www.industry-asia-pacific.com
26
'19
Written on Modified on
Shaped charge, a new tool for the industrial world
Numerical analyses to better understand the physics of penetration, increasing the precision of the design.
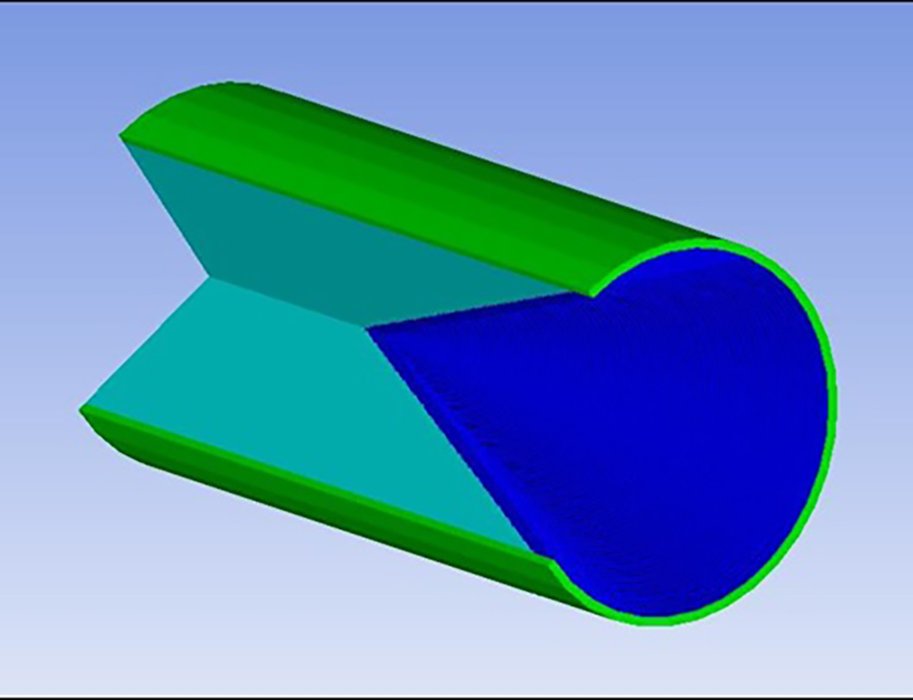
The core of this type of device is a metal liner that is rapidly deformed and projected against the target following detonation of the surrounding explosive. The ability to simulate the whole phenomenon, by using dedicated solvers, enables engineers to better understand the physics of penetration and, therefore, to increase the precision of the design.
The numerical study presented in this article compares the results obtained using two consolidated commercial solvers, LS-DYNA® and ANSYS® Autodyn®, and details the peculiarities of the cases. The impact of a high-speed shaped charge's jet onto a target and its subsequent penetration are characterized by fast dynamic phenomena that are quite challenging to simulate.
Computational studies related to shaped charges are typically addressed through the so-called hydrocodes, or numerical solvers able to predict the behaviour of materials in such extreme conditions. The afore-cited software were used to reproduce some experimental tests based on strictly confidential data. As a result, this article qualitatively describes the computational outputs.
However, information is provided on the strategy and models adopted, which can be useful for the structural hardening of the passive ballistic protections or, alternatively, to maximize the effects of the shaped charge.
Before performing the numerical analyses, data relating to a series of experimental tests using standard shaped charges that were carried out by a RINA Group company, were collected and evaluated.
This was done to predict the effects of the impact of the jet produced by such charges on passive ballistic protections. In particular, two specific target configurations were studied: monolithic blocks made of ductile materials and sandwich structures (assemblies of several layers of both ductile and brittle materials).
Autodyn was used with the aim to determine the equivalent charge, whilst LS-DYNA supported the numerical verification on the monolithic target. With regard to the multi-layer configuration, which is of major interest to the present study, Autodyn was the only numerical means used.
The penetration of the monolithic target of standard steel was selected as a reference and in order to obtain the equivalent charge in two stages, hereinafter referred to as identification and calibration, which were performed in sequence. In the identification stage, the equivalent charge was set up following the guidelines for the design of conical shaped charges.
These simulations were performed using the arbitrary Lagrangian Eulerian (ALE) method and modelling the shaped charge and the target by using Eulerian and Lagrangian sub-grids, respectively. In the calibration stage, the depth of the hole obtained in the identification phase was aligned with the one actually produced, by properly tuning one of the most influential parameters of the charge (density).
The device consists of an external cylindrical aluminum casing containing a certain amount of explosive material (TNT) whose front side presents a conical cavity that houses a copper liner characterized by a specific charge diameter (CD). Regarding the equations of state (EOS) for the materials, the Shock model was used for the liner, target and casing, whilst the Jones-Wilkins-Lee (JWL) was adopted for the TNT.
Regarding the strength models, the Steinberg Guinan model was used for the target and casing, the Multilinear Hardening model for the liner, and High Explosive Burn for the explosive. The geometrical axial symmetry of the charge made it possible to implement a 2D case representing only one sector of the device, by assigning the axial symmetry boundary condition to the axis along which the jet is supposed to travel.
This assumption is commonly accepted by computer aided engineering (CAE) experts because the metal jet moves at high speed and at a sufficient distance from the edges of the donor system (target). Furthermore, this assumption is even more true since the direction of the jet is orthogonal to the target surface.
The concept of axial symmetry allows the analyst to significantly reduce the required computational time while maintaining adequate calculation accuracy of the solution. The portion of the mesh filled with air was initialized using the sea-level ambient condition and an outflow condition was imposed at its boundaries.
Moreover, the target was constrained by fixing some nodes of the rear edge of the target, while the detonation was assigned to a set of nodes of the cells filled with TNT. A first set of simulations was carried out after properly modifying the refinement of the mesh to obtain a case providing mesh independent outputs (a mesh sensitivity study), with the intention of assessing the generated case.
Once obtained, the smallest elements of the mesh were less than 1mm in size. Then, the density of the liner was suitably adjusted to finally obtain a penetration with a relative percentage error below 4%.
To simulate the brittle behaviour of the ceramic layer appropriately, considered to be of fundamental importance, the ALE method was coupled with smoothed particle hydrodynamic (SPH) in Autodyn. The SPH method considers the elements constituting the model to be composed of free particles that, without being anchored to any mesh (mesh free method), include all the characteristics of the constituting material.
Particularly, in the case of high-speed impacts, the use of the SPH method allows an accurate reproduction of the response of brittle materials, including the phenomenon of destruction and the fragmentation of the elements. The entire charge was thus represented as the sum of three SPH blocks, while the target was modelled as a series of two Lagrangian steel layers and an SPH ceramic layer.
The set-up of the EOS and resistance models of the various materials involved followed the indications presented in the literature. With regard to the multi-layer configuration, the physical characteristics of the ceramic protection were extrapolated from the information provided in the materials sheet and they were then inserted into the solver by modifying the properties of the material already present in the library.
The obtained results demonstrated the ability of the developed CAE predictive model to assess the depth reached by the jet in a multi-layer target. In addition, they also confirmed the effectiveness of using such ceramic structures for passive ballistic protection to counteract the action of a shaped charge.
www.rina.com