MELFA ASSISTA robot automates the application of double-sided tape in collaboration with workers
Working together, TOPPAN Inc.’s Chubu Business Division, and HEXA Co., Ltd. developed a Mobile Robot System, that automates the task of applying double-sided tape at manufacturing facilities.
www.mitsubishielectric.com
Established in 1900 as Toppan Printing Limited, TOPPAN Inc. is the core company of TOPPAN Holdings (renamed in 2023). The Chubu Business Division has three manufacturing sites in central Japan, providing solutions to companies in sectors ranging from information and communications to lifestyle and industry. As part of a recent project, it set out to develop an automated system to apply double-sided tape as a solution for manufacturing sites.
“Double-sided tape is often used as an adhesive method in production facilities. At many manufacturing sites, human workers manually apply this, so we identified that there was an opportunity to benefit from automation,” explains Muga Yamaguchi, head of the SX Business Promotion Department, Business Production Section 1, TOPPAN Chubu Business Division.
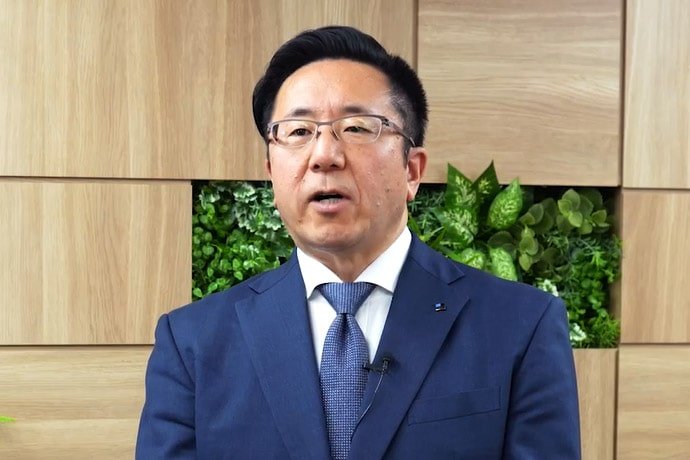
Muga Yamaguchi, General Manager, SX Business Promotion Department, Business Production Section 1, TOPPAN Inc, Chubu Business Division
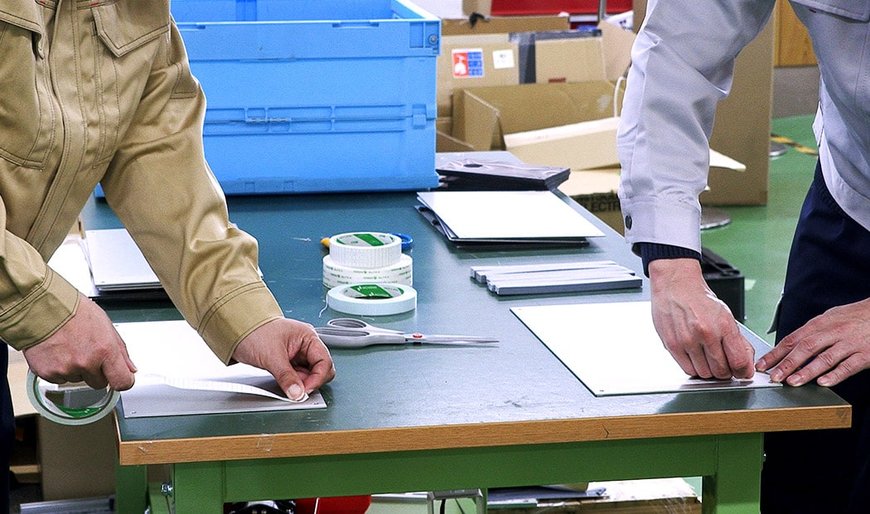
Double-sided tape is often applied manually at manufacturing sites, making it an ideal process for automation
To support its goal of automating tape application with robots, selecting the appropriate tape was crucial. The company decided to work with HEXA Co., Ltd.’s “Mobile Tape” product. This double-sided tape, has several features that lend it towards automated application such as its stripe “wave-pattern” design of the adhesive. The companies decided to work together on the project, however, they soon realized that there was one significant challenge to overcome – there were often other people working in the area where the tape application process was situated.
A workspace shared by robots and human workers
The industrial robots used at manufacturing sites are typically designed for mass production, focusing on quickly moving large workpieces. Since this involves heavy machines moving at high speeds, a collision between a robot and a human could result in a serious accident. Therefore, it is crucial to always maintain a safe distance between robots and people, such as by placing safety fences between them.
However, according to Toshihide Waku of the SX Business Promotion Department, Business Production Section 1, TOPPAN Chubu Business Division, “In manufacturing sites that use double-sided tape manual work is often still required before and after the automated part of the process. Therefore, robotic solutions need to be able to work closely alongside human workers.”
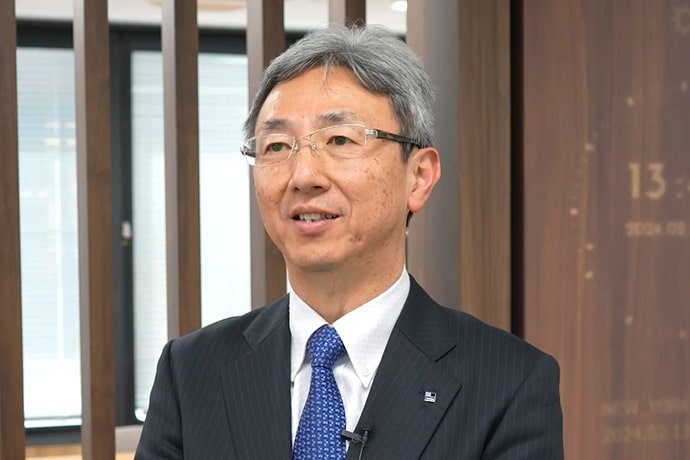
Toshihide Waku, SX Business Promotion Department, Business Production Section 1, TOPPAN Inc, Chubu Business Division
Since it would be impossible to maintain a suitable distance for using conventional industrial robots, the main challenge for the automated tape application became finding a robot that could carry out the required task while also ensuring worker safety.
To address this issue, TOPPAN turned to MELFA ASSISTA, Mitsubishi Electric’s collaborative robot. It offered compliance with international safety standards, as well as enhanced safety features such as automatically stopping operations when it detects a person nearby, enabling it to safely share a workspace with humans.
Applying tape in three-dimensions
In December 2021, the development project began by applying HEXA’s double-sided Mobile Tape to various workpieces using the MELFA ASSISTA collaborative robot and then assessing the performance. The combination of the Mobile Tape’s striped wave-pattern based adhesive, allows it to be applied in curves, not just straight lines.
“By adding a suspension function to the tape head we could ensure reliable contact with the object.” explained Yoshihide Nishikawa, representative director of HEXA Co., Ltd.
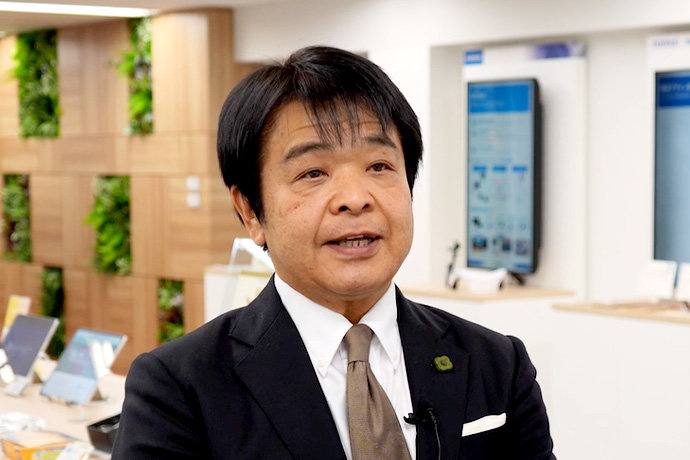
Yoshihide Nishikawa, Representative Director, HEXA Co., Ltd.
Although this allowed the double-sided tape to be applied to flat workpieces without any problems, it needed refinement for three-dimensional objects. This was to allow for individual differences between workpieces and subtle differences in the tape attachment position.
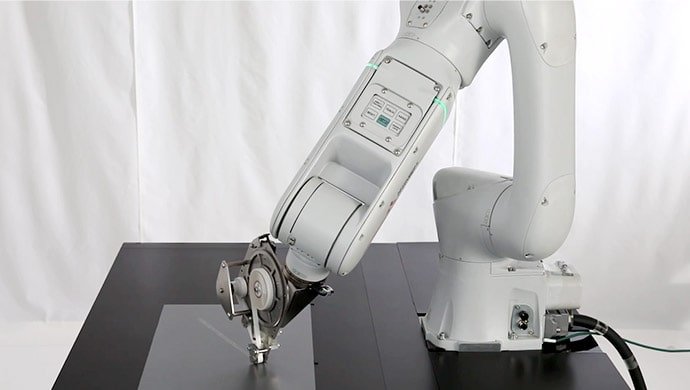
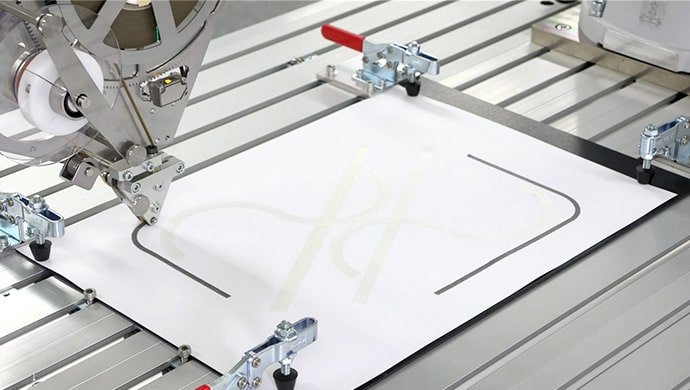
Automated double-sided tape application system using MELFA ASSISTA (Above). The adhesive on the Mobile Tape has been applied in a striped wave-pattern, allowing the tape to be laid down in curved shapes (Below)
The development team realized that the problems with the tapes adhesion were caused by fluctuations in the tape application pressure due to misaligned workpieces. Although they managed to absorb some these fluctuations by improving the suspension system, the team realized that a complete solution would require an active control function for the tape application pressure, so they consulted with Mitsubishi Electric for help.
In response, Mitsubishi Electric suggested using a force sensor, which is available as a peripheral device for the robot. Once attached to the robots ‘wrist’ the force sensor could detect the tape pressure and three-dimensional movement when the robot interacted with the workpiece. By controlling this it allowed the robot to apply a constant pressure to the tape head, no matter which direction the robot hand was facing.

By using a force sensor to control the pressure applied to the tape head, tape can be accurately applied to curved surfaces.
Also effective for traceability and predictive maintenance!
The introduction of the force sensor also brought additional benefits. By continuously monitoring the applied force, this data could be used to improve traceability through the captured data. Further analysis of the data also helped with early fault detection and predictive maintenance.
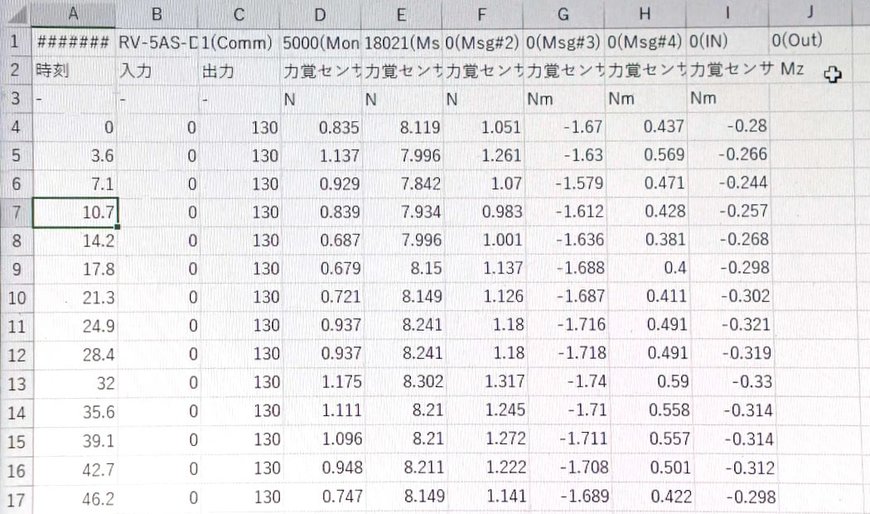
The log from the force sensor is used for traceability and predictive maintenance
The Mobile Robot System, developed as a solution to automatically apply double-sided tape, was made possible through the cooperation between the three companies – TOPPAN, HEXA and Mitsubishi Electric.
“We believe this solution can be deployed at a wide variety of manufacturing sites, such as those producing materials for domestic appliances and vehicles, not just in packaging and wrapping processes,” says Yamaguchi. “Japan’s declining birthrate and ageing population means it is becoming harder for companies to find workers, and employment costs will continue to rise. Companies need to streamline work processes to address these issues. I am confident that our Mobile Robot System technology will be useful for achieving this.”
Find more information about the solution in our video