Developing a Trained Workforce for the Plastics Industry
Finding skilled workers in the plastics industry is challenging.
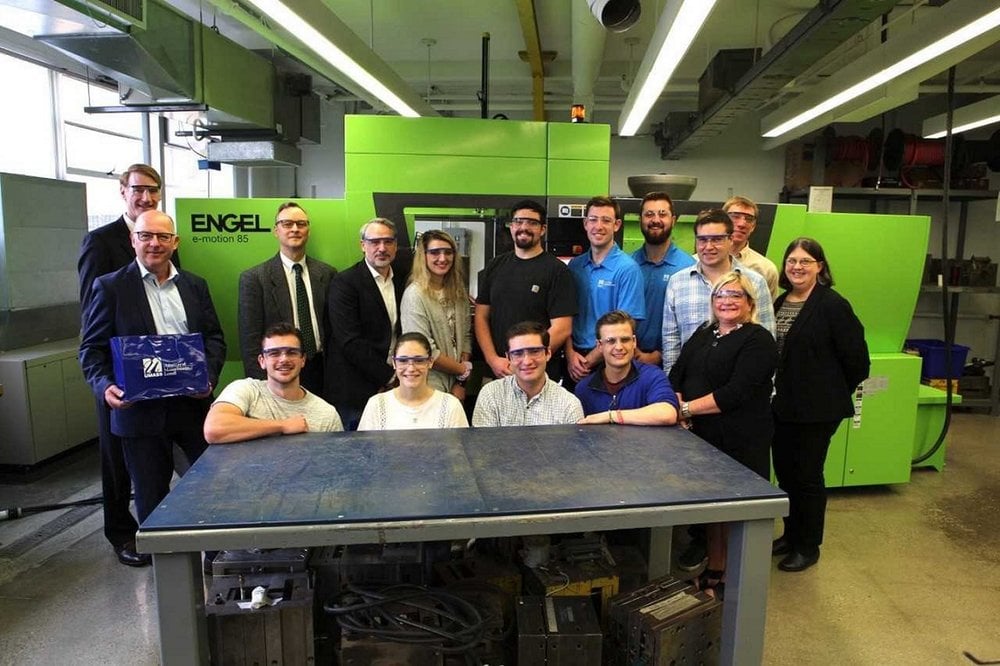
ENGEL, dedicated to supporting the global plastics industry, is doing their part by providing ENGEL equipment to several educational institutions running plastics related programs and graduating skilled employees to meet the growing need.
The need for a skilled workforce
The plastics industry requires skilled employees in a multitude of fields, from the design and development of parts, molds and machinery through to the manufacturing of plastic products. To support the development of this skilled workforce, ENGEL continues to provide several educational institutions with state-of-the-art machinery for their plastics laboratories.
“ENGEL places a great importance on the support of universities and institutes globally,” shares Thomas Leng, ENGEL’s Vice President Global Application Engineering. “We are building the future of both our company and the plastics industry by investing in the young talent of today.”
Learning with the latest advances in machine technology
Over the last six months, ENGEL has provided tie-bar-less injection molding machinery to four universities. Each of the ENGEL e-motion 85 ton machines, equipped with an ENGEL e-pic Z robot, was provided with the latest in machine and processing technology to give students the opportunity to enter the workforce with experience in the most up-to-date technologies available in the plastics industry.
Equipped with the full array of ENGEL inject 4.0 software, ENGEL’s answer to Industry 4.0, these smart machines allow students to experience the latest in self-optimizing injection molding production and the opportunity to see firsthand the increased process stability these machines provide.
In order to make sure the students are able to take full advantage of the capabilities of these machines, ENGEL provides each school with a full day of training specific to the ‘smart’ machine. This includes not only theoretical training, but also a demonstration of each software program with the opportunity to disrupt the process and actually see how the software automatically compensates for these changes:
- determines the optimum clamp force quickly and automatically keeps mold breathing within the ideal range while reducing the number of rejects. (ENGEL iQ clamp control)
- adapts the switchover point and holding pressure profile to match current conditions, automatically compensating for the effects of external influences. (ENGEL iQ weight control)
- independently regulates temperature differences for each distribution circuit, along with pump capacity, to ensure consistent conditions. (ENGEL iQ flow control)
- detects oscillation in the robot’s own movements and actively compensates for vibration caused by external influences to guarantee precise positioning. (ENGEL iQ vibration control)
- an injection compression molding process that allows reduced clamping force for optimum melt distribution in elongated cavities perfectly suited for molding large-surface parts. (ENGEL coining)
Education in Plastics
University of Massachusetts Lowell
Established in 1954, the Plastics Engineering program at the University of Mass Lowell was the first program to provide a degree program in plastics. With an enrollment of 33 students at inception, the university currently has around 350 students in the program (250 undergraduates, 50 in the masters program and 50 PhD students).
Job placement of the program is almost 100% with approximately one third of program graduates going into each process engineering and materials development/testing, 20% pursuing careers in design (mold, product or application engineering), and a few entering technical sales.
In addition to the 85 ton ENGEL e-motion machine, the University of Massachusetts Lowell received a 55 ton ENGEL e-mac machine with LSR molding package for their lab. With one third of the curriculum in the plastics program being lab-based – more than any other major – the university is well equipped.
In addition to the two new ENGEL injection molding machines the lab is outfitted with 8 other injection molding machines, 8 single-screw and 5 twin-screw extruders, 2 thermoformers, 2 blow and 1 injection-stretch blow molding machines, 2 blow film lines, 4 micro-molding and micro-compounders and a wide array of auxiliary equipment.
Professor David Kazmer shared some unique capabilities the new ENGEL equipment has brought to the lab:
- The ENGEL e-motion 85 provides excellent sensing and control, with advanced options for control profiling and sensor feedback.
- The tie-bar-less machine has clamp displacement profiling to support injection-compression molding and core back for advanced foam molding.
- As there is a lot of interest, the university is continuing to expand its curriculum and seminars in the area of molding silicones, and the ENGEL LSR machine is the only machine of its type in the department.
- The automation features are really exemplary. The ENGEL e-pic Z robot is super easy to use, and the conveyor take-out is tightly integrated into the machine.
“We chose to add ENGEL machines to the lab as we were impressed by their vision and commitment, specifically to the iQ suite of products,” shares Professor Kazmer. “We believe that advanced sensing and control is critical to enabling new plastics applications and thus being competitive. We want our students and industry partners to be up to date on the latest technologies.”
Pittsburg State University
The Plastics Technology program at Pittsburg State University will celebrate its 50th year this fall. The university established a 4-year program in Plastics Technology in 1969, along with a hands-on plastic laboratory.
Program enrollment was 3-5 students the first year and has grown to the current 80-85 students majoring in Plastics Engineering Technology with approximately 20 attaining their bachelor’s degree each year. Job placement for graduates is almost 100%, with most filling positions as Design or Processing Engineers, but some pursuing material science testing, quality or technical support / technical sales.
PSU took delivery of its first ENGEL machine in 2001. The new 85 ton e-motion is their fifth ENGEL press and one of three injection molding machines currently in their processing lab. The university’s Industry Advisory Council encouraged them to bring an ENGEL machine into their lab 18 years ago.
After experiencing the quality of the equipment and the strong level of support the company provided, they have maintained the strong relationship – and hope it continues well into the future. “Students, even though learning a new science, can tell that they are working with some of the finest equipment on the market,” says Professor Paul Herring.
“The support ENGEL provides is essential in helping us get up to speed with new capabilities and in ensuring the equipment is ready for classes every term.” The professor continues “Even though the demands placed on the equipment for education don’t compare to those of industry, we notice the way ENGEL machines are designed and built – and how they differ from others on the market.”
Some machine highlights for the students include the clean and quiet operation of the all-electric press – a nice feature for education – as well as today’s evolved controls with their large touch screens and the familiar type of operation. The students also benefit from working with ENGEL’s suite of iQ products and the Authentig monitoring program.
Professor Herring explains “The exposure the students receive to these cutting-edge technologies will prepare them for what they will likely encounter in industry in the very near future. As companies adopt Industry 4.0 technologies, the ideas of connectivity and optimization will be found in all industry sectors. ENGEL’s capabilities with injection molding will provide an excellent introduction to the concepts.”
In addition to three injection molding machines, the PSU laboratory also includes 3 extrusion lines, an extrusion blow molder and reheat-stretch blow molder, 2 thermoformers, a rotational molder, an automatic compression molder and a transfer molding press. All equipment, as well as a wide selection of auxillaries to support it, is housed in labs totaling 7,500 square feet.
Penn State Erie, The Behrend College
The Plastics program at Penn State Behrend was launched in 1984 and saw its’ first graduating class of four students in 1989. Today’s annual enrollment in the B.S. Plastics Engineering Technology degree is between 40 – 50 students, with an almost 100% placement rate at graduation into positions such as Process, Product, Project, Design and Sales Engineer.
As program courses include 50% theory and 50% hands-on lab time, Penn State Behrend has continued to expand their plastics laboratory. They grew from their first Behrend Plastics lab - established in 1988 with two injection molding machines, a single screw extruder, a torque rheometer and some ancillary/test equipment – to the 7,500-square foot Fasenmyer Lab by the school year 1993/94. Today’s program utilizes four plastic labs which total in space well over 10,000 square feet.
The lab at Behrend housed its first ENGEL machine – a 60 ton tie-bar-less model – in 1994. They were donated another ENGEL in 2000, which was retired last year to make room for the new ENGEL e-motion machine.
The four plastic labs contain a total of 12 injection molding machines (including 2-shot, vertical and ultrasonic models), a thermoset compression/transfer press, 6 extruders (4 single-screw, 1 twin-screw and 1 kneading), a blown film line, a cast film line and a pelletizing line, 3 compounding/torque rheometers, 2 thermoformers, as well as 1 injection and 1 extrusion blow molder -- a range of equipment that ensures their students are well-versed in all areas of plastics processing.
The decision to add the latest ENGEL was based on the company’s excellent reputation in the industry as well as the participation of Joachim Kragl, ENGEL’s Director of Advanced Molding Systems and Processing, in several of the University’s industry conferences, which provided an insight into what the ENGEL machines could provide to their students:
- Exposure to state-of-the-art equipment
- Excellent repeatability
- Advanced features
- Easy to learn operation and modern user interface
“Smart machines, such as the ENGEL’s with iQ programs, are the future of manufacturing,” advises Bradley Johnson, Lecturer in Engineering, Plastics Engineering Technology at Penn State Behrend. “It benefits our students to know how to adapt that technology to make more consistent parts. Many people do not implement all the options that are available on today’s machines and the best way to change that is through education.”
University of Wisconsin-Stout
The University of Wisconsin-Stout has a 6,600 square foot laboratory for plastics processing for programs within the Department of Engineering & Technology and started their B.S. degree in Plastics Engineering in 2008. They were accredited by the Accreditation Board for Engineering & Technology in 2013 (the second ABET accredited Plastics Engineering program in the United States).
Course enrollment has grown from twelve students in the program’s first year to an average of 75 students over the past 5 years. Job placement is 100% within six months of graduation, with students starting careers as Process, Tooling, Applications and Quality Engineers, as well as in the areas of R&D, Failure Analysis and Simulation, and Technical Sales.
The University prides itself on its hands-on learning environment, with their plastics-specific courses being approximately 50% each theory/lecture and hands-on/lab. The laboratory portion of the program is supported by six injection molding machines, including the latest addition from ENGEL (which replaced an older model). The new 85 ton ENGEL e-motion molding machine brings some unique benefits to students:
- An exposure to the innovative tie-bar-less technology from ENGEL
- A new and different user interface
- The opportunity to explore “smart” machine technology with ENGEL’s iQ software suite of products
- Touch-screen control technology
“With ENGEL being known as a premier injection molding machine manufacturer, we jumped at the opportunity to bring a new ENGEL machine into our lab,” states Professor Adam Kramschuster. “I was also extremely interested in the machine’s iQ software features as the industry trend is to the ‘smart’ machine. I think this is the future of high-tech molding and it was a great opportunity to bring in this type of equipment for not only the students – but also myself – to learn on.”
The lab at the University of Wisconsin-Stout provides equipment across all areas of plastics processing and testing. Along with the 6 injection molding machines, which are equipped with a variety of RJG and Priamus process monitoring/control technologies, their lab houses 5 extruders (including blown film, cast film, profile extrusion and twin-screw compounding), blow molding equipment, and several thermoformers and rotational molding machines.
Their well-equipped materials characterization lab includes moisture analysis, MFI, FTIR and advanced thermal, rheological and mechanical analysis equipment (DSC, TGA, rheometer and DMA).
ENGEL also offers all the universities no charge ENGEL training courses for their students. This involves members of ENGEL‘s training staff going into the school – either as part of the regular curriculum or offered as an extra option outside the curriculum (however the school prefers) -- to provide regular ENGEL training courses.
This will give students an added advantage, making them even more valuable when applying for jobs. The students will have additional ENGEL specific training that the employer will benefit from, at no cost to them.
“Providing training to the plastics industry’s next generation of workers is paramount for the future of the industry,” shares Joachim Kragl, ENGEL North America’s Director Advanced Molding Systems and Processing. “Whether that training be in basic machine operation, ‘smart’ machine technologies, robot operation or the latest in innovative processing technologies, ENGEL will supply whatever support these educational programs request.”
With an almost 100% placement rate across the board, there is no question that the demand is high for skilled workers in the plastics industry, and that universities in the United States are doing their utmost to train students on the latest technologies available in order to give them the greatest advantages.
“The more complete and up-to-date education that a student receives in plastics related programs, the better it is for our industry,” notes Mark Sankovitch, President of ENGEL North America. “These graduates are the future of plastics. Training them on out-dated technology is not in anyone’s best interest. That is why ENGEL has dedicated itself to supporting plastic-focused education programs throughout the country.”
www.engelglobal.com