Lenze Provides Plant Operators With a Smart Solution for Materials Handling Technology
The right drive for reduced engineering complexity and improved energy efficiency.
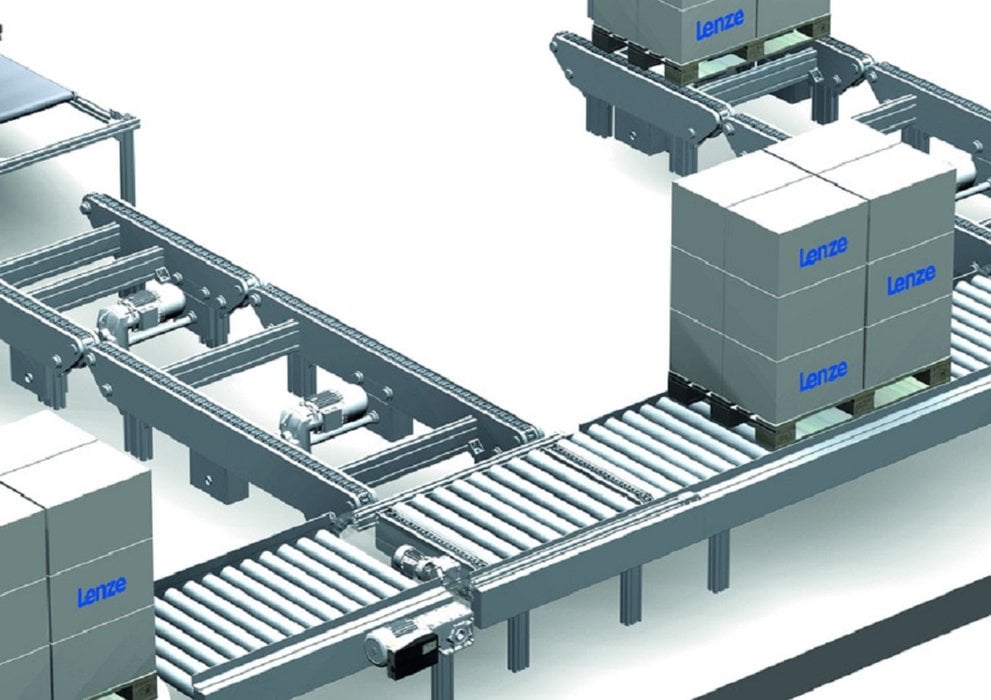
Lenze Americas, a global leader and manufacturer of electrical and mechanical drives, motion control and automation technologies, discussed its fully-integrated solution that provides plant operators with an energy-efficient alternative for many applications at ProMat 2019 in Chicago, Illinois from April 8-11.
Conveyor applications have to perform three diverse tasks, each of which places entirely different demands on the drive technology. At the start, a high breakaway torque must be generated to accelerate the load. Once the nominal conveyor speed has been achieved, only the friction of the mechanical design needs to be overcome.
Much lower torques are sufficient for this. This changes again for pallet alignment, namely when they are pushed against the limit stop and the rollers or chains are forced to slide briefly underneath the pallet, creating high frictional resistance.
The energy required for this accounts for 95 to 97 percent of the overall costs during the service life of a drive. Common geared motors, which are operated directly on the 50/60-Hz using contactors and/or motor-starter combinations, are not particularly efficient in this case. This is because they need to be configured to suit the starting torque - and are then over dimensioned during the phase of normal conveyor speed.
Even the use of frequency inverters, which typically provide up to twice the overload (180 to 200 percent) during the start-up process, cannot fully resolve this problem. They result in additional costs and increased engineering effort, as well as providing a complex functional range that needs to be paid for by the OEM and end customer, but is essentially useless for their horizontal conveyor technology.
Lenze's solution addresses these current challenges relating to drive technology for horizontal conveying. As a fully-integrated solution with a dedicated electronic control unit, it provides up to four times the nominal torque during acceleration and alignment. Accordingly, it can be sized based on the required power during constant operation and runs at almost optimum performance in this mode and not in the less efficient partial load range.
The solution features the Smart Motor with g350 gearbox, Smart Motor with g500gearbox, in-cabinet c300 controller and I/O 1000 modules, remote fieldbus I/O and IR sensors. Lenze's g500 gearbox with Smart Motor and the g350 with Smart Motor offer the simplicity of a motor direct on line with just the right features of an electronically controlled motor.
They work without a contactor or starter; fixed speeds can be set at will; highest energy efficiency requirements are met; and they can be conveniently operated via a smart phone.
The entire conveyor concept offers:
- Costs reduced by use of a smaller cabinet, less cable, less engineering time, less manufacturing time, fewer part numbers, and less operational costs. Examples of increased functionality include: defined Start/Stop ramps, better energy efficiency, standardization/modularity, simplicity/reduced complexity, and a flexible automation concept.
- With five adjustable speed levels - and the infinite selection of rotating direction - definable start and stop ramps, as well as an electronic contactor and motor protection function, the Smart Motor's integrated electronics eliminate the components, reversing contactor and motor protection circuits, as well as the polarity reversal required for mains motors.
This enables space savings of up to two-thirds of these components were previously installed in a control cabinet. In the Smart Motor, speed levels are switched independently of the fieldbus using 24V signals. The 400-480V cabling can be implemented with a stub so that entire drive trains can be built on a single supply line.
The control unit is also prepared for such a design: in this case, entire units with several drives can easily be integrated. Wireless technology can be used to transmit predefined speeds and acceleration ramps, as well as to optimize speed levels, by smartphone - without the need for expert knowledge or extensive staff training. Braking is also controlled electronically.
This ensures that a constant braking distance is maintained at all times, regardless of the load.
www.lenze.com