Ultrahigh precision wire-cut EDM meets customer’s precision requirements
Kato Seisakusho Co., Ltd. uses Mitsubishi Electric’s MP2400 ultrahigh precision wire-cut electrical discharge machine (EDM) to manufacture press dies for automotive components that need to meet the strict requirements of the industry.
www.mitsubishielectric.com
Key Points
1. Mitsubishi Electric’s MP2400 was used for a collaborative industry-government-academia R&D project that required a high level of precision in processing.
2. The finishing process can be done on the same machine, eliminating the need for a separate unit.
3. Mitsubishi Electric’s 20-year guarantee and service support mean its products can be used with confidence.
The company, which has its headquarters in Kani, Gifu in Japan, originally introduced the unit to support a collaborative R&D project, but it is now meeting the precision requirements of metal molds for automotive parts.
Founded in 1947, as a manufacturer of toy cars, Kato Seisakusho Co., Ltd. later expanded to produce components for clocks, kerosene stoves, gas appliances and water heaters. Delivering components to many businesses in different industry sectors, the company gained expertise in advanced technologies, including press working and mold manufacturing. It is now mainly engaged in metal pressing processes for automotive components, such as parts for fuel pipes, airbags and engines.
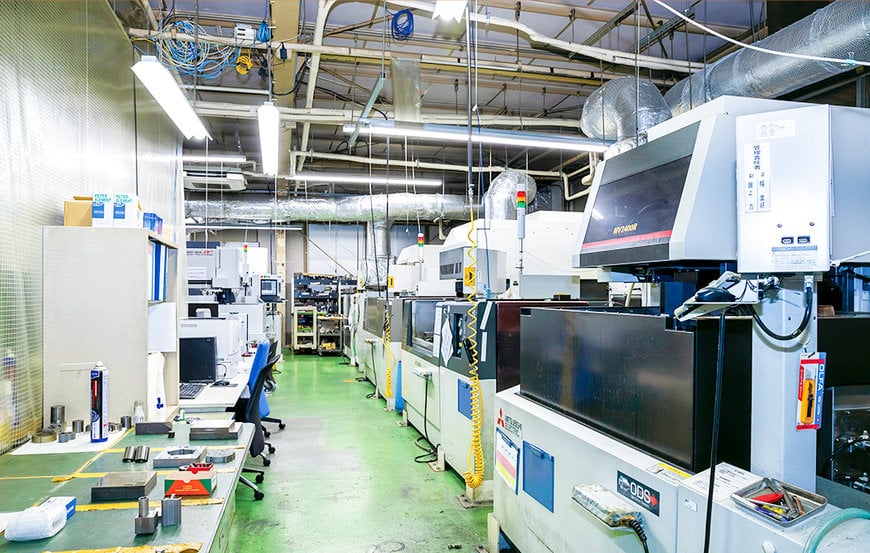
This production hall contains Mitsubishi Electric’s EDMs: MV2400R, FA20, FA20P and FA20PS are on the right of the picture, with the ultrahigh precision MP2400 and EA12V on the far left. Kato Seisakusho is a longstanding Mitsubishi Electric partner and uses the company’s processing machines as well as other products.
At its facility, the company uses Mitsubishi Electric machines, namely the MV2400R, FA20PS, FA20P and FA20 wire-cut EDMs and the EA12V die-sinking EDM. In 2016, Kato Seisakusho introduced the MP2400 wire-cut EDM to produce press dies for automotive components, which require particularly high shape and pitch accuracy as well as exceptional precision in surface finishing.
Company President Chiyuki Kato says the MP2400 is proving valuable in the manufacture of components with strict specifications. “For example, we wanted to use press technology to make engine shafts, which were previously produced using cutting machines because of the precision requirements. To achieve this change, we needed a solution capable of high-precision processing of the press dies. The introduction of the MP2400 has made this possible,” says President Kato.
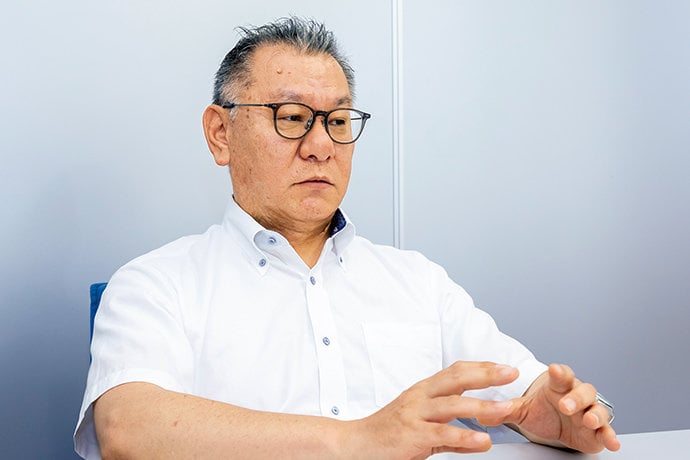
Chiyuki Kato, President, Kato Seisakusho Co., Ltd.
Customized design to deliver higher precision
Kato Seisakusho invested in an MP2400 featuring ultrahigh precision specifications that enable it to address even more demanding applications than the standard model. The machine is capable of going beyond Mitsubishi Electric’s accuracy guarantee of ±2 microns for stock MP2400 devices, and even is able to achieve circular accuracy within 1 micron using an optical drive system (ODS). Initially, this next-level machine was introduced as part of an R&D collaboration involving industry, government, and academia.
Ahead of the R&D project, the company conducted a comparative analysis of various processing machines, including evaluating samples that they produced. In addition to the extreme accuracy and precision that Mitsubishi Electric’s EDM offered, the team at Kato Seisakusho was also impressed by the company’s drive to deliver a high-quality solution that would meet their specific requirements. As a result, the component manufacturer selected the MP2400, which saw the R&D project bring good results. Technical Director Akiyoshi Haba, who oversaw the comparative study, says, “It’s fair to say it would have been impossible to realize the goals of the R&D project without the high pitch and circular accuracy achieved by Mitsubishi Electric’s ultrahigh precision machine.”
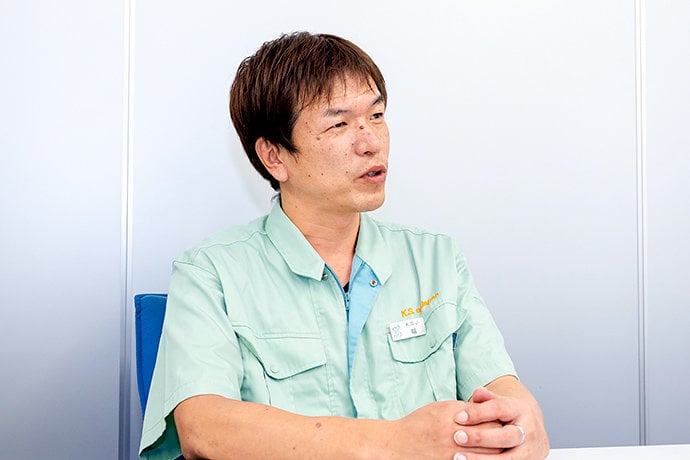
Akiyoshi Haba, Technical Director, Kato Seisakusho Co., Ltd.
Benefiting from complete after-sale services
Dies for automotive components need to be manufactured with extremely high precision. “We aim for a strict processing accuracy of ±2 microns, and the MP2400 makes this possible. We would not be able to achieve such good results with any other product on the market,” says Akiyoshi Haba. To process cemented carbide components, the optional ASC (aqua surface control) circuit is used as it minimizes the generation of cobalt, which could occur during wire-cut electrical discharge machining. The ASC helps produce a clean surface finish – another point that is highly rated by Kato Seisakusho. Prior to the adoption of the MP2400, extra machining allowances would be required and a time-consuming finishing process needed to be performed by another machine. By offering a complete solution, Mitsubishi Electric’s ultrahigh precision machine has significantly improved processing times.
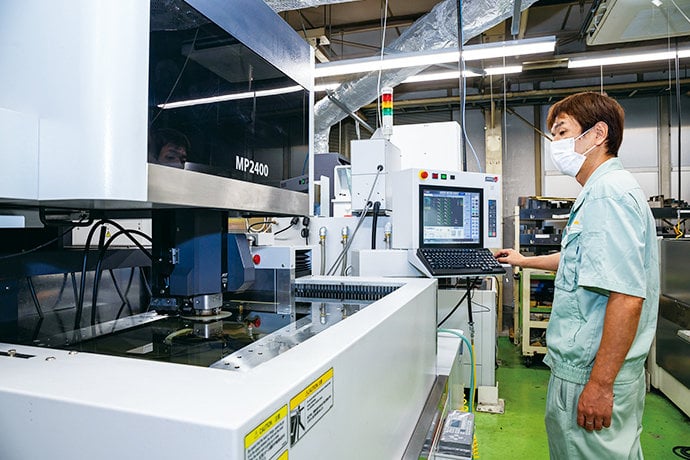
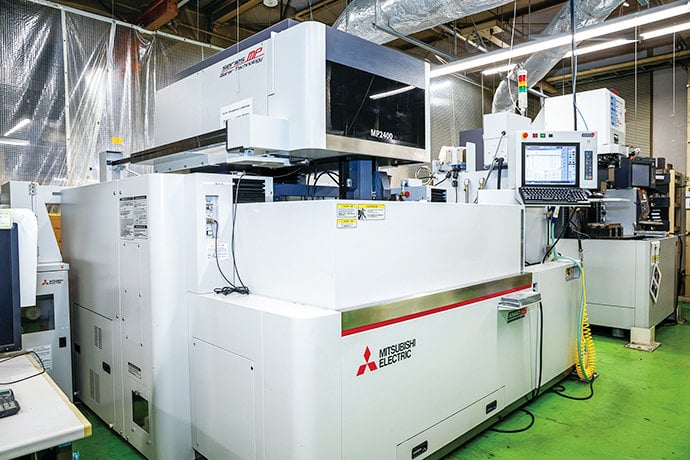
The standard MP2400 is a high-precision machine that has Mitsubishi Electric’s accuracy guarantee of ±2 microns. Systems featuring the additional ultrahigh precision specifications were designed to offer even higher standards. The optional ASC circuit produces a clean surface finish when processing cemented carbide workpieces.
Akiyoshi Haba is impressed by the MP2400. “Personally, I have a lot of experience using Mitsubishi Electric’s machines and I find them easier to use than other companies’ processing solutions, both in terms of hardware and software. Even a new employee without a technical background can quickly learn to use this machine, which we really appreciate.”
The company also benefits from Mitsubishi Electric’s after-sales support, which includes service and maintenance. Its ultrahigh precision MP2400 and MV2400R come with a 10-year “Support 10” maintenance contract, while its ten-year-old FA20PS and FA20 are covered by the 20-year “Life Support” contract. “We can use Mitsubishi Electric’s products with confidence, and the after-sales support is the best in the industry. I think this sense of reliability is a real strength of the Mitsubishi Electric brand,” says President Kato.