www.industry-asia-pacific.com
08
'20
Written on Modified on
Always in front of the right rack: Less downtime for compartment fine positioning with camera-based positioning sensors
Pallet and container racks consists essentially of vertical columns and horizontal bars. In the past 20 years, the design of these installations has changed considerably. For cost reasons, thinner-walled materials were increasingly used. The loading possibilities and range of applications became significantly larger. Racks are increasingly affected by thermal and dynamic influences and shock loads have increased, e.g., from the integration of shuttle systems. The resulting deformation of rack components under load, for example, from deflection or expansion, must therefore be considered in detail.

Permissible limiting deviations, deformations and open spaces, such as for corridor supply vehicles or high-bay storage devices that serve adjustable, single-depth pallet racks, were defined early on in European standard DIN EN 15620 "Steel static storage systems." It ensures that the functional requirements are fulfilled and, at the same time, that a suitable interaction with the high-bay storage devices is maintained.
The 200 class includes racks in which the high-bay storage devices are automatically controlled and which have a fine positioning system at the storage spaces of the loading units. For the fine positioning, influences that act on the tolerances of the steel structure in the warehouse are to be given special consideration.
In addition to mechanical tolerances from material- and mounting-related variances such as uneven hall floors, these also include wall and wind loads, elastic deformations as a function of the load state, static and dynamic loads of the high-bay storage device from different load states (empty runs, removal from storage with load), forces from acceleration and deceleration as well as thermal deformations and material expansion under the influence of temperature changes.
If one initially considers only the deformation from different load states, it quickly becomes clear that the horizontal position can change as a result of the deflection of the bar (see figure 1 and 2).
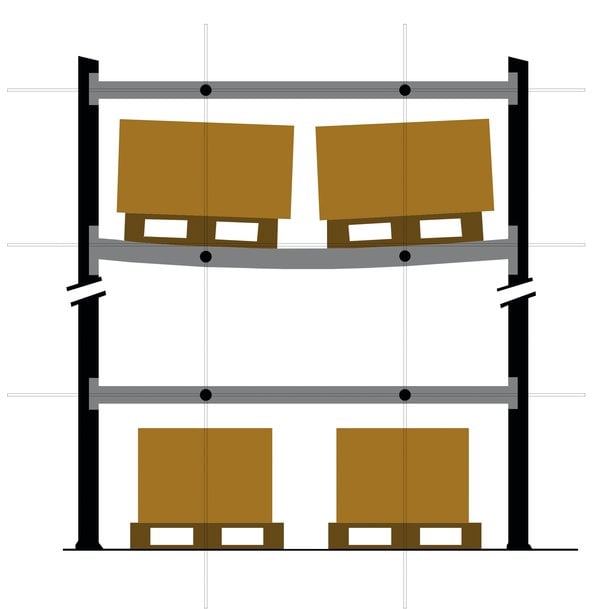
Figure 2: Loaded pallet warehouse results in a deviation of the horizontal position due to the deflection of the cross member
Just as the horizontal position can change, so too can the vertical position, as the columns can likewise deform as a result of dynamic, thermal or shock loads. It thereby becomes apparent that adherence to the functional requirements for the precise positioning of a high-bay storage device takes on special significance. For positioning in the X- and Y-direction, rough and fine positioning are generally used. Used for the rough positioning of the high-bay storage device are, for example, bar code positioning systems, optical distance sensors with long operating range or incremental transmitters. Once the approximate position is reached, compartment fine positioning performs the targeted approach of the high-bay storage device to its final position. Mounted on the load receptacle of the high-bay storage device are at least two optical diffuse reflection sensors per positioning direction – for the X- and Y-direction – i.e., at least four sensors. Without object detection, the outputs of the sensors are OFF. If a sensor detects the edge of a column or of a bar, the output state changes and the sensor output indicates ON. With the help of the new signal state, it is possible, on the one hand, to detect the direction of movement of the high-bay storage device and, on the other, to calculate the desired target position with respect to the edge. Shown in the following is the schematic arrangement of the sensors with the corresponding binary evaluation. The arrows indicate the intended direction of movement of the high-bay storage device. Other states arise in a similar manner.
The solution with binary sensors, which has proven itself over the years, has a number of disadvantages. For example, the space available on the load receptacle is extremely limited, since additional sensors are often mounted there, e.g., for the compartment occupation check, feed-through monitoring or for projection monitoring. In addition, diffuse reflection sensors can relatively easily produce faulty switching as a result of glossy profile surfaces, undesired reflection signals from edges located in the background or due to the effects of ambient light (especially HF light from energy-saving lighting installations). This results in downtimes, leading to a smaller number of storage and retrieval operations. The biggest disadvantage, however, is the complex alignment of the binary sensors – both during setup as well as during operation – meaning that all storage positions must be approached with the required accuracy. Trained, qualified personnel are required for this purpose. In addition to this is the fact that a binary sensor provides no further state information, such as information concerning the function reserve or sensor state. Similarly, new possibilities and solution approaches that arise from digitalization within the scope of Industry 4.0 for diagnosis and predictive maintenance cannot be supported.
What alternatives are available for a forward-looking compartment fine positioning solution?
A camera-based positioning system with an evaluation algorithm tailored to the specific application offers one possible solution approach here and, thus, a smart alternative to the column and bar positioning with multiple diffuse reflection sensors used up to now. This often results in a faster and more elegant approach than the previously used solution with binary sensors. Solutions where the camera and evaluation unit are integrated in a compact system are particularly popular with users. These offer straightforward commissioning and operation, without the need for special knowledge. With the IPS 200i/400i product family, Leuze electronic offers the smallest camera-based sensor available on the market for the compartment fine positioning of high-bay storage devices. By means of an additional quality score, it helps to reduce downtimes of high-bay storage devices, thereby satisfying the call for condition monitoring. Tedious mounting, aligning, and readjusting during operation is no longer required, saving the customer valuable time. Using a novel quality score, the IPS 200i/400i notifies of changes to the sensor or rack and thus assists the user in identifying possible faults early, so that predictive maintenance can be implemented: the quality score helps to identify issues such as contamination or an overhanging film at any given position. The endangered part of the system is found in due time, thus preventing a standstill of the system stemming from inaccurate positioning. The quality score also facilitates identifying particularities that may precede a system failure, so that the endangered system components can be duly removed. Maintenance times can be planned preventatively with this information, downtime can be minimized, and the cost effectiveness increased. This approach is very advantageous when time and costs are important, and it is a significant factor in terms of the total cost of ownership. Thanks to the integrated web server, all relevant data is available worldwide, without having to access the control system.
Fast commissioning and high reading performance
The IPS 200i was developed for single-depth containers and pallet warehouses and the IPS 400i for double-depth pallet warehouses. Both versions facilitate easy and quick commissioning and operation. The web-based, multi-language configuration tool with a user-guided wizard reduces the times it takes for commissioning to a minimum. The IPS 200i/400i can also be configured with XML commands or commissioned using parameterization codes printed via the code generator tool. Innovative feedback LEDs offer instant feedback, which makes aligning the sensors as easy as parking a car. Similar to an acoustic distance sensor in a car, the position of the marker is displayed in relation to the sensor by means of four LEDs mounted on the side. Each side LED corresponds to a single quadrant. If the marker is located in one of the quadrants, the corresponding LED illuminates or flashes. If the marker is in the center (coordinate origin), all four LEDs light up simultaneously. Then the sensor is optimally positioned. In addition, in alignment mode the flashing frequency provides visual indication of the distance from the marker to the origin coordinates.
The new sensor, which is optimized for depth of field, features a fixed focus position and, after rough positioning, is used for optical fine positioning of a high-bay storage device in the X or Y direction. It is capable of transmitting the correction coordinates for the precise positioning of a rack to a high-bay storage device. This is how it works: The smart sensor detects round holes (marker) or reflectors in a single-depth or double-depth bar or column of a pallet storage and determines the positional deviation of the pallets or containers in the X or Y direction relative to the target position. The sensor uses different programs for single-depth and double-depth positioning. The positioning sensor generates one or more images as the gray value. First, the sensor searches for a defined, round marking (hole/reflector) in this image. The X/Y deviation is output in millimeters to the target position or as quadrants by means of the available switching outputs. The IPS 400i covers a working range of 250 mm to 1,900 mm in a single device model, and with the optional reflector up to 2,400 mm.
Can be used in different temperature ranges
The small IPS 200i/400i dimensioned 66 x 43 x 44 millimeters with an industrial design in compliance with degree of protection IP65 is suitable both for normal temperature ranges or, with optional integrated heating, for deep-freeze use down to 30 °C. Thanks to its assembly options on three sides, the compact sensor can be flexibly mounted to the high-bay storage device. The powerful, ambient-light-independent infrared LED illumination (Light-Emitting Diode) ensures flexible use in conveyor and storage systems. It provides for a short exposure time for moving objects, and no additional external illumination is needed. The high object speed in combination with a high depth of field also supports the flexibility of the new positioning sensor of Leuze electronic. Intelligent image processing algorithms ensure reliable positioning as well as a high throughput. The FTP (File Transfer Protocol) image transfer of the IPS 200i/400i enables complete documentation of the (error) images.
Easy integration into existing network environment
With the integrated Ethernet interface (TCP/IP or UDP) and the optional PROFINET interface, both direct integration into the customer's network environment and quick, location-independent diagnostics via remote control are possible. "With the quality score, the IPS 200i/400i now makes it possible to detect the cause of standstill of a high-bay storage device early on. A significant step toward predictive maintenance, one of the most frequently mentioned applications of Industry 4.0," summarizes Sven Abraham, Product Manager Identification + Machine Vision at Leuze electronic. "Compartment fine positioning with a camera-based solution is a future-oriented and smart solution that will also be winning out in terms of cost in the long term."
Author
Sven, Abraham
Product manager Ident + Vision
Leuze electronic GmbH + Co. KG
In der Braike 1
73277 Owen
Ph.: +49 7021 573-116
Fax: +49 7021 573-199
E-mail: This email address is being protected from spambots. You need JavaScript enabled to view it.
Web: www.leuze.de
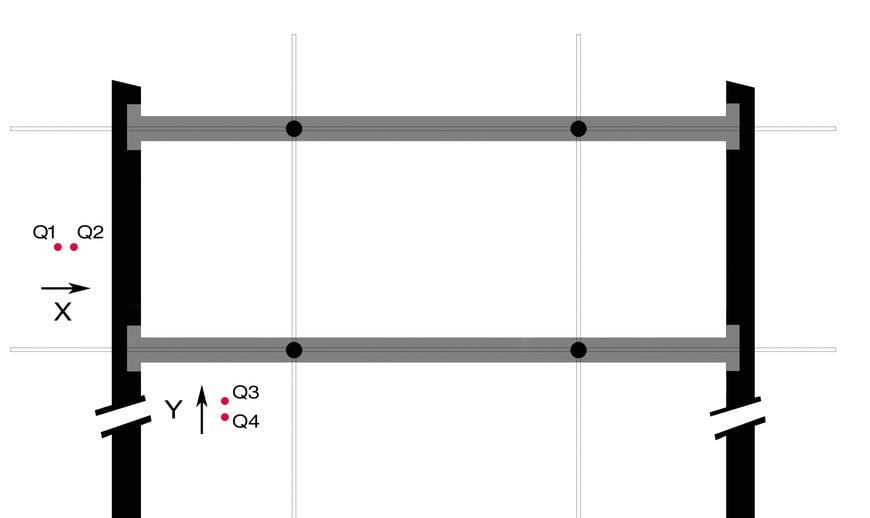
X-direction = column not yet detected
Q1: OFF
Q2: OFF
Y-direction = bar not yet detected
Q3: OFF
Q4: OFF
Figure 3: Binary switching signals on approach of the load receptacle
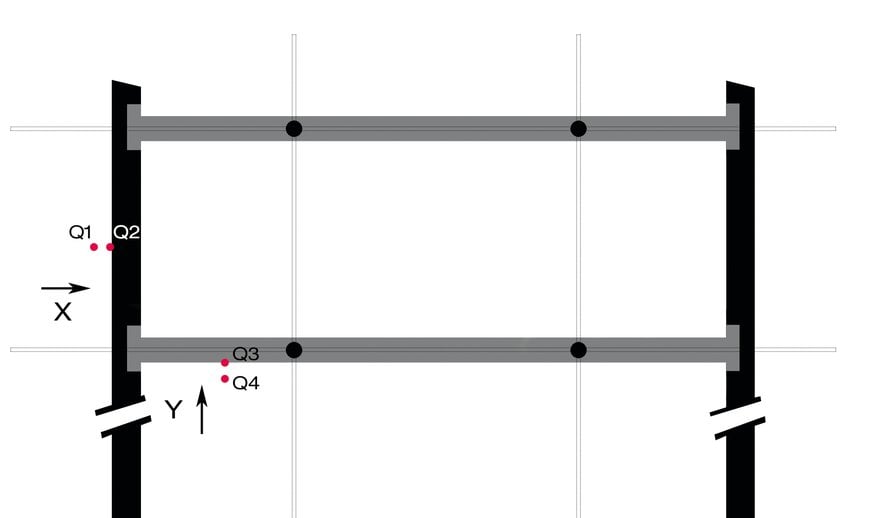
X-direction = column detected
Q1: OFF
Q2: ON
Y-direction = bar detected
Q3: ON
Q4: OFF
Figure 4: Binary switching signals upon detection of columns and bars
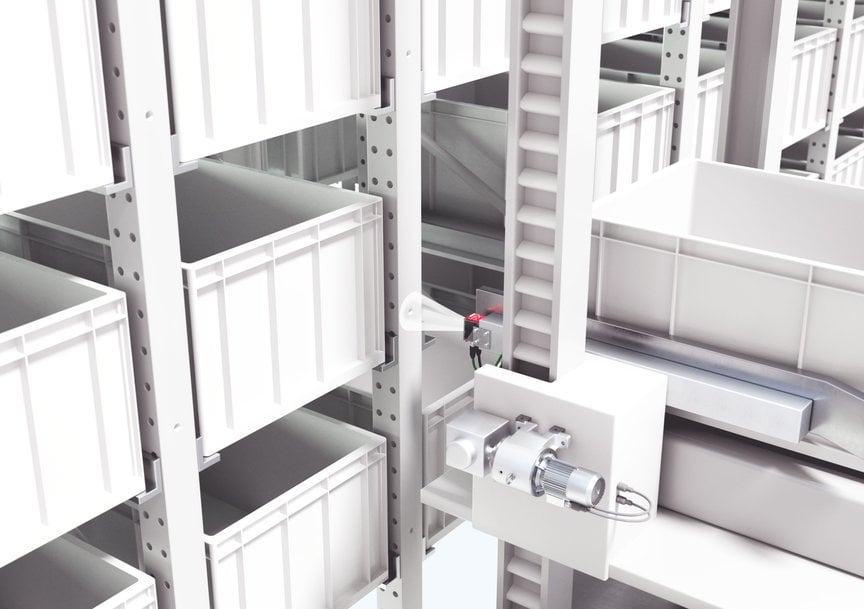
Figure 5: IPS 200i: Fine positioning on columns in container warehouse
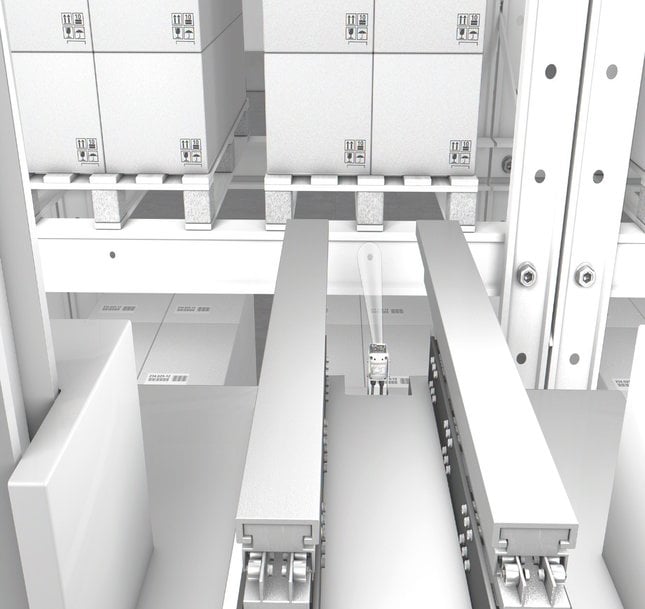
Figure 6: IPS 400i: Fine positioning on bar in double-depth pallet warehouse
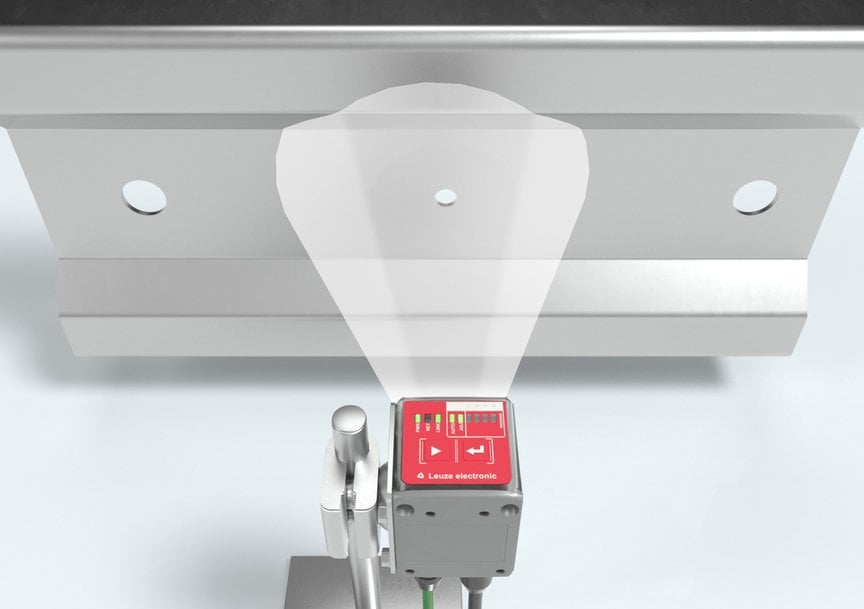
Figure 7: IPS 200i: Marker in field of view