www.industry-asia-pacific.com
22
'16
Written on Modified on
Perfect Printed Images with Long-Term Guarantee
PrintJet ADVANCED for industrial switch cabinet labelling
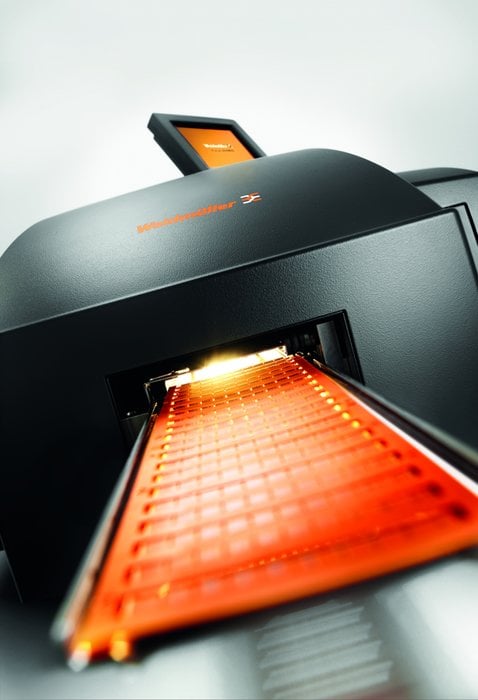
Two FAULHABER motors take care of precise transportation of material through the print unit and fusing unit. Everything literally comes together in the switch cabinet: cables, fuses, relays, transformers and connection points. Only when everything is properly connected to each other, can electrics and electronics do their job correctly and sustain the operation. The plans for the wiring are of course done on computers today. The planning system also produces the contents for labelling the components at the same time. Weidmüller has developed its own M-Print® PRO software which takes this data and forwards it to industrial-compatible specialised printers in the appropriate format. Polymerisation under heat The latest generation of Weidmüller printer, the PrintJet ADVANCED, is also designated with the internal-company abbreviation, PJA.
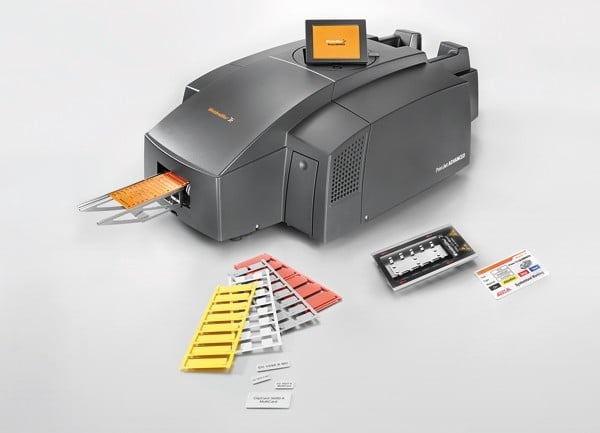
It has four printing cartridges, black, cyan, magenta and yellow which are applied via the print head onto the printed ma terial in the multipass process. This is where the similarities to the common office printer come to an end. The ink is an in-house development and anything but the usual printer ink. It is water-based similar to conventional ink but it is specially designed for non-absorbent surfaces. No moisture is transferred to the surface as what happens when printing on paper. Instead, it is fixed in place and polymerised using heat exposure. In doing so, the molecules in the ink combine into long, stable chains. This reaction is triggered by infra-red light and temperature. Afterwards, the imprint is wash and scratch resistant, withstands petrol, drilling oil, hand sweat, acetone, a multitude of solvents and detergents as well as most chemicals. The polymerization process thus determines the durability of the imprint. “The imprinted plastic or metal marker travel through a fusing unit with infra-red radiators and are exposed to a defined temperature for a few seconds.This process takes a bit longer with metal markers”, says Michael Gockel, Lead Developer for markers and tools at Weidmüller, describing the fusing process. “When doing this, it is a matter of having a precise, reproducible passage in order to guarantee that the amount of heat that is applied is consistent. If the cards pass through too quickly, the fusing remains incomplete, the ink would not be sufficiently firm. In the opposite case, too much heat would be applied and the material would be subjected to unnecessarily high temperatures.” So that neither of these things happen, the motor that transports the cards through the fusing unit must run absolutely evenly.
This is implemented at this point by a so-called flat rotor motor that is only 7 mm long, the FAULHABER DC motor 2619. An integrated speed controller ensures that the speed is consistent and its high output torque also ensures that there is uniform power output even under load. Together with the 12 mm long gearhead, the entire drive measures less than two centimetres – a crucial advantage since a lot of technology is housed in the smallest space in the housing of the special printer. The length of the drive would be two to three times longer with conventional technology. Perfect speed control At the beginning of a print job, a multicard contain ing up to 200 individual labels falls out of the integrated magazine onto a conveyor and is transported into the start position before printing. “Previously, we used a simple motor at this point for this short transport whose speed could fluctuate by up to 20 % of the set point. This deviation was extremely difficult to be compensated for. Thanks to a new motor from FAULHABER, we can now save ourselves this effort and additional adjustments during transportation is no longer needed.” The already mentioned motor from the fusing unit also synchronises the transportation of the cards through the print unit. The requirements there are quite similar as in the fusing unit.
The start position is checked during referencing, the card in the print unit advances and printing starts. “Material and labels are precisely placed by referencing”, explains Michael Gockel. “So that the print head always reaches the correct position, transportation of the multicard must be carried out absolutely precise.” The coupling of print unit and fusing unit, that previously had to be separately controlled, now functions without problem since the two identical motors for the “printing and fusing” areas ensure that there is a smooth transition without further support. “Their performance data is integrated into the control software”, explains the development manager. “Reliable function of the drive makes each additional control or program adjustment redundant – they automatically run synchronously.” Customer-specific modification Experts from FAULHABER were also involved with the development of the PJA. They did not just provide the usual detailed advice and application-specific design of the drive. “So that it is perfectly suited to the printer, we did some modifications to the motor”, reports Thomas Kraus, who supervised the project at FAULHABER. “Among other things, we adapted the connector and the stranded wire, fitted the cable with a strain relief, modified the length of the motor output shaft and fitted a surface to it for attaching a wheel. Furthermore, we have re-parameterised the control board and adjusted the control frequency to get the best possible concentricity. The unit therefore provides an integrated speed control function which, for example, ensures that the plastic and metal cards, which have different weights, are always consistently transported at the correct speed.” Michael Gockel remembers the technical exchange well: “The collaboration was very intensive and extremely successful.”