www.industry-asia-pacific.com
22
'20
Written on Modified on
New GEA Upgrade Kit digitizes functionalities of marine separators
GEA automates the functionality of its separators for marine applications with a new Upgrade Kit.
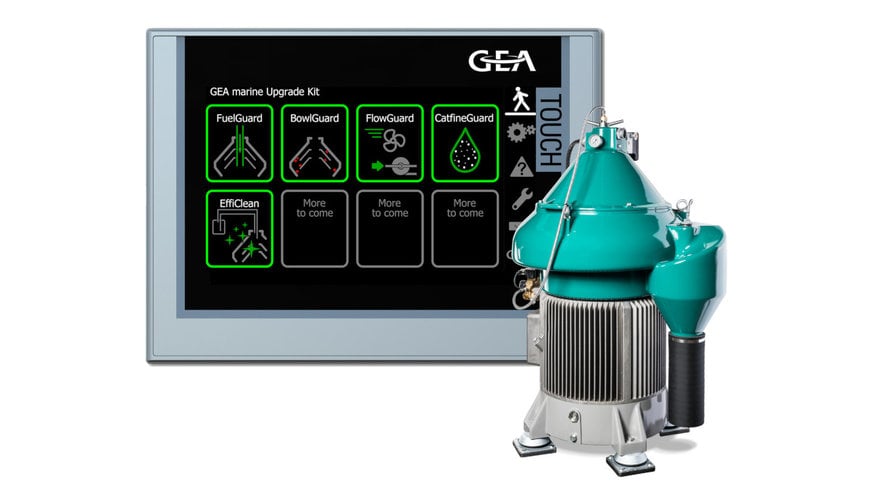
For GEA customers this means cost savings, safe operation and an improved CO2 balance for their plants. The new hardware and software are available as a retrofit solution for OSC, OSD and OSE separators. Currently a large liner shipping company is already retrofitting container ships with the GEA marine Upgrade Kit. GEA also announced that the Upgrade Kit will be optional included in the scope of supply of newly installed GEA marine Separators.
Ideal combination of innovative software and proven separation technology
The new GEA marine Upgrade Kit digitally controls several separation processes in parallel. Five so-called "guards" monitor and control important functionalities.
FuelGuard - automated way to reduce fuel loss
Fuel is a critical cost factor in shipping. The FuelGuard reduces fuel loss during separator bowl emptying by precise, volume-based and fully automatic dosing of displacement water. Only a sensor and integrated software are required. The amount of fuel saved, calculated on a fleet of 50 container ships, is impressive. Saved 686 tons is not only a large number, but also represents a significant reduction in operating costs.
BowlGuard - a smart solution to reduce disposal costs
The BowlGuard optimizes separator bowl ejection. The sludge volume is reduced by up to 50 percent, disposal costs are minimized. The challenge is solved by actively controlling the ejection interval depending on the bowl volume. The technical prerequisite for this solution is an activated FuelGuard package.
FlowGuard - Fuel processing on demand
Many separators run at full capacity, even though the actual consumption of the running ship engine varies depending on the operation mode. The FlowGuard software adjusts the flow rate of the separator to the needs of the ship's engines. This means that only as much fuel is processed as is actually required by the ship's engines. This ensures very efficient separation, saves energy and reduces CO2 emissions. In addition to the FlowGuard software, only a frequency-controlled feed pump is required. The saving of CO2 emissions is great (calculated again on 50 container ships): 910 tons less CO2 emissions are emitted into the atmosphere.
CatfineGuard - finest fuel at the push of a button
Cat fines (catalytic fines) are hard aluminum and silicon oxide particles. With the help of the CatfineGuard, these tiny particles with a size down to three µm are filtered out. This is done by hot separation at temperatures of up to 110 degrees Celsius or by reducing the flow rate of ultra-low sulphur fuel oil. This solution requires a frequency-controlled feed pump and, if necessary, heat-resistant seals for hot separation.
EffiClean - best CIP cleaning
The manual cleaning of the disc packs of mineral oil separators used to be a laborious, time-consuming and also dirty affair. Dismantling is also often necessary. With EffiClean, separator disks can be cleaned in only 20 minutes - instead of the usual eight hours - depending on the degree of contamination. The system consists of a cleaning unit and a highly effective yet environmentally friendly cleaning agent. The cleaning process can be performed directly at the machine. It is no longer necessary to disassemble the bowl. The amount of work is reduced by up to 95 percent compared to manual cleaning. With a minimal footprint, the mobile unit fits into even the smallest of spaces and the robust stainless-steel construction can withstand the demanding conditions on board.
Further guards for even more customer benefits
GEA, the company announced, will continue to work systematically on the development of digital functionalities for its separators. The GEA marine Upgrade Kit with software and technology can be retrofitted. Thus, the development and implementation of further guards is already being worked on.
www.gea.com