www.industry-asia-pacific.com
06
'17
Written on Modified on
Predictive maintenance and optimal use of resources
NORD DRIVESYSTEMS is developing cost-efficient and reliable virtual sensor functions for condition monitoring.
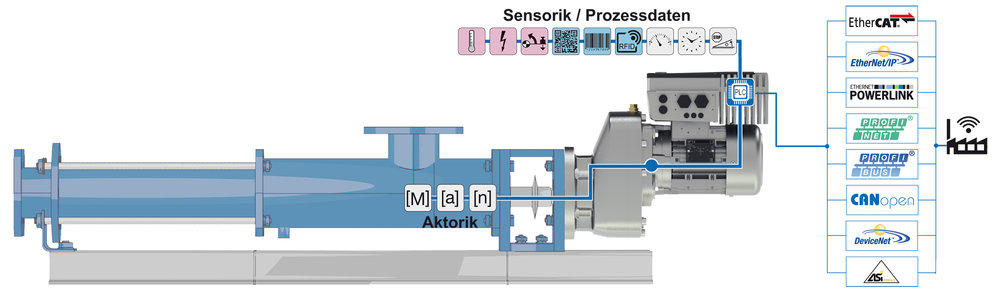
The meaning of virtual sensors is explained using the oil lifespan as an example. This is to empower drive technology to schedule maintenance dates solely based on calculations, with no expense for hardware sensors. The onboard PLC evaluates extensive operational datasets on current, voltage, and speed. From this data available in the inverter, the drive is always able to indirectly infer the current oil temperature. Taking product-specific characteristics of the lubricant into account, oil aging can be determined, allowing for optimal utilization of the lubricant. NORD has validated through testing that the calculated oil temperature curve is nearly congruent with the real, measured temperature curve. Working up to launch a fully operational solution soon, NORD is currently validating temperature curves under various load conditions. Predictive maintenance functions are expected to be commercially available in all NORD drive electronics units with an onboard PLC from late 2018.
AT A GLANCE: Virtual sensors for predictive maintenance
• Function in frequency inverters with an integrated PLC
• Precise definition of maintenance intervals helps
- reduce operating costs
- increase plant availability
• Due for launch: late 2018
• Pure software solution without hardware costs for sensors/control units