www.industry-asia-pacific.com
16
'16
Written on Modified on
A 7-Joint Arm Robot Performing 'T'ai Chi Ch'uan'
Elmo’s Ultimate Multi-Axis and servo solution incorporated in the design and development of the first Chinese Collaborative Robot by Siasun, China
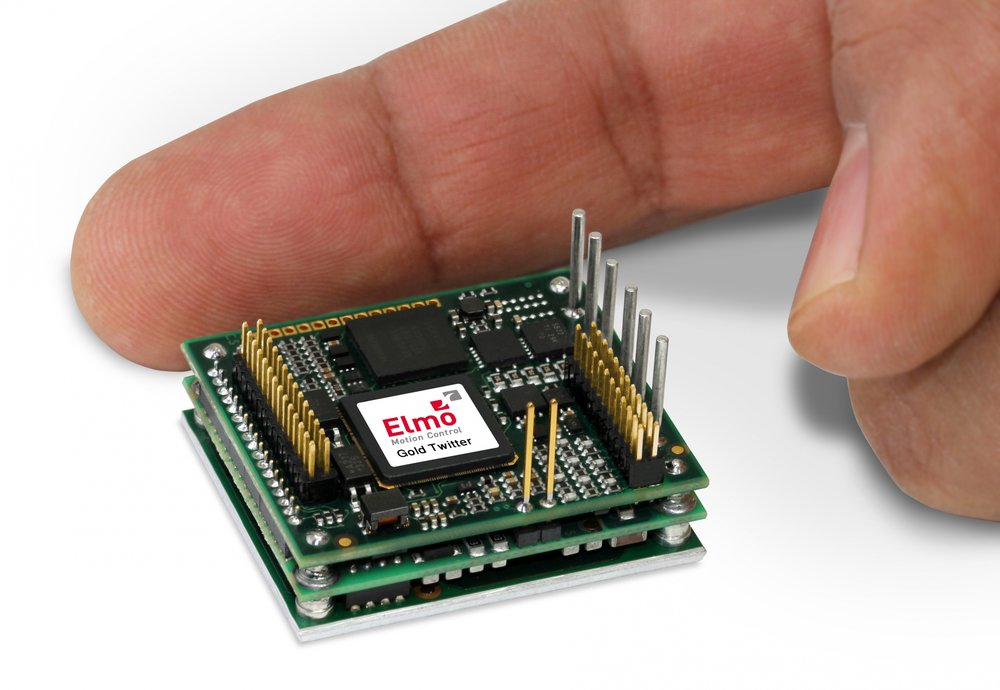
Elmo Solution
The Servo Drives
Elmo's ultra-small and powerful EtherCAT Gold servo drives were selected for the challenging task. The drives were mounted directly onto the robot joints, and were a perfect choice for maintaining the small size and compactness of the robot. Two powerful ultra-small Gold SOLO GUITAR drives were used to drive the two base joint motors that support the whole mechanical structure of the robot. The ability to drive the motors with continuous current of 50 Amps and high peak current of up to 100 Amp allowed reaching the required high speed, acceleration, and deceleration operation rates. Additional five miniature Gold SOLO WHISTLE drives capable of running 20 Amps continuous current, and up to 40 Amps peak current were used to operate the additional five robot joints. Each drive in the system operates at maximum speed, acceleration and deceleration rates, yet also required to operate at slow speeds with extremely high accuracy and precision. Such polar opposite operation using same drive is made possible by the exceptional 1:2000 dynamic current range, and the very wide bandwidth response of the drives. A drive with a sufficiently small physical footprint such that it could be mounted directly onto the robot joint, was the only option for such complex project. Positioning the drives in close proximity to the servo feedback resulted in minimum cabling, minimum influences of external noise, low EMI and RFI, and overall dramatic increase in the reliability of the system.
The EASII (Elmo Application Studio)
Elmo’s highly advanced yet simple to use configuration tool, the EASII, (the tool that “does it all for you”) assisted in tuning each of the individual drives in the network to their highest level for optimized servo performance. System Identification and suitable controller design, using high order filters to overcome imperfections in the mechanical structure, were just some of the tools implemented to elevate the system to its highest possible servo performance. Further, multi axis identifications using simplified and advanced identification methods with special position gain scheduling to eliminate the crossover-effects between the various axes were implemented. Many other feature were used in this application, all for operating the system with the highest possible bandwidth, fastest response time, and simultaneously maintaining stability and smooth robot operation with high margins.
The Platinum Maestro, the Ultimate Multi- Axis Controller
Elmo’s proven ability to support a wide range of built-in robot kinematics using its advanced multi axis controller, the Platinum Maestro (P-MAS), with mechanisms such as Cartesian, SCARA, 3- link, Delta etc. makes it easy to answer any robotic challenge. The built-in kinematic support operates in either MCS (Machine Coordinate System) or PCS (Product Coordinate System) with full synchronization to turn tables, conveyors and other external equipment. In addition, the P-MAS has a special real-time code section for user applications. This special code section enables robot developers to write their own specific robot kinematic equations, enabling the P-MAS to support any highend, unrestricted robot types available today, where users can implement their own specific kinematics. The P-MAS, which is based on the newest 4-Core powerful processor is essential in this kind of applications requiring real-time calculation of the robot kinematics and inverse kinematics within network cycle time of 250µSec. The kinematic equations implemented in the user input real-time section, calculate the target positions/velocities or torque of all the axes in the system and output them on each EtherCAT cycle. The robot operation is divided into two main modes; the first is the operation teaching mode, and the second is the working mode. In the teaching mode, the operator physically moves the robot to key position points along the wanted path trajectory. The multi axis controller records the relating position points in order to repeat the whole trajectory motion in the working mode. The drivers operate under cyclic synchronous torque (CST) mode of operation during this mode. In addition to the torque command, the multi axis controller outputs additional compensation current (torque) in order to overcome resistance factors, such as gravity and robot dynamics, while maintaining a smooth dragging process. One of the highlights of such complex robotic solution is the implementation simplicity of the teaching process for the non-programmer, where most tasks could be accomplished with no programming experience or skills whatsoever. The second mode of operation is the working mode, where the multi axis controller calculates the seven target position/velocities according to kinematic model of the robot (Inverse kinematic solution of DH matrix), and if necessary, compensation of the torque based on the dynamic model is added to the total output torque. The drivers operate under cyclic synchronous position (CSP) or cyclic synchronous velocity (CSV) mode of operation, receiving target position/velocity commands and torque offset commands.
Solution highlights
-Unbeatable servo performance.
-250 us cycle time for up to 16 axis fully coordinated and synchronized
-Small size servo drives with very high power rating mounted right on robot joints
-High dynamic current range for high speeds and high precision
-Dual loop control capability
-Ability to communication with variety of feedback devices (incremental and absolute encoders)
-Using powerful Multi Axis Controller for synchronization and robot motion implementation
-Fast EtherCAT real time serial deterministic networking
-Optimized servo performance -very fast response time as a result of extremely wide control loop Bandwidths
-Powerful EASII enables easy robot configuration and implementation
-Top efficiency, utmost reliability
-Ultra rugged, the drives can be mounted anywhere.
-Low EMI , RFI
Summary
Elmo’s Smart, Small, and Simple servo and motion solutions boost the performance and enhance the functionality of Siasun’s newest technology - the collaborative robot