Transform Preventive Maintenance into Predictive
In a rapidly changing world and with the availability of Industrial Internet of Things (IIoT) solutions and services, the food industry is faced with some key digital transformations. The JBT version of IIoT is called iOPS and we are excited to have the digital tools to further improve our customers’ production lines with this performance optimization technology. The technology, which allows for connected equipment and operation monitoring, provides food manufacturers with new and unique possibilities to ensure sustainable and profitable growth through insights and proactive actions that would not have been possible to achieve in a profitable way before.
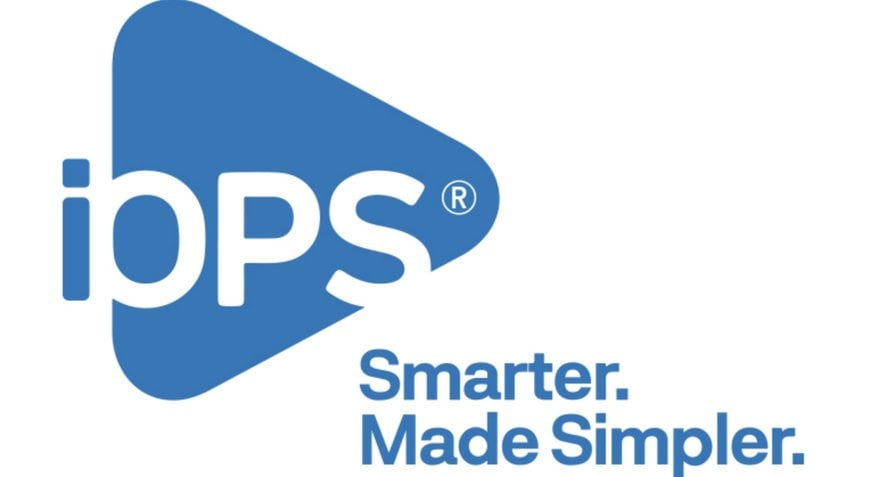
With the ongoing COVID-19 outbreak limiting our travel and access possibilities, many businesses are now looking to adopt to new technologies faster than they might have planned, acting as a boost for digital, virtual and remote innovations.
Greater production efficiencies
JBT’s iOPS makes use of collected real-time data providing customers a better view of their operation and supports in planning preventative maintenance well ahead of time.
By collecting and learning from real time data from systems and machinery, iOPS can detect potential issues before they become problems and even improve the overall efficiency of operations.
"Today, most maintenance is preventive or reactive, but not predictive."
The technology enables customers to gain a far clearer idea of the true state of their Overall Equipment Effectiveness (OEE). Jean Bülow, JBT’s iOPS manager, explains: “Today, most maintenance is preventive or reactive, but not predictive. By employing remote equipment monitoring we can foresee issues ahead of their occurrence, thereby saving money and time. This allows us to move from measuring a single parameter to proactive actions based on trends and expert analysis.”
Jean continues: “Our support team transforms the valuable data into supported advice based on know-how and trends, allowing us to generate alarms and act before a breakdown or premature wear becomes a fact.” Jean and his team are working continuously to move the technology from a technical platform to a value adding solution for our customers. “We see a lot potential and areas where we can use the data, and I’m sure we’re only at the start of a big transformation,” he says. “Within the area of food production, powered by intelligent data analysis and other advantages like re-use product data from PLM or using AR/VR technology, IoT will bring a lot of advantages to our customers and in the end the consumers.“
Act faster through predictive data
The next step is to act predictively and being able to adjust and change parts exactly at the right time. “By predicting, I envision that this technology will allow us in the near future to act faster when we see a failure is about to hap-pen,” Jean explains. “We will be able to optimize our efforts, such as deliveries of spare parts and the employment of field service engineers, and thereby shorten the resolution time on customer site and schedule replacement work in advance to when it best fits production cycles.”
Proactive means taking steps and replacing parts before machinery breaks, predictive means doing these things when conditions are optimal, i.e. before technical problems arise and at exactly the right time to get the most out of the investment. By making sure problems are tackled in time and avoiding parts being changed earlier then necessary it optimizes the total cost of ownership.
Optimization all over
With the increasing need to maintain high food standards, integration of iOPS can assist in improving food safety and energy savings. Concentrations of cleaning chemicals as well as cleaning water volume and temperature are examples of things we can measure and document. This provides you with the reassurance that cleaning procedures are being followed, and potential bacterial growth issues prevented. Moreover, iOPS technology greatly helps reduce waste, cost and risks at all stages of the production process.
With the onset of the COVID-19 pandemic, and greater numbers of companies moving to remote working as a result, iOPS integration can provide an overall, accurate picture of food processing operations without always having to be there in person.
iOPS is an Industrial Internet of Things performance optimization platform
- A secure big data analytics technology that gathers and analyses your JBT equipment and process performance in real time.
- A system that can inform your people when action is required or automate that action for lightning-fast response.
- A solution that will maximize uptime, productivity and profit, painlessly.
- Removes the necessity to train your people to install or run it. We handle everything.
Maximize
- Equipment uptime
- Profit per machine
- Labor productivity
Minimize
- Equipment downtime
- Maintenance expense
- Cost of ownership
- Labor shortage/turnover impact
Realize
- Maximum ROI
- Optimum business results
- The promise of Industry 4.0
A solution that will maximize uptime, productivity and profit. Painlessly.
www.jbtc.com