www.industry-asia-pacific.com
19
'19
Written on Modified on
Safe use of the human/robot collaboration
Industrial automation is facing a fundamental change.
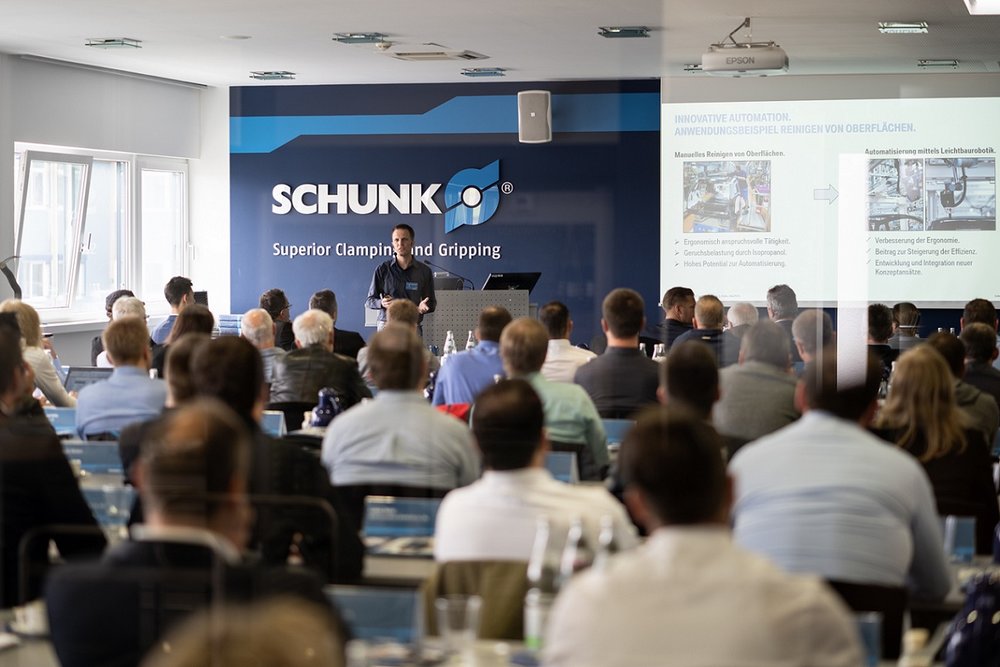
According to SCHUNK's development chief Prof. Dr. med. Markus Glück, the number of collaborative applications for robots in manufacturing is certain to grow dramatically in the coming years.
This importance of this trend was reflected in the large turnout for the 4th SCHUNK User and Technology Dialog on "Using HRC safely in companies."
For two days, specialists in automotive, robotics, automation and engineering as well as medium-sized industrial companies from Germany and Europe gathered to discuss the applications and opportunities of Human-Robot Collaboration (HRC) and experience them up close.
Pro. Dr. Markus Glück, Chief Innovation Officer (CINO) at SCHUNK, is confident that co-acting, meaning unrestricted interaction with robots, is on the verge of a breakthrough. The main driving forces are ergonomic relief, greater flexibility of work processes, increased efficiency as well as the expansion of logistics, loading, handling and retrofitting.
"It's all about bringing together the strengths of humans and robots," said Glück. The speed, power, repeat accuracy and high quality of robotics will be combined with the human strengths of perception, improvisation, reaction and adaptation to create synergy. The goal: automation with maximum flexibility of use.
Careful testing in advance
The development chief admits that first-time projects require a substantial amount of work that should not be underestimated: "The usual amortization periods of less than two years will be difficult to achieve at the beginning," says Glück, who recommends a systematic approach in which the suitability of the HRC application is first assessed based on specific eligibility criteria.
Such criteria include the programming cost or the ability to implement operator guidance, the cost of integrating the application into the process chain, options for intuitive training, handling and acknowledgment, moderate cycle requirements as well the employees' relationship with technology.
He also recommends conducting a business assessment that takes into account the costs of robot procurement, commissioning and integration as well as costs for safety precautions and certification.
Conversely, however, the assessment must also take into account the savings achieved by lowering personnel costs and increasing productivity. Above all, first-time projects should be thoughtfully approached, carefully planned and implemented with less complexity.
SCHUNK product manager Benedikt Janssen presented SCHUNK's options for cobot peripherals. For example, the SCHUNK co-act EGL-C surpasses the usual force limit of 140 N in collaborative applications.
Starting in late 2019, collaborative form-fit handling of parts up to 8 kg will be possible for the first time. An intelligent gripping strategy makes this breakthrough possible. The main field of application is supportive handling for ergonomic relief.
Faster and faster CE certification
Jochen Vetter, Team Leader for Robot Safety at PILZ, gave an overview of standards-compliant use of HRC as well as reliable measurement of applied forces. In order to safely implement HRC applications, both the manufacturer and the operator require appropriate measures, from collision-friendly environment design and functional safety to comprehensive user information and training.
Vetter made it clear that learning curve effects are significant in the world of HRC. Whereas it used to take up to eighteen months for the first HRC applications to receive CE certification, it now takes only about six months for first-time customers.
Subsequent projects can even be implemented within three months. PILZ assumes a substantial part of the responsibility with its written confirmation on the declaration of conformity, said Vetter.
Quick check simplifies workplace analysis
Dr. Alfred Hypki, Senior Engineer at the Department of Production Systems of the Ruhr University Bochum, presented a standardized questionnaire, which enables fast, objective and reliable assessment of HRC potential in companies. Within one hour, the quick check can determine whether an application harbors potential for HRC.
Additionally, by combining the EMA process simulation software for human-process organization with the ROS framework, it was also possible to integrate a path planning system with dynamic obstacles into simulation scenarios.
As a result, holistic workplace simulations of HRC scenarios are now possible. Hypki strongly recommended that the involved disciplines and individuals participate in the decision-making and planning processes at an early stage.
Automotive industry acting as trailblazer
Sebastian Keller, production specialist for the BMW Group at the Leipzig plant explained how HRC is successfully employed in day-to-day production. Applications range from applying window adhesives to robot-controlled measuring equipment and palletizing systems to surface cleaning in assembly.
A total of 29 HRC applications have already been implemented by the BMW Group, primarily power and force limiting applications. In doing so, the company has gained a number of valuable insights. For example, BMW recommends choosing applications so that the workers immediately recognize their advantages and benefit from them.
In addition, participatory development strategies that involved the affected employees at an early stage increased acceptance and simultaneously benefit from employees' ideas and expertise.
Furthermore, for new installations, the company recommends allowing sufficient time for risk analysis and implementation of safety strategies. Keller also recommends forming a team of experts for building and converting automated systems on site.
Start-ups ensure rapid pace of development
Jens Kotlarski, Managing Director of Yuanda Robotics in Hanover, Germany, gave an impressive presentation on the creative potential and dynamism of start-ups in the field of HRC. In his eyes, the world is now entering a golden age of robotics.
Later this year, Yuanda Robotics will launch a new type of collaborative robot that combines certified safety, joints with integrated torque sensors, built-in cameras, artificial intelligence, a graphical user interface, and modular hardware and software. In his opinion, robots for collaborative applications should be like a power tool and should always be exciting to use.
Above all, Yuanda wants to take the interaction with the operator to a new level of development. The goal is to ensure simplicity of use, for example through a graphical user interface, intuitive programming and simple integration of vision systems.
"Collaborative robotics is much more than safe HRC," says Kotlarski. It's mainly about interaction and usability, he says. Looking ahead, he sees automatic object recognition as the goal, with secure cameras and secure networks in the background, including use of digital twins and automated path planning.
Turnkey cobot solutions
Uwe Schmidt, Head of the COBOT World division of HLS Ingenieurbüro GmbH in Augsburg, demonstrated how HRC scenarios can be implemented in the real world.
As an integrator, the company develops certified cobot solutions for applications such as automated loading of machine tools and uses different platforms and configurations for this purpose. For him too, simulation of machining areas is a topic that is becoming increasingly important for HRC. Dirk Garzke, head of automation at ZOLLER, presented HRC solutions in the field of tool management.
For him, the most important factors for increasing acceptance include not only end-to-end flow of data within the overall process, from tool management to warehousing and logistics systems to the machine tool, but also soft factors, such as the name of the cobot system. Zoller chose the name "Cora" for the system.
Live demo tour
Visitors to the User and Technology Dialog took a tour of the different stations to experience first-hand how diverse the concepts and solutions for HRC already are. The tour showcased different testing and assembly applications, collaborative pick & place solutions as well as solutions for collaborative tool presetting and preparation.
During the tour, it became clear than an enormous selection of different cobot systems with different strengths and capabilities is now available. The peripheral equipment is also continuously expanding.
By the end of the year, SCHUNK will be offering a complete range of certified Co-act grippers for a wide variety of interfaces and applications. In the process, more and more intelligence is being directly integrated into components.
A quick poll of participants in the User and Technology Dialog shows that HRC is now becoming a priority for users. Altogether, they named roughly 50 HRC applications. Around one-third of the HRC community has already gained experience with pilot applications and is moving from the evaluation phase to the next phase of implementing the technology in real-world manufacturing applications at selected sites.
The preference is mainly for robots from Universal Robots and KUKA, but cobots from other manufacturers are also attracting great interest. The main areas of application are pick and place tasks, assistance with assembly applications and in-house logistics.
www.schunk.com