Saint-Gobain 3D prints tooling for an elevated efficiency of its automotive production line
The French multinational Saint-Gobain, dedicated to the manufacture of glazing for multiple industrial sectors, has found 3D printing technology developed by the Barcelona-based multinational BCN3D to be the perfect ally for increasing the efficiency of its manufacturing processes.
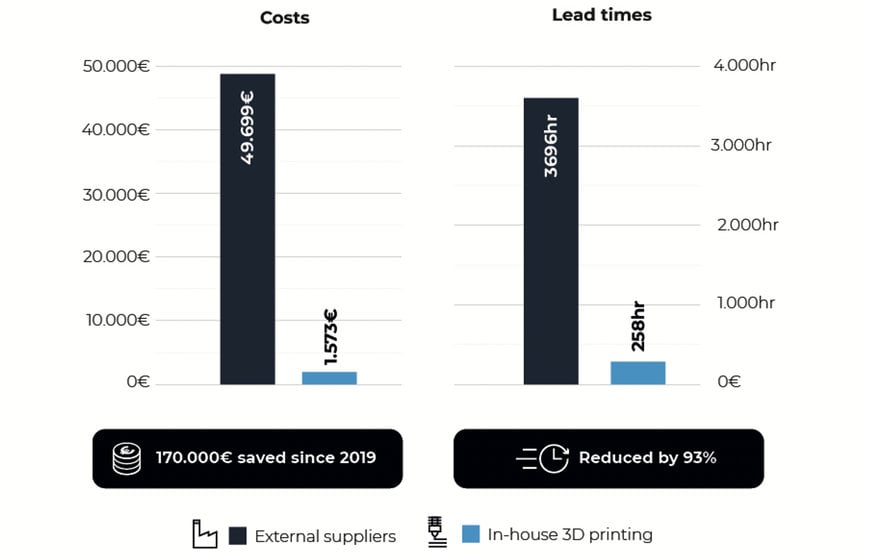
- At the French multinational's facilities in l'Arboç (Barcelona), 3D printing is used to manufacture tooling such as templates and positioning fixtures that contribute to more efficient glazing production lines.
- Since 2019, the automotive glazing manufacturer has saved 170,000 euros in its manufacture of said tooling thanks to the incorporation of BCN3D 3D printers.
BCN3D's 3D printers and various innovative technological solutions now enable Saint-Gobain engineers at its plant in L'Arboç, Barcelona, to significantly improve efficiency in the manufacturing processes of parts and components for its automotive customers including Daimler Mercedes, Stellantis Group, Volkswagen Group, Renault Dacia and Ford. By creating 3D printed tooling, the French giant's Spanish factory has improved and reduced costs and times by manufacturing tooling implemented in automated lines.
This success story exemplifies how BCN3D's 3D printing technology can be of great assistance to the automotive sector and consolidates the additive manufacturing solutions manufacturer based in Gavà, Barcelona, as a strategic partner of this industrial sector worldwide. This case shortly follows the incorporation of its equipment in the production plants of Seat and Nissan in recent years.
Since 2019, Saint-Gobain's Sekurit business unit at the L'Arboç plant - where 19 million different automotive glazing units (backlites and sidelites) are produced per year - has incorporated 3D printing technology after outsourcing for years the manufacture of tooling that it entrusted to mechanized processes with much higher costs compared to 3D printing.
The incorporation of this additive manufacturing technology has since enabled Saint-Gobain's Spanish plant to save around 170,000 euros and reduce its lead times for tooling by 93%. The 3D printed parts take the form of tools, jigs, and fixtures all the way through to quality control.
"At Sekurit we have been manufacturing automotive components for 90 years. Thanks to 3D printing, we have experienced a significant cost reduction and a faster workflow adapted to our needs in the manufacture of tooling and tooling since we incorporated this technology compared to external suppliers we used in the past," explains Angel Salas, Saint-Gobain's maintenance engineer at the Barcelona factory.
3D printing revolutionizes production at Saint Gobain
Saint-Gobain's Barcelona plant has incorporated 3D printing technology (including IDEX Technology) in its workshop with several BCN3D Epsilon W50 series printers and Smart Cabinets, making it easier for the multinational to develop new ideas, easily and conveniently create new prototypes in a shorter period of time compared to other machining technologies, and carry out tests and end-use parts in a matter of days, all while maintaining the highest quality.
Additive manufacturing integrated into automation
Saint-Gobain integrates additive manufacturing into tooling that facilitates the production of rear and side panels for vehicles. The process begins with a fully automated robot line: the glazing is cut to shape, the sides are smoothed and designated aesthetic details are added.
The glazing is then collected and placed in an oven to create the curves. Fresh from the furnace, the glazing is checked for dimensions and quality, and then sorted into pass or fail for manual checking.
www.bcn3d.com