www.industry-asia-pacific.com
24
'19
Written on Modified on
EV and Hybrid automotive manufacture benefits from Renishaw’s Equator™ gauge
When you visit Renishaw at EMO Hannover 2019 you will see multiple Equator systems gauging a range of electric vehicle (EV) and hybrid engine and transmission components.
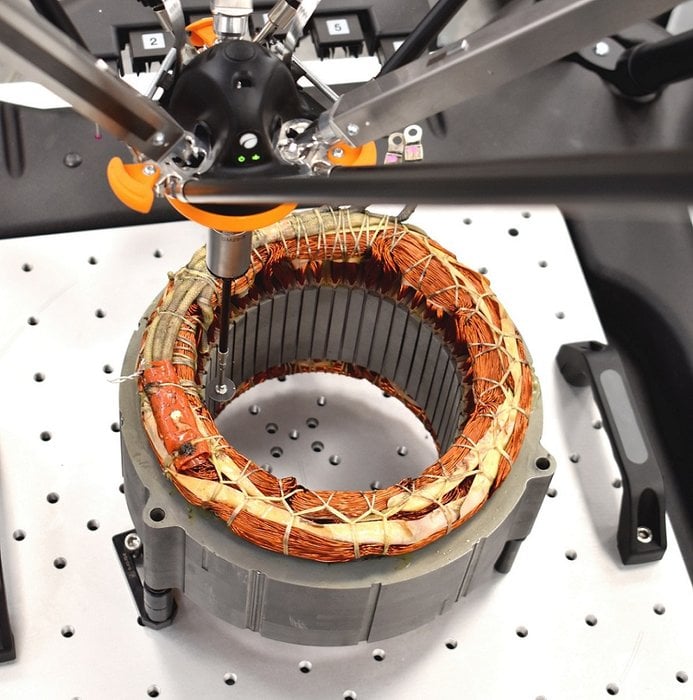
Significant investment in research and an increase in EV production has generated additional inspection requirements, which is where Equator gauging systems come into their own. This is backed up by a network of experienced application engineers, and served by software and hardware options applied to the needs of each type of process.
Proven capability on EV parts
EV motors, generators, transmission gears and casings – all examples of parts where production lines and cells now rely on the process control capabilities delivered by the Equator gauging system, at the point of manufacture.
Motor stators are a prime example – the high-speed scanning capability of Renishaw's SP25 probe used by Equator systems, coupled with Renishaw's powerful MODUS programming software, is ideal for assessing the demanding size, position and geometric tolerances on the ID and concentricity of an assembled EV stator – critical to guarantee motor efficiency.
The same Equator system can also use a Renishaw TP20 touch probe to collect single point data at a rate of up to three points a second – perfectly suited to gauging the relative positions of multiple edge points on a stator lamination plate.
Direct process control where it matters
IPC (Intelligent Process Control) software, developed with help from many end users across multiple industries, is an optional feature available on all Equator systems. This software allows constant monitoring and automatic adjustment of machining operations, keeping part dimensions close to nominal and within process control limits. This correction of process drift improves part quality and manufacturing capability, thereby reducing scrap and quality costs.
Automated cells versus manual gauging stations
Equator gauges can be quickly configured to meet the same application demands of dedicated gauging systems. With the reduction in automotive design lifecycles in recent years, fast and efficient re-deployment of Equator gauges to new lines and cells is a major advantage over part specific gauges which require time consuming redesign, costly rework or being scrapped altogether.
In addition, with increased demands for factory automation, Equator machines are perfectly suited for integration with robots and conveyors. The new EQ-ATS (Equator Automatic Transfer Systems), for Equator 300 and Equator 500, allows parts to be loaded at the front of the device, and transferred in and out of the measuring volume under automatic program control.
In some situations, particularly with very harsh environments, Equator systems are placed in an optional enclosure; an EQ-ATS system may also be fitted so that the parts can be loaded safely and easily outside of the machine volume.
www.renishaw.com