www.industry-asia-pacific.com
02
'19
Written on Modified on
Reaching for the stars with textile machines
Reliable suppliers of automation technology ensure success.
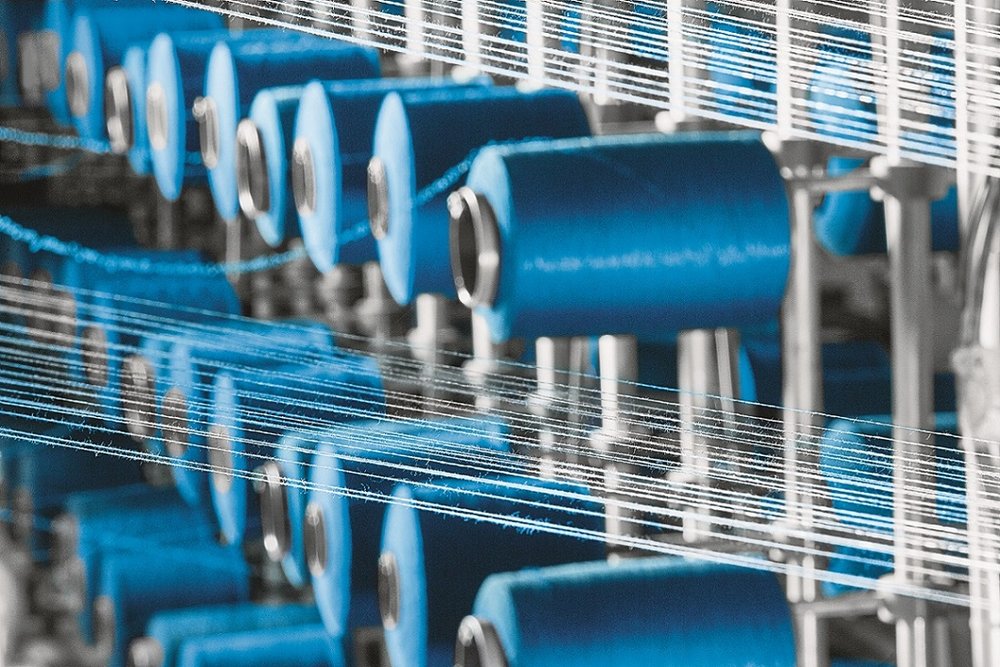
The global demand for textiles is growing unchecked. Experts expect an increase from 80 million textiles a year today to 120 million in 2030. Yet textile prices are falling. As a result, textile manufacturers are forced to keep cutting costs. For OEMs this means developing ever faster and more productive machines and plants. However, this can only be done with reliable and attractively priced components, such as from the Festo core product range. These are the “Stars in Automation Technology” – quickly available worldwide, durable and attractively priced.
“Many manufacturers of textile machine have their development centres for pre-production machines in Europe. But their textile machines are assembled in production countries such as China or India. Closeness to customers therefore needs to be more than just an empty promise,” explains Bernhard Wolz, Key Account Manager for the textile industry at Festo.
That is why it is hugely important for the major machine manufacturers that their suppliers be close at hand all over the world – with products, spare parts, advice and services, and also with individual, customised product solutions. That is why the automation specialists from Festo with their industry expertise are travelling not just around Europe but especially in Asian countries with their vast stocks of textile machines.
Ring spinning and compact spinning machines
With ring spinning, new machine generations help reduce energy consumption and production costs. Modular machine concepts increase flexibility with regard to the fineness of the yarn. The efficient ring spinning machines produced by the world market leaders can process both coarse and fine yarns as well as special yarns. Cost-efficient solutions reduce the investment costs per kilogram of yarn and thus increase the cost-effectiveness of ring spinning.
Compact spinning machines bind the edge fibres of a yarn completely into the yarn structure. Compact spinning machines with cutting-edge technology require only around 25% of the compacting energy of other comparable solutions. They eliminate the costs and effort required to replace worn compacting belts. Yarn produced on these machines has very little hairiness.
Sturdy standard components
Ring spinning and compact spinning machines as well as other textile machines typically require sturdy standard automation components. They provide reliable operation in the dusty environments caused by fibrous basic textile materials and also in the hot and humid tropical climate of the production countries in south-east Asia.
Pneumatic cylinders from Festo such as the DSNU (round cylinder), DSBC (ISO cylinder) and ADN (compact cylinder) with the self-adjusting cushioning system PPS have demonstrated their proverbial durability millions of times over, both in the laboratory and in practical operation.
The same applies to the valves VUVS and valve terminals VTUG from Festo. The pneumatic control circuit is completed with the flexible and modular service units of the MS series from Festo as well as suitable tubing and fittings. If a precise approach to positions is required, the solution of choice is the electric cylinder EPCO from the Optimised Motion Series, since it is just as easy to commission as a pneumatic cylinder.
2200 components in the core product range
The automation components mentioned are part of the Festo core product range. These "Stars in Automation" include over 2200 components from every phase of the pneumatic and electrical control chain – from compressed air preparation, valves and cylinders to accessories, such as matching tubing and fittings.
With the core product range from Festo, textile machine manufacturers can realise around 80% of all applications effortlessly and quickly at attractive prices, even when large quantities are needed.
Fast availability worldwide
Many of the components marked with the star are ready to be shipped just 24 hours after the order is received, while configurable products are ready for delivery within five days. All products in the core product range are available worldwide and with the same level of quality thanks to automated production at various decentralised locations in the core markets of Germany, China and the USA.
There are further plants in India, Brazil, Hungary, the Czech Republic, Bulgaria and Switzerland. Distribution is also decentralised thanks to highly automated logistics centres in Germany, China and the USA, so 70% of all customers can be reached within one day.
Efficient production
The hallmark of the latest components of the core product range is the collaboration between the design engineers and production planners at Festo. They worked closely together during the development of these products to ensure that the components can be manufactured in the Festo plants with a high degree of automation. For the new mini slide DGST, for example, the yoke and slide are manufactured fully automatically as a single part.
In addition, the developers successfully reduced the number of components by 60% compared with the previous model. This enables the DGST to be produced in large quantities with maximum efficiency. This approach also allowed the cycle times for the guided drive DFM to be reduced by almost 50%. Festo plants can now produce a DFM every minute. Another example is the fully automated production line for the standard valve VUVG, which produces a fully assembled valve every 12 seconds.
New stars in the world of automation
The current Stars in Automation have more to offer than their price and logistics advantages. The mini slide DGST, for example, is the smallest of its kind and the shortest slide drive on the market. However, it is strong when it comes to precision, forces, motion control, durability and reliability.
Other new Stars in Automation include the lightweight and compact cylinder ADN-S, which is produced almost entirely as one part and can perform small and micro-movements in the smallest of spaces. The regulators and filter regulators of the MS2 series service units are designed for use close to the process directly in the machine and for end-of-arm applications. They are lightweight and compact, but with high flow rates of up to 350 l/min.
The tubing/fitting combination PUN-H/QS also ensures reliable compressed air supply in standard applications and in wet areas and is suitable for use in the food industry. These are just some of the more than 2200 products in the Festo core product range that offer quick availability worldwide at attractive prices.
Better delivery service
In the case of high-performance machines such as rotor and air spinning machines, OEMs not only expect to be supplied with reliable standard components but also expect their automation suppliers to offer a wide range of services that will allow them to concentrate on their core competencies and develop their machine technology further.
“They expect us to supply complete units such as mounting plates already fitted with valve terminals, service units and tubing,” reports industry expert Bernhard Wolz of Festo. Complete units such as a fully assembled DSBC cylinder with sensors, fittings and attachments can be configured online with the help of the Festo Design Tool 3D and ordered as a single unit.
The Festo Design Tool 3D is a 3D product configurator for generating Festo-specific CAD product combinations. This allows machine designers to generate and order product modules quickly, error-free and automatically in a CAD format. OEMs also attach great importance to customer-specific tubing with special labelling and specific flow control valves.
www.festo.com