www.industry-asia-pacific.com
02
'19
Written on Modified on
Lonati Reduces Product Development Cost by 50% with Selection of 3D Systems’ Additive Manufacturing Solutions
3D Systems’ new Selective Laser Sintering (SLS) & Figure 4® platforms continue to build momentum, transforming Lonati’s machinery production workflow.
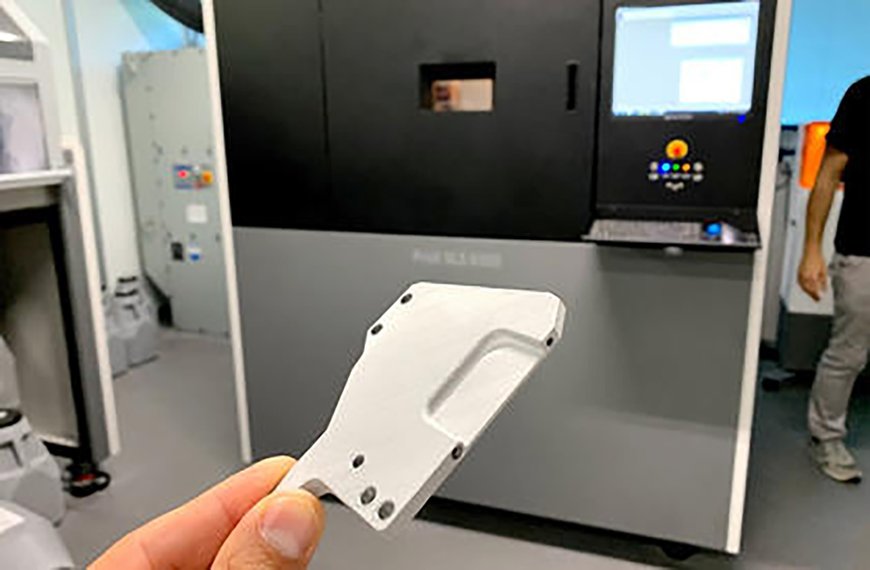
Lonati SPA, headquartered in Brescia, Italy, is a 150€ million global textile machinery manufacturer with more than 70 years’ experience. They are viewed as an industry leader that is constantly looking for ways to improve their processes to provide high quality, reliable products. The manufacturer produces 8,000 machines annually for 60 countries.
The machinery Lonati creates requires extremely precise parts with very thin walls that can function at rapid speeds. They looked to 3D printing to enable production of high quality, precise and reliable components for its machinery.
“We work in a highly competitive global market,” said Marco Gavazzi, senior R&D designer, Lonati. “To remain an industry leader, we are constantly searching for new ways to deliver the best products possible. The machinery we produce undergoes highly-pressured pneumatics and we need to produce parts with the highest standard of mechanical properties to withstand these stresses. After multiple tests against similar products, we found the best results using 3D Systems’ solutions.”
Lonati is using 3D Systems’ ProX SLS 6100 for prototyping as well as production of jigs and fixtures. They are printing final parts for assemblies using a combination of the ProX SLS 6100 and Figure 4 Standalone using both DuraForm® ProX AF+ and Figure 4 TOUGH-GRY 10. In a side-by-side comparison with other currently available materials, Lonati has found that the 3D System’s materials have a 2X improved tensile strength, which is critical for durability in high stress environments.
“Using 3D Systems’ solutions as part of our product development cycle, we are realizing tremendous efficiencies,” said Michele Faini, designer, Lonati. “We initially purchased one 3D printer to produce one component for our machinery.
However, because of the results we’re seeing, we have not only expanded to additional printers and materials, but also are creating more parts and assemblies. We’re fortunate to have partners like 3D Systems and 3DZ who are providing unparalleled applications expertise and support.”
“Lonati is a leading innovator in their category,” said Matteo Marcellini, channel manager, 3D Systems. “The way they have incorporated additive technologies into their production workflow and the results they are realizing provides compelling proof that 3D printing technology can meet high quality standards with improved efficiencies – all at a reduced cost. I’m inspired by our collaboration, and look forward to helping Lonati continue to expand AM’s role in its business.”
Ivan Zannol, 3DZ country manager added, “It’s very motivating to see the progress Lonati’s R&D team is making on a weekly basis. The experience of partnering with 3D Systems, and our collaboration with Lonati to design the right solution to meet their application needs, is very rewarding.”
www.3dsystems.com