www.industry-asia-pacific.com
18
'16
Written on Modified on
Eplan Harness proD 2.6 Comprehensively carefree through to manufacturing
Efficiency ranks first, but the joy of designing doesn’t get short shrift: the new Eplan Harness proD version 2.6 is an intuitive 3D/2D software that covers all of today’s requirements for wiring and wire harness engineering. New features include enhancements to production specifications, which include cable drawings in addition to the nail board. Cable dimensioning is now automatic. If desired, cables with predefined length can easily be routed in an intuitive fashion. Cooperation between mechanical and electrical engineering becomes true team-work with open interfaces.
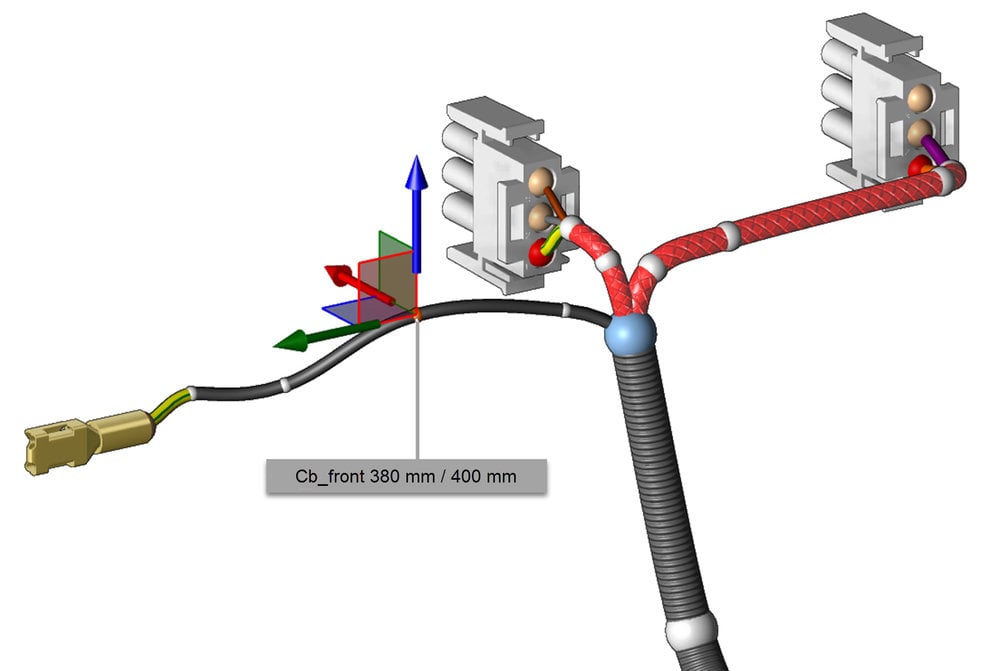
Monheim/Nuremberg, 22 November 2016 – The new Eplan Harness proD version 2.6 software from Eplan for convenient cabling and wire harness engineering is ready for release. Based on the 3D model of the mechanics and electrical schematics, the wire harness can be designed in an intuitive manner. The next step is the handover of this data to manufacturing, and there have been major updates in this area as well: integrating 2D cable drawings, which are automatically derived from the 2D/3D design environment and that specify both dimension points and connection points. This allows for automatic dimensioning, saving valuable time and ensuring correct results. Stripping lengths and wire coatings can now also be defined in the design phase, and professionally depicted in the manufacturing drawings. This provides users with a quick and comprehensive overview of their projects.
Determining lengths
Wiring harness software normally offers the suitable tools of the trade to easily calculate cable lengths. In Eplan Harness proD 2.6, this now also works the other way around: users may predefine a fixed length – for antenna cables (as an example). During the design process, the current as well as the targeted length are exactly depicted and users can recognise at a glance how the wires can optimally be routed. This simultaneously allows for the reduction of variations, resulting in cost savings in warehousing and manufacturing. Additional functions for the creation of cable units allow elements to be grouped together as well as the assignment of component numbers to cable units, thereby providing a more comprehensive project overview.
Optimally integrated
The connection to Eplan Platform and system openness to MCAD and ECAD ensure a continuous workflow between electrical engineering and mechanical engineering. Another new feature is that Eplan projects can be transferred directly into the wire harness software with version 2.6. Not only that, but Eplan Platform’s central parts management supports integrated data storage as users must only maintain master data in one system. This allows for integrated working processes for wire harness engineering from the schematics to manufacturing. The ease of use and integrated data in every phase of design through to manufacturing thereby lay the groundwork for quick and efficient results.
Individual fields of application
Numerous functional enhancements in the system contribute to making cabling design and wire harness projects more efficient and to accelerating customers’ workflows. Eplan Harness proD supports all industries in which cables and wire harnesses must be routed, for instance special vehicles, equipment manufacturers, wiring/wire harness prefabrication, machinery manufacturers and company divisions where interdisciplinary cooperation is required.
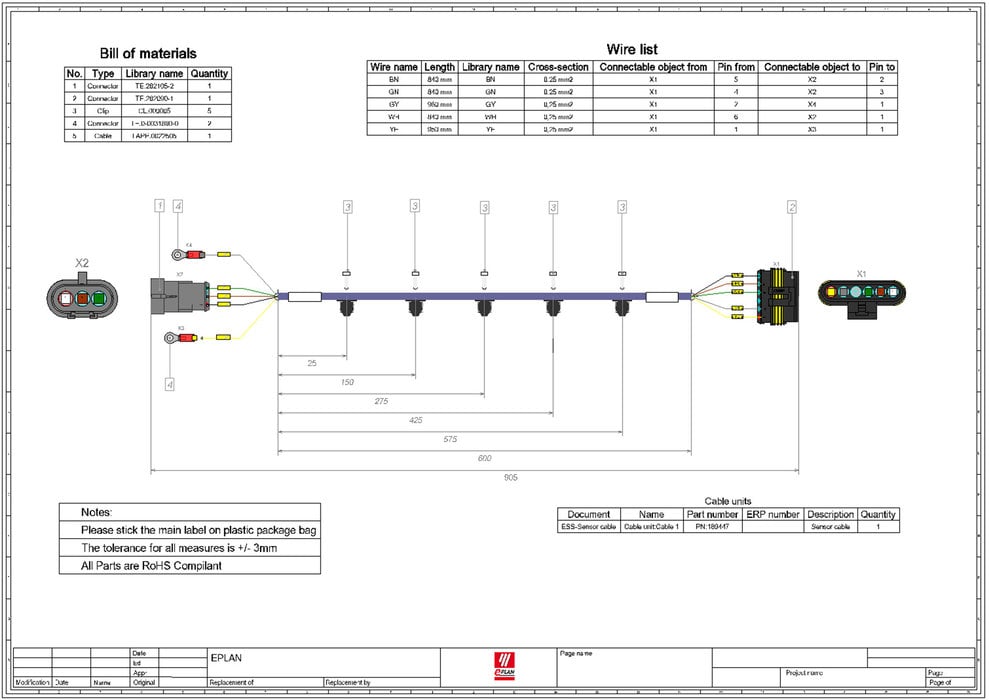