www.industry-asia-pacific.com
25
'14
Written on Modified on
Taken to new heights: Industrial gear units from NORD complete heavy workload at a reservoir project
Bargteheide – Swiss energy supplier Axpo is close to finishing the demanding large-scale “Linthal 2015” construction project: Switzerland’s largest hydroelectric undertaking will increase the overall output of the existing Linth-Limmern power plants from 480 MW to 1,480 MW. A new underground pumping station was created to pump water from the Limmernboden reservoir at an altitude of 1,860 m above sea level into the Muttsee lake about 600 m higher up. This elevation difference will be used to produce hydroelectric power on demand. The heart of the project in particular – the underground center for the new pumped storage hydroelectric power station – required gigantic efforts. At an extreme incline of 45 degrees and a height difference of approximately 180 m, conveyor systems in a sub-station transported 500 t of excavated material per hour, around the clock. On a second conveyor belt, the crushed material was transported up to the gravel plant where it was stored or processed for further use. For a total of three years, these conveyors were driven by NORD industrial gear units and transported approximately one million tons of material.
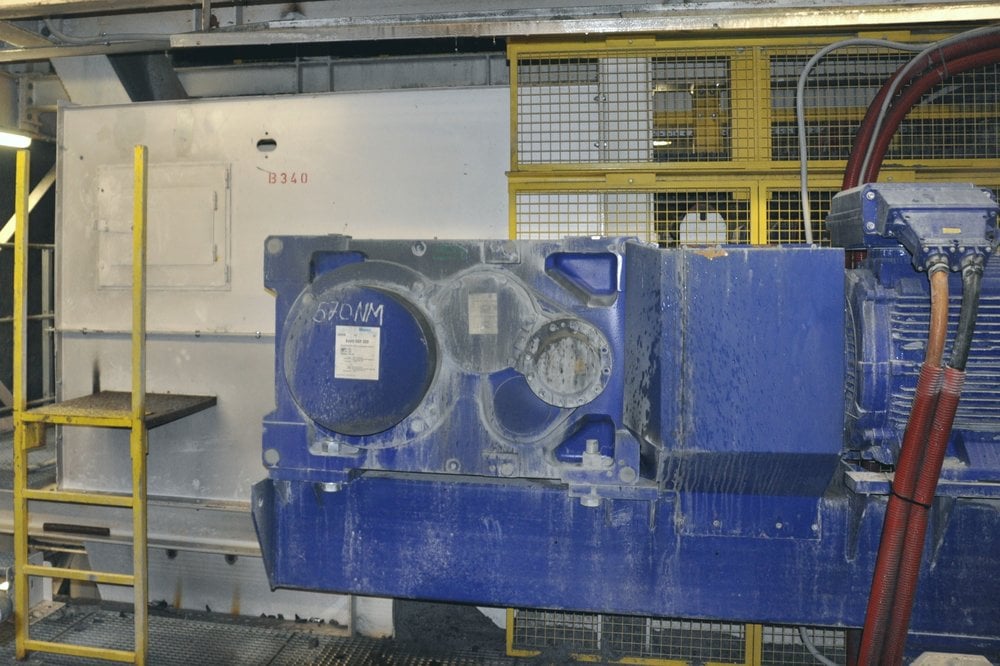
After the completion of the conveying tasks, the NORD industrial gear units were disassembled by plant manufacturer Marti Technik AG, and are now awaiting their next assignment. Ernst Kuster, head of conveyor maintenance at Marti Technik, says: “In compliance with the instruction manual, we changed the oil once, but that was the only maintenance measure we had to take over the course of three years. The NORD gear units performed brilliantly.” The industrial gear units qualified for this massive construction project thanks to the tried-and-tested UNICASE design: this one-piece housing block integrates all bearing seats. UNICASE housings are manufactured on state-of-the-art CNC machines in a single setting. The concept ensures high precision, rigidity, and strength, with no joints between the output side and the gearcase which are subject to radial forces or torque. Moreover, the overlapping bearing offset allows for more compact gearcases and larger roller bearings that allow for a long operating life.