www.industry-asia-pacific.com
07
'19
Written on Modified on
Does your machine also need too much run-out?
Who doesn't know that? If you dimension a travel drive or a linear drive, you must install a mechanical buffer at the end of the travel distance to be on the safe side.
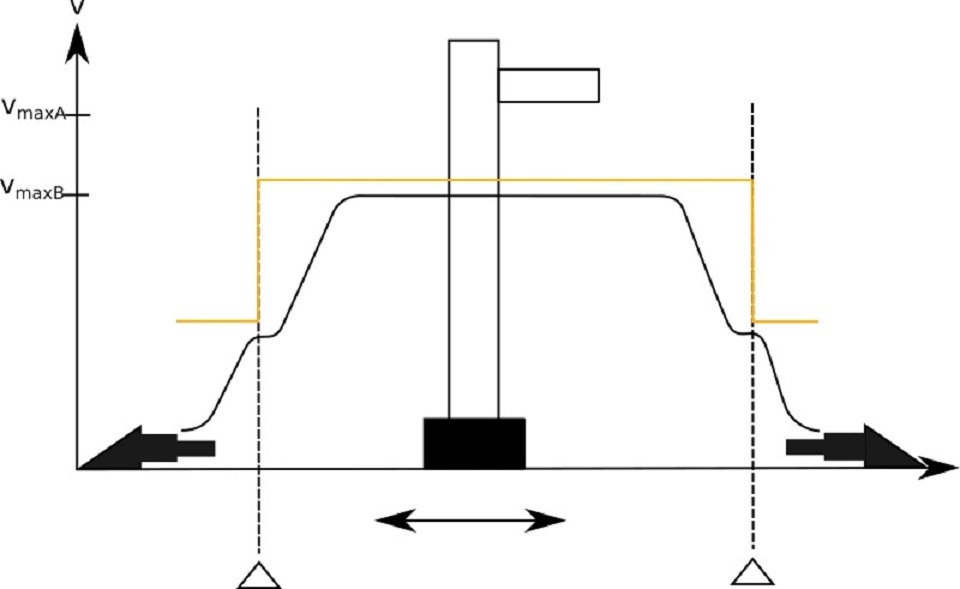
With machines, this track is not an active working path - similar to the gravel bed next to a race track. The buffer zone reduces the actual working area - in other words, it makes the machine larger. Both are undesirable.
LTI Motion offers the solution here. In the relevant standard for AS/RS stacker cranes, for example, the speed to be taken into account for the calculation may be reduced to 70 % for buffer design if safety functions in accordance with DIN EN 528 are used. Since the speed is included in the calculation of the buffer zone in quadratic form, you can always reduce the length of the buffer zone to less than half by using these safety functions.
This principle can also be applied to travel drives and linear axes outside AS/RS stacker cranes. Among other things, LTI Motion offers the safety functions required for this, such as SLS (Safe Limited Speed) or SCA (Safe CAM = Safe Cam) integrated in the ServoOne servo drive system or in the complete SystemOne CM automation system.
Safe monitoring of the travel drive can also shorten the buffer zone here. This gives your machine more space for the active working path, i.e. it becomes smaller or faster.
www.lti-motion.com