www.industry-asia-pacific.com
04
'20
Written on Modified on
Overcoming the crisis: COVID-19, the automotive industry and the potential of additive manufacturing
Every day, industries across the world face unique and interlinking challenges as a result of the COVID-19 crisis.
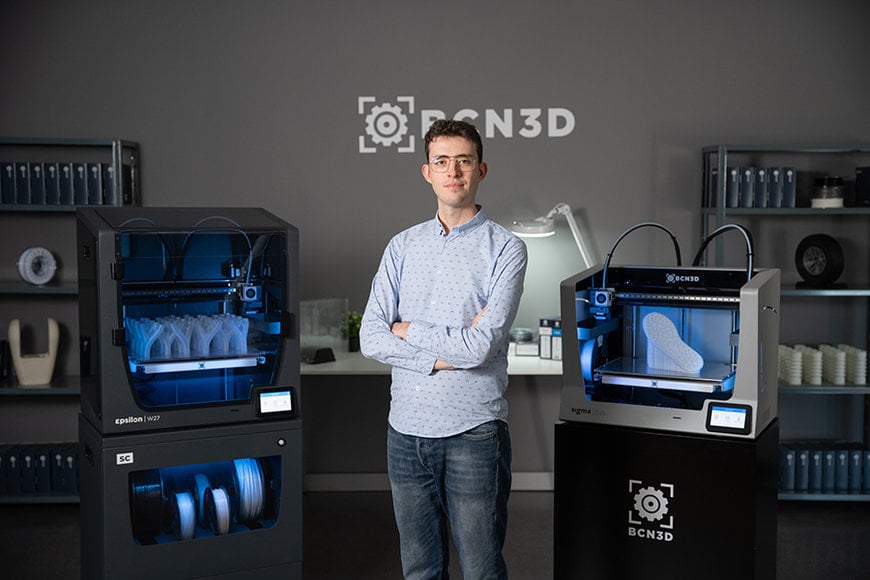
For the automotive industry, it’s a complex picture in which there are both hurdles and opportunities. In this feature, Eric Pallarés, Chief Technology Officer at BCN3D, considers the impact of this tumultuous year on the automotive industry and how additive manufacturing can help.
John Allen Paulos, a mathematician and Temple University professor, once said that ‘uncertainty is the only certainty’. It’s a phrase that the majority of us have become regrettably familiar with in 2020. When the COVID-19 pandemic swept across the globe at the beginning of this year, the impact on the automotive industry was stark. In China, part exports were severely disrupted. There were large scale manufacturing interruptions across Europe, and in the United States assembly plants shut down overnight. By May, commentators were noting that the industry was expected to realign in monumental and profound ways. Even as the world shifts into some semblance of a new normal, the issues and financial repercussions of this crisis still loom.
Interestingly, the pandemic came at a time when the industry was already battling with trends that were set to alter it in profound ways. In urban centres, vehicle ownership was falling lower down the priority list, with car sharing, ride hailing and public transport proving to be king. We now live in a world acutely tuned to the climate crisis, and pushing for the faster adoption of electric vehicles and greener energy. These are monumental shifts in mobility habits that the automotive industry was adapting to when the pandemic once again altered the course.
According to Deliotte, the need for physical distancing and health concerns have forced a large number of consumers to change their opinions on mobility. Many more now think that vehicle ownership is valuable (79% of consumers in France, 74% in the United States, 69% in the United Kingdom, and 63% in South Korea). A report recently produced by Britain’s RAC has even showcased that the pandemic has actually put back attitudes to public transport by two decades. Given all these rapid shifts, manufacturers are faced with the challenge of preparing for a future where resilience, agility and adaptability will be key.
So, where does additive manufacturing fit into all this? Well, this particular crisis has thrown light onto the unique benefits of additive manufacturing. Many of which are exactly what the automotive industry needs to recover, from building a resilient supply chain, to maintaining and optimizing the production line, and ensuring versatility.
Early on in the crisis, additive manufacturing proved itself to be a technology adept at overcoming supply chain issues, and offering the efficiencies of localised and decentralised production. We have seen fantastic examples of applications from our own customers in which in-house 3D printing has made on-demand production of tools, jigs and fixtures a possibility. Take for instance, the creation of a support for AGVs (autonomous robots for the supply line). Such supports are essential, as they help to significantly reduce the incidences of these robots and ensure they perform.
Inefficient performance can often be the difference between a supply line being profitable or not. Traditionally, such supports are machined in nylon via a slow and expensive process. 3D printing the supports in-house removes the need for outsourcing and is dramatically faster than traditional machining. Delivery time for an outsourced support might take up to 25 days, whereas producing the support using an in-house BCN3D Epsilon in TPU material would only take 12 hours. A compelling business case, particularly in a year in where access to traditional supply chains have often been impossible.
Turning to additive manufacturing to produce essential tools, jigs and fixtures has impressive cost efficiencies too. Cost cutting is nothing new, but it is now more important than ever. The previously mentioned AGV support? Traditional machining and outsourcing would cost around €39 for five parts, whereas with 3D printing, costs instead sit at about €9.50. Cost efficiencies go beyond the removal of outsourcing. One such example that springs to mind is the creation of robot arm clamps on demand. Our customers have often turned to machines like the BCN3D Epsilon W50 to 3D print these clamps in industrial-grade technical materials, such as PAHT CF15, when and where they are needed. By creating such applications in-house and on-demand, the need for physical stock, and the cost and supply chain issues that come with it, are eliminated.
In discussions with our customers, from BMW to SEAT to Nissan, it’s become clear that manufacturing centres with the ability to be versatile are the ones that will thrive. Again, to go back to the AGV support example, each one will be different depending on the type of vehicle being manufactured, but this is another challenge in-house 3D printing can help to overcome. By integrating industrial power 3D printing on the work bench, manufacturers can seamlessly produce multiple variations of the support on demand and dependent on production line needs.
In a world in which consumer attitudes to vehicle ownership is changing rapidly, and generally overall demand for new vehicles is down, a production line which is adaptable is key. It could, for instance, enable an easier pivot to the design processes required for electric vehicles. Or, allow vehicle manufacturers to offer the level of customization normally reserved for higher end vehicles to other specifications with relative ease.
Evidently, the challenges that the automotive industry faces are vast, but they are not without opportunity. At the heart of additive manufacturing techniques is a freedom of design and agility that is not always offered by other technologies. We’ve explored how this can help create advanced tools, jigs and fixtures that are cost efficient, unhampered by supply chain issues, and can help to ensure an optimised and efficient production line, all whilst being completely integrated into a companies existing workbench. Now is the time to explore the potential of such technologies. Together, the automotive and additive manufacturing industries can bounce back from this crisis, stronger than ever before.
www.bcn3d.com