www.industry-asia-pacific.com
05
'17
Written on Modified on
Fully integrated drive packages to power parcel distribution
A new sorting and distribution center in Melbourne boasting a capacity of 35,000 parcels per hour gives Australia's largest mover of freight, Toll IPEC, an edge over competitors in the booming sector of shipping merchandise for online businesses. Conveying solutions provider BCS has built a modular, intelligent facility that quickly and efficiently takes in parcels, sorts them, and loads them onto trucks. For the configuration of the drive units, BCS relied on NORD DRIVESYSTEMS' expertise. A great number of NORD drives were selected with a particular focus on easy installation and maintenance.
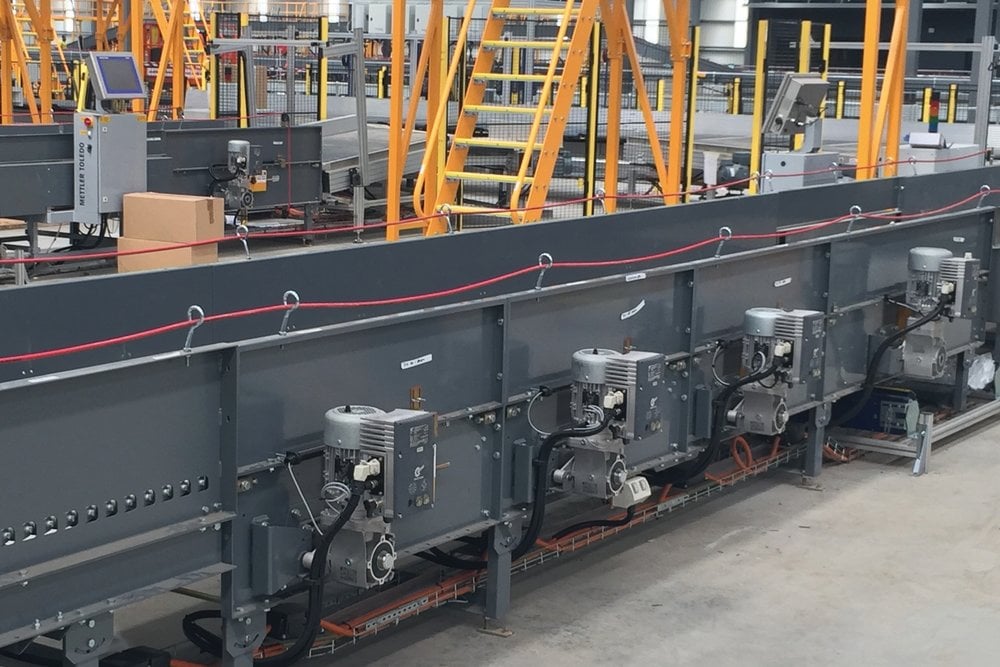
With an all-new distribution center in Melbourne adding a sorting capability of up to 35,000 parcels per hour, courier service provider Toll IPEC has instantly tripled its capacity in this great Australian metropolis and major traffic hub with an international airport. At the time of writing, this is the fastest parcel sorting facility on the fifth continent. Plant manufacturer BCS has designed and implemented an automated facility with more than 1,000 conveyor modules. This extensive installation handles everything from arrival into depot and parcel registration to tracking through the entire facility, overall system control, high-speed sorting, and loading onto trucks. The conveyors stretch across hundreds of meters and multiple levels, and it is often necessary to change belt speeds or reverse the direction at various points. "We were looking at over 1,000 variable frequency drives," says Frank Kassai, group engineering manager at BCS. "They range from 0.37 kW up to 5.5 kW."
Drive packages from a single source
NORD DRIVESYSTEMS configured all required drive sizes based on geared motors and frequency inverters manufactured in-house. The key product category were two-stage NORDBLOC.1 helical bevel gearboxes, which the company developed especially for intralogistics applications. Extremely compact and easy to handle, the gear units are nevertheless very sturdy and offer a long service life. The wide gear ratio range (i=3.58 to 70) allows for a very precise configuration to individual requirements. It is important for BCS that the gearboxes can be mounted on different-sized shafts without changes to the shafts. This way, although the facility comprises various types of conveyor modules, the variety of different drives can nevertheless be limited to an easily manageable level. Kassai also highlights the gear units' high efficiency. The inverters, too, have been especially designed for conveyance applications. The motor-mounted electronics create fully integrated mechatronic drive units. The NORDAC FLEX inverter series covers motor ratings from 0.25 up to 22 kW. Interfaces for all commercially available fieldbuses, for example Industrial Ethernet protocols, are available for networking AC vector drives in the field and connecting them to the system controller.
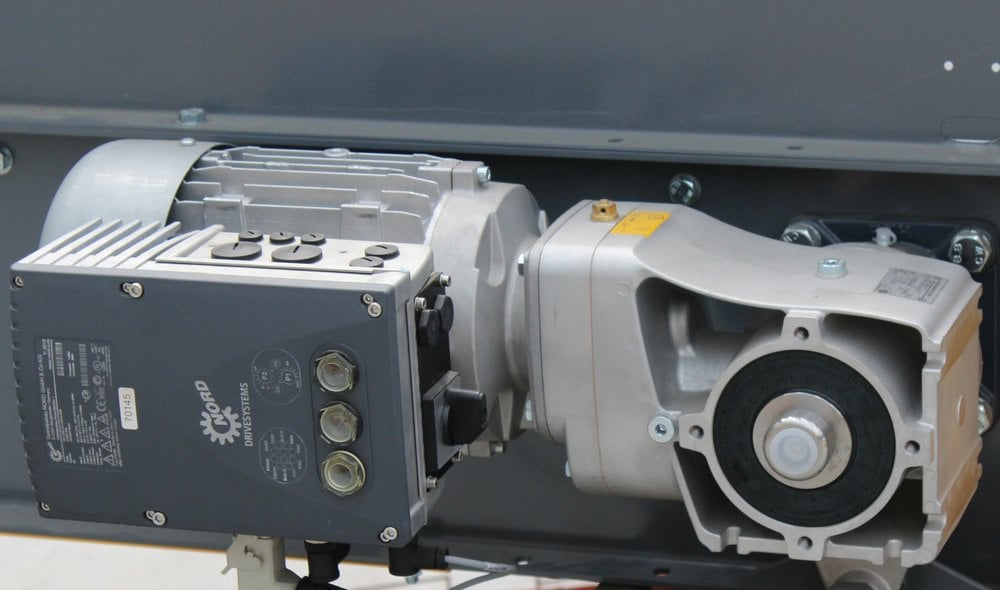
Simple, time-saving installation and commissioning
"The Toll Melbourne courier project was the largest of its kind delivered by BCS in Australia," says Kassai. "So it is nothing short of remarkable that the installation and commissioning processes worked seamlessly. We were able to save a lot of time in commissioning because NORD supplied ready-to-use drive packages, fully pre-installed and pre-parameterized." The individual units were neatly numbered according to their allocated positions, so it was easy to match them to the right conveyor module during the installation. The hollow-shaft gearboxes were fitted directly onto the machine shaft with shrink discs. They are all equipped with a torque arm, which only had to be screw-fastened to the machine frame at a single point. Thus, the installation efforts were much reduced compared to a flange mounting with up to eight screws. Kassai adds: "The maintenance and installation is made easy by the fact that NORD offers plug-in connections. This enables the operator to change a motor drive in a few minutes, instead of needing an electrician to physically rewire a new motor drive." NORD fitted each AC vector drive with a maintenance switch for easy and safe mains disconnection. If an AC vector drive needs to be replaced, the parameters can be transferred to the replacement unit using a pluggable EEPROM module.
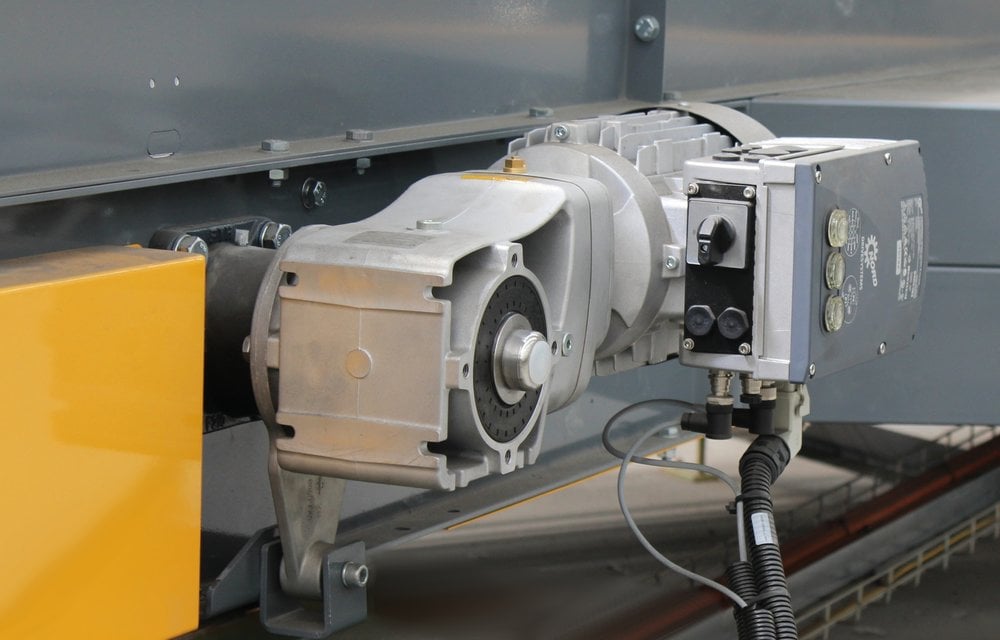
Integrated load monitor and brake management
Due to the very robust drive electronics, NORD was able to supply fully integrated, pluggable drive units, which greatly reduced the necessary cabling effort for BCS. The distributed inverters are mechanically resistant, have a high overload capacity, and resist typical interferences such as fluctuating mains voltages or rapid temperature changes. Since they also integrate comprehensive protection mechanisms, BCS saves the cost for installing and wiring control cabinet components such as motor protection switches and reversing contactors. The inverters monitor overvoltage, undervoltage, overtemperature, short circuit, short circuit to earth, and overcurrent (I²t) and thus prevent downtime, damage to the drive, and interference on the supply network. In the Toll IPEC distribution center, they are used to driving horizontal as well as inclined conveyors. Hoist technology is another textbook application for these systems in which they have been tried and tested many times over. The inverters support four-quadrant operation, i.e. acceleration and braking in both directions. They enable wear-free brake actuation, precise speed control, high starting torques, and safe torques.
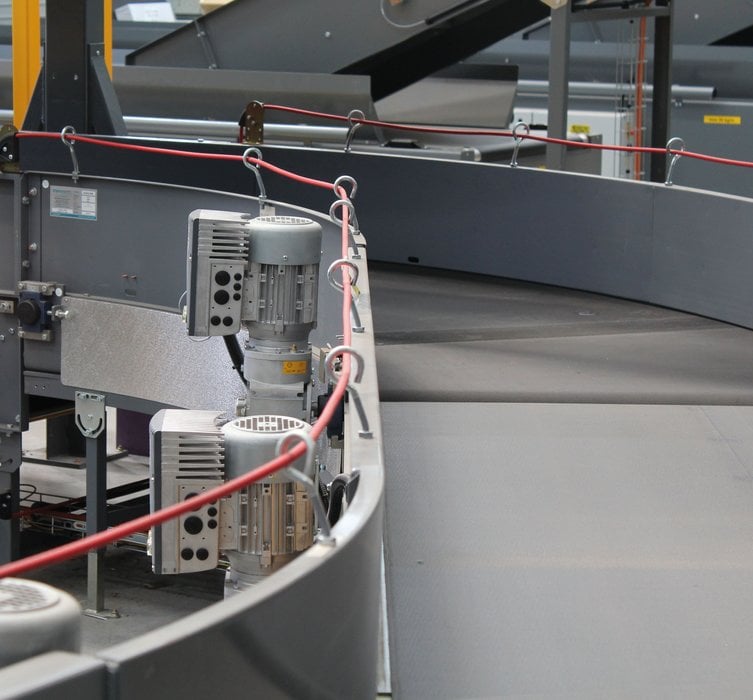
Conclusion
The distribution center is not the first joint project between BCS and NORD DRIVESYSTEMS and will not be the last. In addition to other facilities of this type, the companies have in the past also collaborated on baggage handling systems for Australian airports. The cornerstone of their continued cooperation is NORD's very reliable customer service that has always met the high expectations of BCS. Kassai says: "We are very happy with the support from NORD. Nothing has been a problem."