Reimagining the Manufacturing Workforce in the AI Era
Mr Boon Choon Lim, President of Hexagon Manufacturing Intelligence, explores how smart technologies are transforming the ASEAN workforce through digital upskilling, human-machine collaboration, and strategic change.
hexagon.com
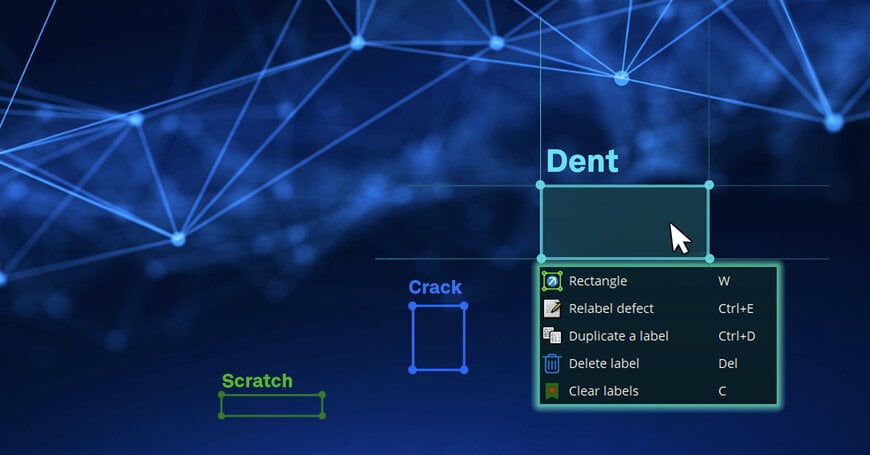
As artificial intelligence (AI) and automation gain ground in the manufacturing sector, the conversation is shifting from “what machines can do?” to “how humans and machines can work together?” In the ASEAN region—home to over 50 million manufacturing workers—this pivot is technological and profoundly human.
An interview conducted with Boon Choon Lim, President of Hexagon Manufacturing Intelligence, shares his insights on how the industry imagines the future workforce in the age of smart manufacturing. With oversight of operations across ASEAN, Pacific and Korea, Boon Choon brings a regional lens to workforce transformation and the growing need to align human capital with AI-driven innovation.
The Shifting Landscape of Manufacturing in ASEAN
Over the past five years, ASEAN manufacturers have steadily migrated from traditional, labour-intensive production models to digitally enabled smart factories. “We’re seeing a rising demand for workers who can operate digital tools, analyse data, and collaborate with intelligent systems,” Boon Choon explains.
However, this shift is not uniform across the region. Singapore and Malaysia are leading with supportive digital frameworks, while countries like Indonesia, Thailand, and Vietnam are advancing at varied paces, often with discrepancies between urban and rural areas.
As automation becomes more pervasive, the nature of factory work is being redefined. “AI is not just about replacing people—it is about augmenting human capabilities. We are seeing predictive maintenance, AI-driven quality control, and real-time analytics transforming the factory floor,” he notes. For instance, tools like Hexagon’s HxGN Visual Detection are revolutionising quality control by providing advanced visual detection capabilities that enhance human oversight and precision.
Boon Choon estimates that the demand for digitally skilled professionals in ASEAN will rise by 15–20% annually, even as low-skilled roles face increasing obsolescence.
The Human Impact of Automation
The shift towards automation inevitably comes with human consequences. “Routine roles like traditional machine operators and manual quality inspectors are increasingly being replaced, leading to pockets of retrenchments in the region, particularly in larger, export-driven factories,” says Boon Choon.
The disruption extends beyond job losses. “The psychological impact on the remaining workforce is significant. There’s anxiety—fear of redundancy and uncertainty about career paths,” he adds. To address this, companies must handle the transition with empathy and transparency.
At Hexagon, workforce transition is managed with an emphasis on continuous learning and cross-functional mobility. “We encourage our people to see career shifts as opportunities for growth. It is about creating a culture where learning never stops,” he concludes.
Transforming the Workforce Strategically
For manufacturers planning to automate, Boon Choon outlines a clear roadmap: begin with a skills gap analysis, establish transparent communication, and choose the right implementation timeline—whether phased or fast-tracked.
“Too many companies jump into automation without preparing their people. You need to bring your workforce along the journey from day one,” he advises.
Open channels of communication—townhalls, feedback loops, and employee workshops—are critical. “Change is easier to manage when employees understand the why and how behind it.”
Upskilling for the AI Age
In today’s AI-integrated manufacturing environment, data literacy, systems thinking, and robotics programming are among the top must-have skills. However, Boon Choon points out that soft skills such as adaptability and problem-solving are equally critical.
He emphasises the importance of skilling by demonstrating how workers can transition from traditional roles to advanced positions through targeted training. “With the right training, employees not only retain their jobs but can also advance and take on mentorship roles.”
To support these transitions, Hexagon collaborates with technical universities and conducts hands-on workshops, ensuring the development of a future-ready manufacturing workforce across ASEAN.
Advice for Workers at Every Level
When asked what advice he would give to manufacturing employees navigating this shift, Boon Choon outlines a clear path by level:
- Shop floor workers should start with the basics—interacting with digital tools, understanding diagnostics, and reading the data dashboard
- Mid-level engineers must evolve into systems thinkers, capable of optimising processes and integrating complex technologies
- Executives need to embrace digital strategy and lead their organisations through transformational change
Looking ahead to the next three to five years, Boon Choon identifies emerging skills like AI operations, human-machine collaboration, cybersecurity, and sustainable manufacturing as essential. “It’s about developing ‘hybrid’ professionals who can bridge domains—technical, digital, and strategic,” he says.
A Vision for the Future
Boon Choon envisions a dynamic ASEAN manufacturing workforce that thrives alongside intelligent systems. “Humans will focus on creativity, strategy, and ethics, while machines take on data-heavy, repetitive work. That synergy is where the real value lies.” He sees entirely new job categories emerging, including AI maintenance specialists, digital twin analysts, and sustainability technologists. “These roles did not exist a decade ago,” he adds.
With tools like Hexagon’s HxGN Visual Detection, manufacturers can enhance precision and efficiency, allowing human workers to focus on higher-order tasks that require strategic thinking and innovation. Additionally, Hexagon's new AI-powered automation tool called ProPlanAI, reportedly slashes machine tool programming time by up to 75%, exemplifies how advanced technologies can drastically improve workflow efficiency and empower workers to engage in more meaningful roles. This reduction in programming time not only boosts productivity but also allows employees to allocate more time to creative problem-solving and strategic planning.
“ASEAN, with its youthful workforce and advancing digital infrastructure, is well-positioned to compete on the global stage—if it can accelerate workforce transformation,” Boon Choon asserts. The region's ability to adapt to these changes will determine its future success in the global manufacturing arena.
Final Thoughts for Industry Leaders
Boon Choon concludes with a message to Human Resources professionals and manufacturing leaders: “Invest in people, not just machines. Start early, communicate clearly, and build a culture of continuous learning.” He stresses the importance of aligning technological investments with human capital development to ensure a seamless transition into the AI era.
His final reminder: “AI is not the end of human jobs—it’s the beginning of smarter, more meaningful work. The future belongs to those who are ready to learn, unlearn, and relearn.” By fostering an environment of continuous education and adaptation, ASEAN manufacturers can create a resilient workforce capable of thriving alongside AI and automation.
The integration of AI and automation in manufacturing presents both challenges and opportunities. By strategically transforming the workforce and leveraging advanced technologies, ASEAN can lead the way in creating a harmonious and productive future where humans and machines work together seamlessly.
www.hexagon.com