www.industry-asia-pacific.com
16
'21
Written on Modified on
IMPAQT makes a world of difference
IMPAQT’s software power impresses experienced processors.
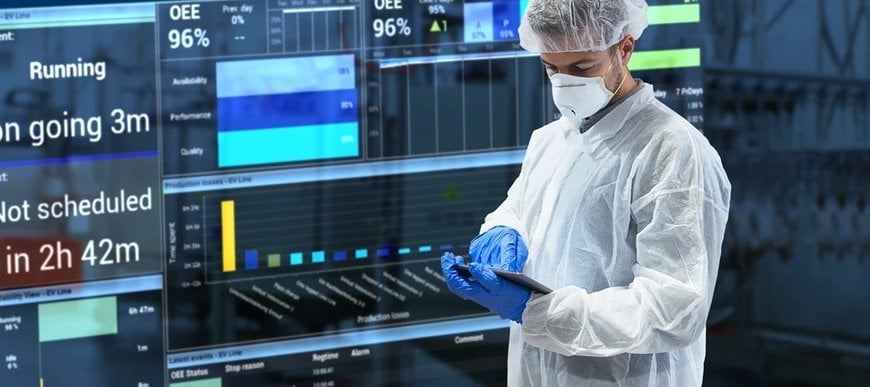
The possibilities offered by IMPAQT software are enormous. Experienced processors find it an extremely powerful tool that makes things they didn’t dare dream of come true. They’re particularly happy to see that IMPAQT reduces their downtime. They’re also pleased with being able to tailor their IMPAQT software to their own needs and requirements.
Overall Equipment Effectiveness (OEE), used across all manufacturing industries to measure efficiency, typically splits the measurement of the productive time into availability, performance and quality. 100% availability, or uptime, means that a manufacturing process is always available without unplanned stops. 100% performance, or throughput, is defined by comparing the theoretical maximum value with actual results, including why and where performance losses have occurred. 100% quality means that the production process doesn’t have any quality loss at all with no one-leggers, dropped products or veterinary rejects.
IMPAQT impresses
IMPAQT brings processors new possibilities they never had before. László Bárány puts it this way:
“We are obviously keen that our equipment gives of its best at all times. With IMPAQT we can focus immediately on problems causing a drop in yield or quality. Our technical people have an invaluable tool at their fingertips. They can do their crucial job even more effectively.”
-László Bárány, Managing Director of Master Good in Hungary
IMPAQT indicates the reasons
Processors usually find it hard to track down the cause of a line stop. But that’s now a thing of the past. They’re extremely happy that IMPAQT not only immediately signals a line stop but also shows the reason for it. Robert Duda says:
“IMPAQT allows us to see exactly in real-time what events occurred during the operation of the line. It has become a lot easier to detect damaged trolleys, for instance. We can resolve such issues much earlier than before, which really minimizes our downtime. At one time the line kept stopping, although the operator panel of the control box displayed no error. Each time people had to wait for the line to be restarted. We checked in the event log to see what had stopped the line and IMPAQT pinpointed the cause immediately. This was a damaged contact in the safety switch. Oxidization was causing line vibrations to disconnect the safety circuit each time for a very short while. It was good to find this out, because it saved us a lot of trouble.”
Robert Duda, Application and Maintenance Manager at Cedrob in Poland
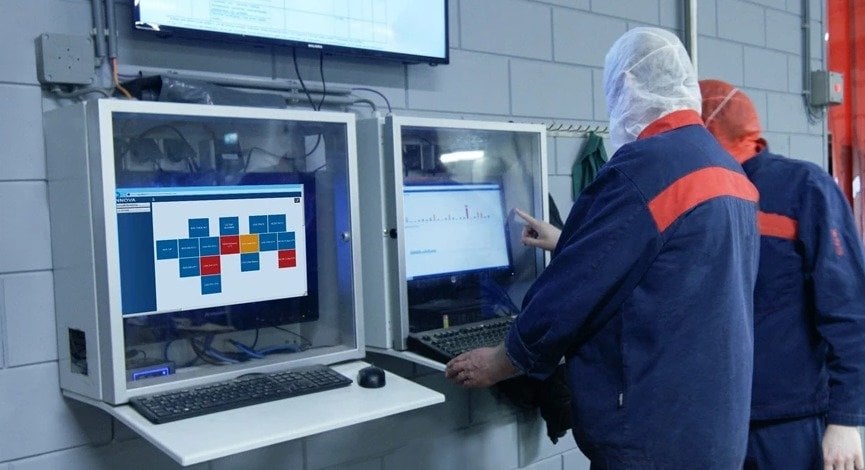
IMPAQT bases its findings on facts
Processors are pleased with the positive effect of IMPAQT in that decisions no longer have to be based on gut feelings of people on the factory floor. Where operators might think that they have found the cause of an issue, IMPAQT bases its findings on facts only and sometimes proves them wrong.
jan Legters gives an example:
"We had a nice discussion with our evisceration operator, who has thirty years’ experience and who refused to believe that unit 9 of the Nuova wasn’t functioning as well as it could, which was picked up by IMPAQT. He was convinced that it was pure coincidence each time the machine didn’t perform as it should. Eventually, I asked him to exchange units 9 and 10 and only then, after having looked in my system, did he admit that IMPAQT was right."
-Jan Legters, Esbro plant manager, the Netherlands
IMPAQT improves the process
With IMPAQT, an alert no longer causes panic. On the contrary, if everybody on the factory floor and in the control room knows exactly what to do, there is a chance to improve the process still further. The exact reason of an alarm can be analyzed quickly and future alerts can be prevented. As a result, the process is optimized. Jan Legters again:
"Usually operators don’t register what happens during a line stop. They just want to get the line running again as soon as possible. They see a trapped chicken in the eviscerator, take it out, reset the machine, and when everything seems okay, it’s chop-chop, up and running again. But that doesn’t help us improve the process, it’s just reacting to incidents. Using IMPAQT, I can prove that the chilling tunnel stopped at 10:22 with the eviscerator following 12 seconds later. Therefore, a chilling tunnel failure caused the standstill and we need to take a look there to improve our process."
Jan Legters, Esbro plant manager, the Netherlands
www.marel.com