www.industry-asia-pacific.com
10
'19
Written on Modified on
Accepting responsibility - for hygiene, safety and protecting the environment
Accepting responsibility - this is the company philosophy of Hamburg-based company Dr. Weigert, the developer and manufacturer of cleaning and disinfecting agents. Not only does this include responsibility for hygiene and protecting the environment, but also protecting the company's employees from dangerous manufacturing and logistics processes.
Accepting responsibility starts with partner selection"Protecting man and machine from dangerous processes in manufacturing and logistics is a top priority at Dr. Weigert, as well as being responsible for hygiene and protecting the environment", says Dirk Böttger, who has been working at Dr. Weigert for 16 years. The qualified process technology engineer and current deputy operations manager knows about the safety risks involved in quick, automated processes such as those in the film wrapper and rolling gate areas. Choosing reliable partners is essential as far as he is concerned. On the one hand he is referring to Industrieautomation Dirk Hähner, for whom he greatly appreciates the consistent, competent project support from planning and installation to commissioning. On the other hand he is referring to Leuze electronic, the manufacturer of safety-related protective devices MLD and MLC for the safeguarding of material flows in the film wrapper and rolling gate areas, which operate fault-free and enable a high degree of system availability.
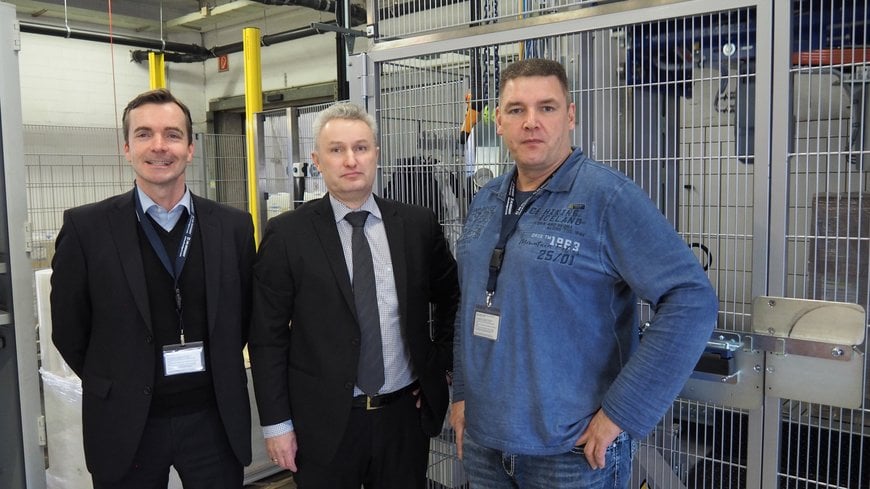
Figure 1: from left: Frank Bröcker, Sales Manager at Leuze electronic, Dirk Böttger, Deputy Operations Manager at Dr. Weigert, Dirk Hähner, Owner and Managing Director of IDH
System modernization pose new safety-related requirements
Dr. Weigert mixes cleaning and disinfecting agents in accordance with the company's own recipes for professional cleaning and disinfecting in laboratory techniques and medical technology, the large-scale kitchen sector and the pharmaceutical, cosmetics and food industry. After mixing, the chemical products are poured into plastic canisters with different volumes and designs, among other things, and then stacked on pallets by robots, each of which has its own affectionate nickname and history. For example, one robot is called Antje, after a Dutch advertising figure, and another has the name of a former HSV (Hamburg Football Club) manager, Huub Stevens. Driverless transportation systems take the products stacked on europallets to the area in which the goods receive an outer packaging in the new TOSA 126 E film wrapper.
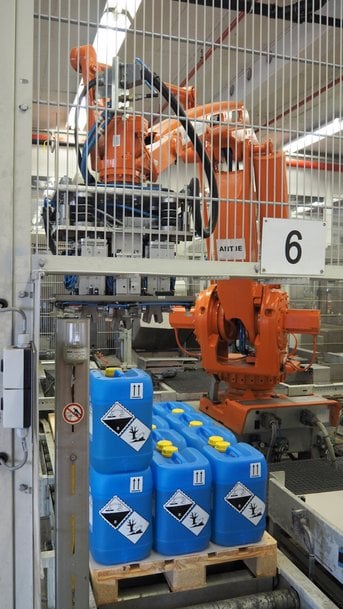
Figure 2: Robot "Antje" stacking the filled cleaning agents onto a europallet
From primary to secondary packaging
The entire material flow process, from the film wrapper's in and outflow to passing through the rolling gate on the way to the warehouse, has been realized by Leuze electronic using a holistic, safe system solution concept. "As well as the reliable quality of its safety technology, we particularly appreciate the company's competent advice, quick support and efficiency – we are therefore delighted to incorporate Leuze electronic safety components into our safety concepts", says Dirk Hähner, Managing Director of Industrieautomation Dirk Hähner. Particularly when a tricky task has to be carried out in a special application, Leuze electronic often has flexible, smart solutions at the ready which stand out from conventional safety concepts. "We promise our customers Smart Sensor Business 4.0 – which is not a marketing term or advertising slogan but a real promise to the customer by us, the sensor people", says Frank Bröcker, who has been the Hamburg area Sales Manager for 10 years. What we mean by this is providing customers with simple usability of the products that they use, and based on in-depth expert knowledge from many years of experience in the industry, develop new, creative solutions together with customers that are specially adapted to their requirements.
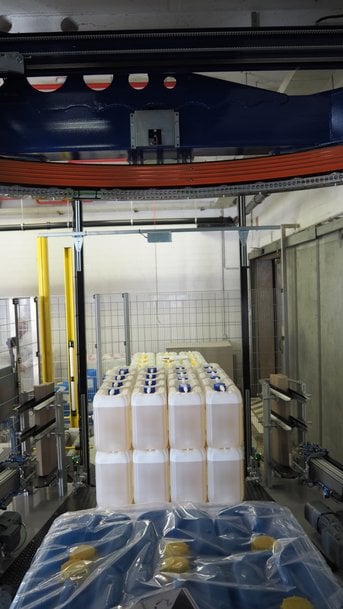
Figure 3: From primary to secondary packaging
The specific requirement: Rolling gate safeguarding
When the new TOSA film wrapper was commissioned, the rolling gate at the exit of the material flow in the direction of the warehouse was also replaced with a new one. The previous door was not safeguarded by any safety technology whatsoever. However, new additions to the machinery directive now stipulate that safety-related monitoring is mandatory. "Rolling gate protection is not that simple, since muting with sensors was hardly feasible due to lack of space – and without a consistent, holistic safety concept we would not have been given the order", says Dirk Hähner. A specific safety-related requirement was that transportation of material into and out of this danger area, which is safeguarded from unauthorized access, would take place safely in the future. Due to the lack of space in the rolling gate area, a space-saving safety solution was sought which detected the approach of the wrapped europallet on the conveyor belt, temporarily bypassed the protective field and therefore ensured that the transported material could pass through without problems. However, it was important that the protective field is only bypassed when the transported material is approaching, and that access by persons is still prevented. Until now, additional sensors were required for detecting the transport material – and therefore also for distinguishing between transport material and persons.
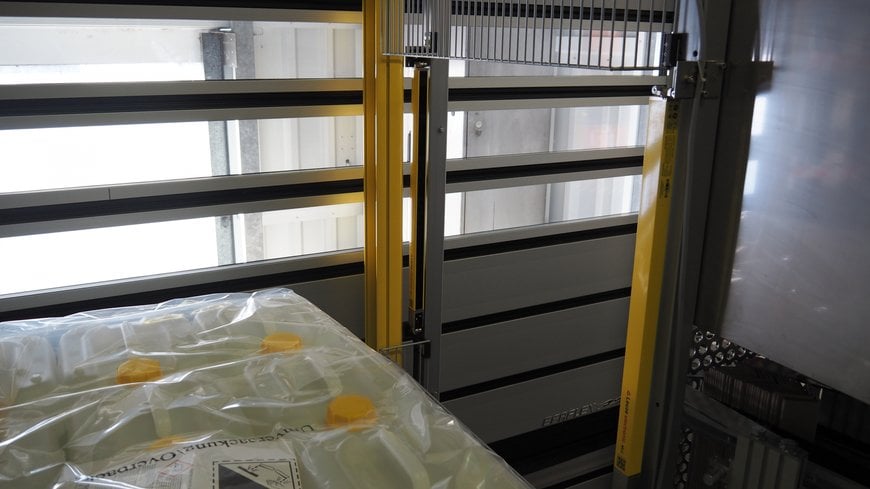
Figure 4: Rolling gate safeguarding with sensor-less muting SPG
The solution: Smart Process Gating
Dirk Hähner put his faith in Smart Process Gating, the new sensorless muting process from Leuze electronic, and succeeded in winning over the customer. This is a new muting process developed by Leuze electronic, which does not require additional muting sensors to protect danger zones which have to be safeguarded against unauthorized entry. The process is based on type 4 safety light curtains of the MLC series and integrated in the MLC 530 SPG model. The integration of an SPG application into a system is considered to be a system solution as far as safety technology is concerned. This results from the interaction of the safety light curtain, the system control and, if necessary, mechanical elements. "In order to do this, the system manufacturer requires competence and experience in safety design as well as knowledge of the relevant safety-related, international standards", says Dirk Hähner, owner and Managing Director of Industrieautomation Dirk Hähner. "For example, the gating sequence must be programmed in the PLC and the safety system solution itself has to be created."
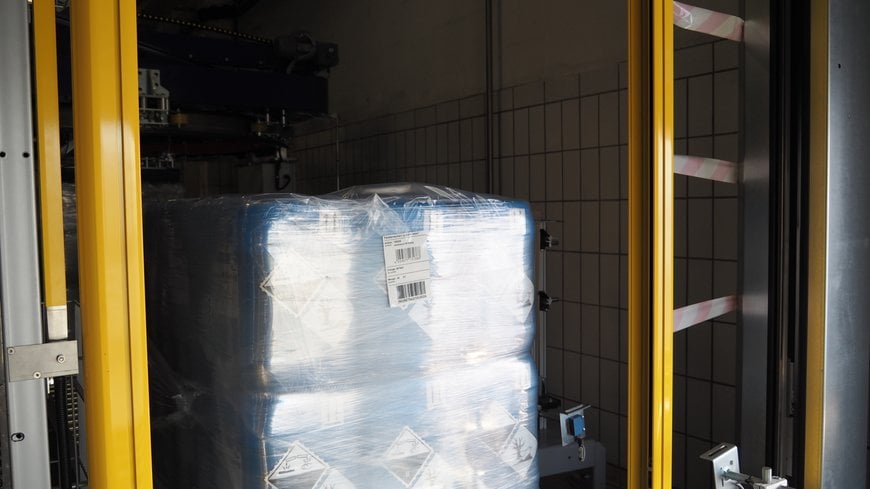
Image 5: Space-saving Smart Process Gating
Advantages of the Smart Process Gating
Dirk Böttger, deputy operations manager at Dr. Weigert, is extremely satisfied with the decision to use the Smart Process Gating application: "The pallets are transported without problems – even partial pallets with a gap between the load. The safety device operates in an extremely reliable way. The installation and service costs are kept within limits, since the omission of additional muting sensors also means that they do not need to be installed and adjusted." Overall, the system can be designed to be very compact and space-saving, because no room has to be provided in front of or behind the light curtain for muting sensors. The operators are protected, and the risk of tampering is also reduced. And something that is extremely important compared to the past: The specification of the MLC 530 SPG safety light curtains is designed in accordance with the safety-related, international standards.
About the companies
Dr. Weigert
Dr. Weigert, the developer and manufacturer of cleaning and disinfecting agents from Hamburg, already has more than 100 years of company history with the guiding principle of "No future without a past". Not only is this a commitment to "Made in Germany" but also expresses awareness and taking responsibility for hygiene, safety and protecting the environment. The medium-sized company is a leader in professional system solutions for automatic cleaning and disinfecting in laboratories and medical engineering, the large-scale kitchen sector and the pharmaceutical, cosmetics and food industry.
IDH - Industrieautomation Dirk Hähner
Founded in 2001, the company Industrieautomation Dirk Hähner (IDH) began its still quite short company history as a service provider for programming and service work on behalf of renowned production plants and machine manufacturers. Continuous project support from the planning stage to assembly and initial operation of complex industrial systems is one of IDH's core competences, in addition to control and switchgear construction.
Leuze electronic
More than 50 years experience have made Leuze electronic real experts in innovative and efficient sensor solutions for industrial automation. Its main focus is on the areas of intralogistics, packaging industry, machine tools and automotive industry as well as laboratory automation. The product range includes switching and measuring sensors, identification systems, solutions for image processing and data transmission and also occupational safety components and systems. Leuze electronic was founded in 1963 at the current headquarters of the sensor system manufacturer in Owen/Teck, southern Germany. With its extensive international sales and service network, competent consulting and reliable customer service, Leuze electronic serves customers worldwide. More than 1200 sensor people at 24 locations are involved in development, production, sales and service – supported by more than 40 sales partners around the world. Every single day, each one of them delivers the Smart Sensor Business promise to their customers: to think easy, share experience, offer proximity and create the future: www.smart-sensor-business.com
Author
Martina Schili
Corporate Communications/Public Relations
Leuze electronic GmbH + Co. KG
In der Braike 1
73277 Owen
Ph: +49 7021 573-116
Fax: +49 7021 573-199
Email: This email address is being protected from spambots. You need JavaScript enabled to view it.
Web: www.leuze.com