www.industry-asia-pacific.com
11
'19
Written on Modified on
A systematic approach to the ideal toolholder
Modern 5-axis and multi-tasking machines as well as high-precision machining centers for micro-cutting enable permanently new and improved machining concepts.
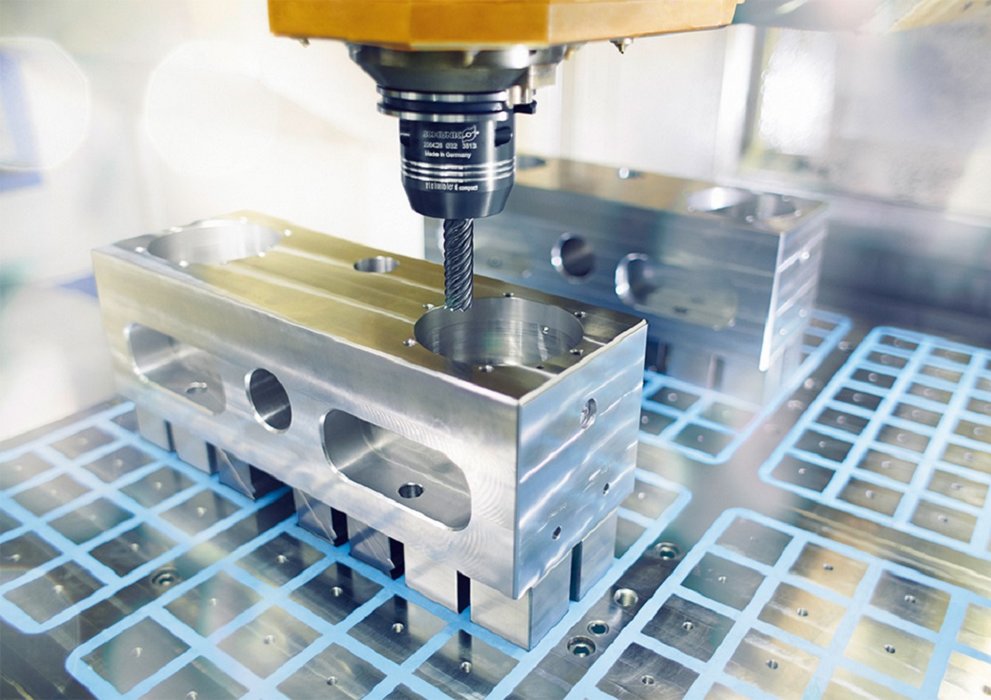
The varied requirements of the individual sectors are reflected by the different distribution of tool holder systems worldwide. While about 60% of these systems in Europe are thermal chucks, the corresponding share in the USA and Asia is 20% and 30% respectively. Collet chucks, on the other hand, play a much larger role outside of Europe than in Germany. The proportion of high-precision hydraulic expansion chucks, in turn, is between 8% and 15% worldwide.
When assessing the development in the market for tool holder systems, two aspects become particularly clear: Firstly, the variety of variants is increasing. On the other hand, precision mountings are rapidly gaining in importance as the improved quality and performance of machine tools leads to growing demand for process reliability and increased tool life.
In addition, increased efficiency in the production of precision toolholders significantly reduce the cost over mechanical chucks, such as Weldon, Whistle-Notch, or collet chuck systems. For hydraulic expansion chucks in particular, initial prices have dropped significantly. This makes it all the more important to question established tool holder strategies on a regular basis, especially when investing in new machine tools.
An assessment of the overall system
When we compare the individual tool holder systems, their technical characteristics and their interfaces to the machine spindle, it becomes clear that there is no optimal tool holder system for all applications. Selecting a system is always a unique decision that depends on a variety of parameters.
The tool holder should never be considered in isolation, but always in terms of the interaction of the entire system, consisting of workpiece clamping, workpiece, tool, tool holder, spindle interface and machine. As the foremost interface with the workpiece, the tool holder plays an essential role, not least because it is able to at least partially compensate for weaknesses within the overall system.
Selection of the ideal tool holder system should be performed in several steps. First, it is important to define the basic criteria that significantly influence the underlying stability of the process. These include the required clamping force, radial rigidity, interfering contour and, if applicable, the suitability for high-speed applications. In a second step, the focus is on quality criteria that affect process quality, precision and productivity.
These include run-out accuracy and repeat accuracy, balancing quality, vibration damping, coolant supply and the possibility of length pre-setting. Finally, in the third step, it is advisable to consider economic criteria within the framework of a cost-benefit analysis (i.e. acquisition costs, service life, flexibility and reusability, as well as the costs of ongoing operation).
Basic criteria are vital for process stability
The basic criteria for the tool holder selection can be understood as KO criteria. They must be met for the machining process to proceed smoothly.
Clamping force/torque: The clamping force of the tool holder determines to what extent the torque at the interface between the tool holder and the tool can be controlled. If the clamping force is sufficient, then the cutting edge of the tool engages the material evenly. If it is not enough, the tool begins to turn in the holder and the cut will be unsteady. In extreme cases, the tool may even be pulled completely out of the tool holder.
The torque transmission is achieved in different ways in the individual tool holder systems: Tools can be screwed by thread into the body. In this case, the thread must be designed so that it at least corresponds to the torque output. A second variant is mechanically clamped tools that are equipped with a positive driver. Only when the occurring torques exceed the breaking or shear strength of the components, a clamping of this kind would fail.
As a rule, these strengths are well above the torques occurring during machining, so high process reliability is ensured for mechanically clamped tools. Finally, the third option is non-positive tool clamping, which uses cross-press connections. In this case, the bore receiving the tool is influenced by heat or external forces so that the tool is tensioned by an overlap.
As a rule, precision tool holder systems, such as hydraulic expansion chucks, work according to this principle. In the context of recent technological developments, it has been possible to increase the clamping forces of hydraulic expansion chucks to such an extent that even volume machining can be reliably achieved. With a diameter of 20 mm, torques of up to 900 Nm are transmitted with modern hydraulic expansion chucks.
Radial stiffness: High radial rigidity allows high cutting forces (i.e. large infeeds and high feed rates). It is therefore an essential criterion for volume machining, since it crucially influences the machining time and thus the productivity, but also the possible projection of the tools.
The radial rigidity depends on the material properties of the tool holder (E-module) and its processing, on the geometry of the tool holder and on its integration into the overall system of the machine tool, particularly from the interface to the machine spindle.
Put simply: the shorter the toolholder, the greater its diameter; the more homogeneous the unit consisting of tool and tool mount, the stronger the wall of the tool mount and the more extensive the support for the holder on the spindle, then the greater the radial rigidity.
Interfering contour: If workpieces on modern 5-axis machines are completely machined in just two clamping steps, accessibility plays an essential role. What is needed are slim tool holders that transmit a sufficiently high torque while also ensuring high precision on the workpiece.
In particularly narrow spaces, alternative tool extensions can be used, which can be mounted between the tool and the tool holder if required. In contrast to contour-optimized tool holders with a spindle interface, tool extensions can be used very flexibly. These are offered with different clamping technologies.
High-speed suitability: If spindle speeds of 80,000 rpm and more are achieved during high-speed cutting, the tool holders must meet special conditions in terms of geometry, concentricity, balancing quality but also in terms of process reliability during tool change.
The smaller the clamping diameter, the more frequently mechanical universal toolholder, but also thermal shrink toolholder or hydraulic expansion tool holder, reach their limits, be it because the available space is not sufficient for the corresponding clamping mechanism or because tools of such small dimensions can no longer be reliably replaced or adjusted precisely. Other clamping technologies, such as polygonal clamping technology, which contains no moving parts, come into their own here.
Quality criteria determine precision and productivity
Historically, compliance with the basic criteria has long been sufficient to perform most of the machining operations. Due to growing demands on the workpiece quality and the efficiency of the machining as well as in the context of modern machine tool concepts and procedures, factors previously considered secondary, which could also be described as quality criteria, are now gaining rapidly in importance.
Both industry-specific and regionally different development speeds can be observed here. The higher the requirements with regard to dimensional accuracy, surface quality, but also with regard to economic efficiency, the stronger the following quality criteria come into focus.
Run-out accuracy: For precision machining, the run-out accuracy of the tools and the entire drive train is of crucial importance. They determine whether dimensions and tolerances are met. Furthermore, the run-out accuracy significantly influences the wear on the tool cutting edge and on the service life of the machine spindle.
If the clamped tool does not rotate centrically to the toolholder axis, there is a risk that inaccuracies will occur and the required dimensions on the workpiece will not be met. Furthermore, the tools will start to bang during machining, which leads to micro-blowouts on the blade and accelerates wear on it.
Repeat accuracy: The repeat accuracy of a toolholder describes how well a toolholder can reproduce a defined parameter over several attempts. For modern precision machining, it is not so much the absolute accuracy but rather the repeatability of the machine and thus of the toolholder that is decisive. Systematic machine errors can be compensated for comparatively easily in modern CNC machines using algorithms in the machine control.
However, this is only possible if there is a high degree of repeatability, i.e. if the respective deviations are always as identical as possible. The repeat accuracy of the toolholder is therefore decisive in determining which accuracies are ultimately to be achieved on the workpiece.
Balancing quality: In simple terms, an imbalance arises when the mass in a rotating body distributed unequally, since either the center of gravity is not located on the axis of rotation (static imbalance) or the principal axis of inertia is not parallel to the axis of rotation (dynamic imbalance). Toolholders often have a combination of static and dynamic imbalance.
Causes can include: Design-related technical interpretations of the toolholder or the tool (e.g. single-edged tools); asymmetrical design of the toolholder (e.g. due to gripper grooves or clamping screws); asymmetrical mass distribution due to manufacturing tolerances; misalignment or errors in the mounting of the rotating body.
Toolholders with large imbalances have negative effects in several respects: poorer surface quality due to vibrations on the toolholder; limited achievable cutting speeds; decreased production accuracy; shorter tool life; bearing damage to the machine spindle.
Vibration damping: Depending on the indulgence frequency response of the overall system comprising machine, toolholder, tool, workpiece clamping and workpiece, vibrations occur during each machining process. These can have considerable effects on the machining result and lead to increased tool wear, tool breakage or machine damage.
Similar to a shock absorber, tool holders are able to damp vibrations and support smooth and consistent cutting engagement, depending on the clamping technology. This allows noise emissions to be minimized, the quality of the workpiece surface is improved, tool life is prolonged, and the spindle can be protected.
Coolant supply: Cooling lubricants perform many functions in machining. They remove chips, reduce heat and friction, ensure a uniform temperature of the tool and workpiece, and help to ensure that tolerances are met. Depending on the type of coolant supply, a distinction can be made between external cooling, peripheral cooling and internal cooling.
There are particular advantages with internal cooling: the cooling lubricant arrives exactly at the cutting edge, with no need to manually align the coolant nozzles; chips are also reliably removed from narrow and deep contours; even when drilling deep bores, the cutting edge can be cooled effectively. As a result, the tool life is extended and the process parameters can sometimes be significantly increased.
Economic criteria influence the efficiency of machining
While the basic criteria and quality criteria directly define the machining process and are always to be considered as a priority, the economic criteria help to inform the final decision from an economic point of view. In addition to the pure acquisition costs of the toolholder, on the one hand the direct costs have to be taken into account: life time, investments in peripherals, running costs (tool change, cleaning, length presetting, maintenance), flexibility, power consumption during tool change, and reusability of mountings.
On the other hand, indirect costs in particular play a key role. These include above all the tool costs (as the service lives of the tools vary considerably depending on the clamping system used) as well as the costs/savings resulting from reduced or increased productivity.
Viewed over the life span, indirect costs per toolholder can lead to savings in the five-figure range. In addition, the aspect of accident prevention has been rapidly gaining in importance recently. Burning or crushing in particular are considered potential risks.
Systematic comparison
The criteria catalog shows that a detailed consideration of the respective application is always recommended when selecting a toolholder. As a competence leader for gripping systems and clamping technology, SCHUNK has extensive expertise in this area. Furthermore, the SCHUNK toolholder program is considered the most comprehensive range of technology made in Germany.
It ranges from mechanical toolholders and heat shrink holders, to attractively priced hydraulically tensioned toolholders, to high-end chucks based on hydro-expansion or polygonal clamping technology. The iTENDO sensoric toolholder is currently top of the line, which allows for seamless condition monitoring and documentation of process stability, real-time control of speed and feed rate as well as unmanned limit value monitoring.
www.schunk.com