www.industry-asia-pacific.com
20
'19
Written on Modified on
Expansion of the Circular Milling System with the SYSTEM 620
With the System 620, Horn responds to existing market requirements that required a more stable version of the circular milling system for high-feed milling and face milling.
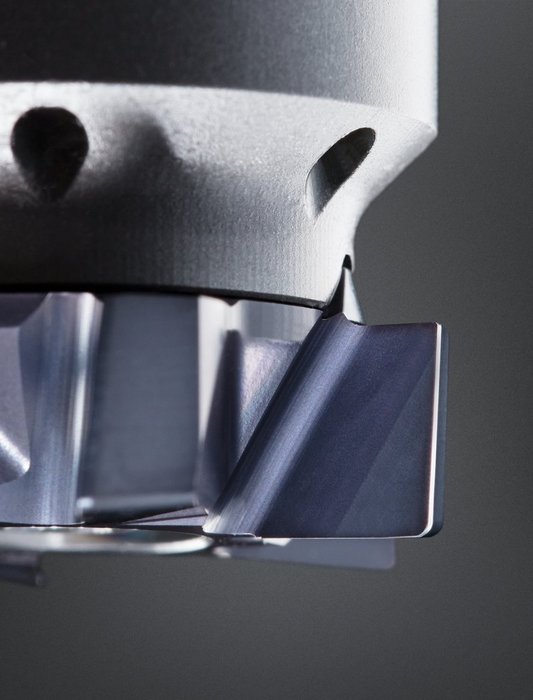
Meanwhile, the high-feed milling version, which has the same cutting edge diameter and the same number of teeth, supports a cutting depth of ap = 0.5 mm (0.0197"). The low-vibration carbide shafts are available with a diameter of 20 mm (0.787") and shank lengths of 150 mm (5.906") and 95 mm (3.740").
The HORN circular milling system offers users a whole host of process advantages: it is fast, reliable and achieves good surface results. During the process, the tool plunges into the material either at an angle or horizontally, and is then driven on a helical path. This means that threads, for example, can be manufactured to a high level of reproducible quality.
When compared to machining using indexable inserts on larger diameters or solid carbide milling cutters on smaller diameters, circular milling is generally more economical. Circular milling cutters have a wide range of applications: they are able to machine steel, special steels, titanium and special alloys.
These precision tools are especially suited to groove milling, circular interpolation milling, thread milling, T-slot milling and profile milling processes. However, they also impress in special applications, such as milling sealing grooves or machining connecting rods.
www.phorn.com