vehicles) and 3D and X-ray automated optical inspection systems.
ACTIA CONFIGURES ITS FACTORIES IN “MIRROR” MODE BASED ON THE COLOMIERS FACTORY.
In the ACTIA Group’s industrial strategy, the synergy between all the factories spread across three continents is significant. This strategy of optimising industrial performance, in “mirror” factories, assumes a level of security that is suited to the means of collaborating and sharing data between the various production sites.
FACTORY CYBERSECURITY: A MAJOR CHALLENGE FOR THE PROGRAMME.
Producing communicating objects in connected factories is a daily challenge in terms of industrial cybersecurity. ACTIA designs and manufactures electronic products and communicating on-board systems in its factories for different business sectors, including the automotive, aviation, space, and energy sectors.
The rapid developments in these product families and systems involve:
- increased complexity of software functions
- the incorporation of numerous security features
- and ever-greater data processing.
In terms of cybersecurity, ACTIA’s Factory of the Future strategy is an extension of its overall approach to protecting all its assets. The challenge is to ensure continuous improvement in the security of the factory (ISO27001 certified) with regard to various risk categories, in particular risks related to cyber-attacks.
IMPROVING THE CARBON FOOTPRINT OF THE COLOMIERS FACTORY.
The factory’s eco-friendly perspective aims to improve the factory’s energy and environmental performance by reducing its carbon footprint as well as its energy consumption levels.
The energy mix is the distribution and weighting of the various types of primary energy for generating power that can be used directly, such as electricity or heat.
80% of the energy mix at the Colomiers site is distributed as follows:
– 60% of the site’s energy consumption is a result of manufacturing processes
– 20% of the site’s energy consumption comes from heating and cooling the premises.
ACTIA is therefore working on both of these optimisation drivers to improve the energy balance at its showcase site. By 2025, ACTIA aims to reduce its process-related energy consumption by 8% and its CO2 emissions by 10%.
ACTIA’S FACTORY OF THE FUTURE SOCIAL PERFORMANCE OBJECTIVES
Experts often equate the Factory of the Future with cooperation between people, robots and intelligent machines. These tools help employees work better and faster by taking advantage of advanced technologies; robots and cobots intervene to allow employees to focus on operations with higher added value.
The ACTIA factory’s social chapter goes beyond this purely technological consideration. For ACTIA, people really are a key factor in the Factory of the Future.
The plan includes measures to develop:
- employees’ skills
- their accountability
- their interest and versatility in the workplace.
This is one of the challenges of the WCM (World Class Manufacturing) programme deployed by ACTIA in the group’s various industrial sites. Used to ensure customer satisfaction and industrial performance, WCM manages and structures continuous improvement action plans with the teams in the field.
The digitalisation of production within the WCM is key to:
- Reducing human effort and moving towards the augmented operator: the robot relieves the operator of tedious and repetitive tasks so the person can concentrate on tasks with high added value.
- Data management.
- Training.
- Predicting future events via models.
True to its commitments and human values, ACTIA is incorporating this social perspective into its factory modernisation plan, with the aim of enhancing its employees’ skills, but also to maintain and develop local employment.
This plan illustrates ACTIA’s ambition for its Factory of the Future. However, although the business environment is quite positive and promising for the group’s activities, the crisis in electronic components is affecting the reconfiguration of the Colomiers factory and testing the entire organisation.
The ambivalence of this market environment reinforces ACTIA’s decision to continue its strategic investments in its production facilities. This strategy will enable it to cope with the changes in an increasingly technological, competitive, and diversified industrial world.
www.actia.com