www.industry-asia-pacific.com
30
'19
Written on Modified on
PENSA Accelerates Product Innovation with MakerBot METHOD
The MakerBot METHOD 3D Printer streamlines PENSA’s product design and development processes, reducing production time and costs.
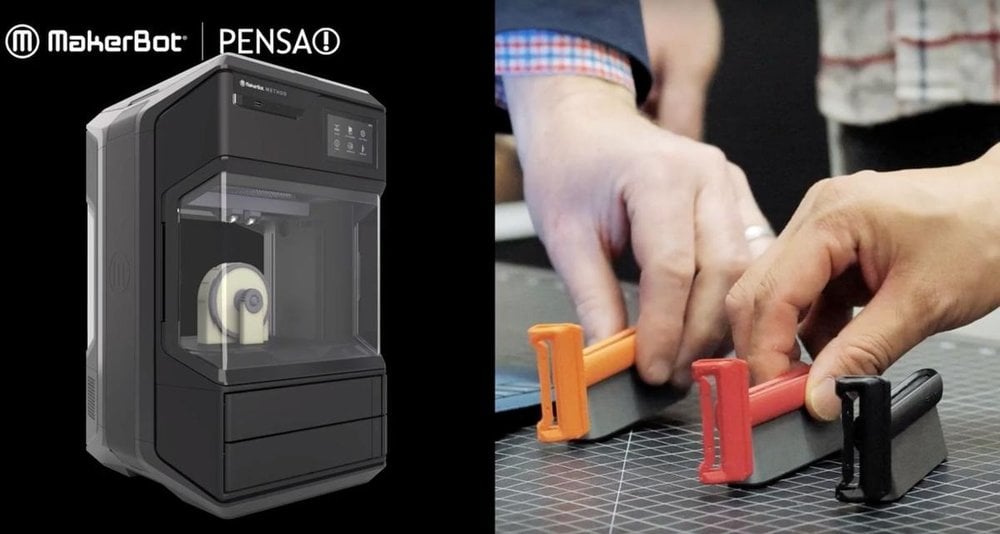
PENSA is a full-service design and engineering agency that develops products and experiences to help customers improve the quality of their lives. The agency works with industry-leading corporations and startups, including GoTenna, OXO, Bayer, One Blade, D.I. Wire, One Drop, and Pepsico.
Since integrating METHOD into their daily design process, the product development teams at PENSA are enjoying their new tool; testing ideas early and often in order to accelerate design iteration cycles and make quicker decisions. The designers and engineers utilize METHOD for a wide range of uses, including to print fixtures or end-use parts, form studies, volume studies, and functional testing.
“PENSA is centered on invention, and we use 3D printing as a way to help us invent. The MakerBot METHOD allows us to be uninhibited in our testing – a crucial step for invention and design,” said Marco Perry, Co-founder, PENSA.
“METHOD has proven itself to be an extremely reliable tool. The dimensional accuracy that we are getting with METHOD compared to any industrial FDM is as good or better than anything we have owned or used in the past. Before METHOD, we would only use industrial 3D printers to check for fit and finish. Now, we are using 3D printing earlier in our process, and we can run through iterations very quickly, using it to check for functionality, ergonomics, and mechanics.”
Previously, PENSA relied on a combination of desktop and industrial 3D printers to execute prototyping at different stages of the design process. However, the desktop machines were unreliable, while the industrial 3D printers were costly to operate, required dedicated technicians, and included lengthy cleanup times.
This would ultimately translate to higher costs and longer production times for PENSA’s clients. As a result, the company invested in METHOD for its industrial grade 3D technologies, desktop accessibility, and disruptive price point.
“We are thrilled to receive such an overwhelmingly positive response from our early customers,” said Nadav Goshen, CEO, MakerBot. “As one of the leading product design firms in New York, PENSA understands better than most the need for reliable rapid prototyping. METHOD was engineered to enable product teams like those at PENSA to become more agile and help them speed up their innovation processes.”
METHOD carefully controls the 3D print environment to produce repeatable and consistent parts, vertical layer uniformity, and cylindricity. This level of dimensional accuracy and reliability are made possible by leveraging industry-leading Stratasys® patents, including a circulating heated chamber, precision PVA water soluble supports, and dry-sealed material bays.
“The reality when it comes to physical models is that it is just a step in the process. The real result for our clients is that it is a product that sells well for them,” explains Perry.
“The fact is that we rely heavily on our tools, just like a chef would rely heavily on a sharp knife. If a chef is thinking about how the knife works, he is not thinking about the meal he has to make. For me, the best tool is one where you do not have to think about how it works. We have to take it as a given that the product will work well because we are focused on the whole picture. The reliability of the METHOD really helps with that—it’s not even a thought. You just run it.”
www.stratasys.com