DOMO Chemicals presents a new optimized workflow simulation tool
As part of a collaborative project with Toyota (TME), Renault, SOGEFI, Hexagon Manufacturing Intelligence, and AROBAS Technologies, among others, DOMO Chemicals introduces a brand-new workflow simulation tool for polyamide parts in contact with water and coolant.
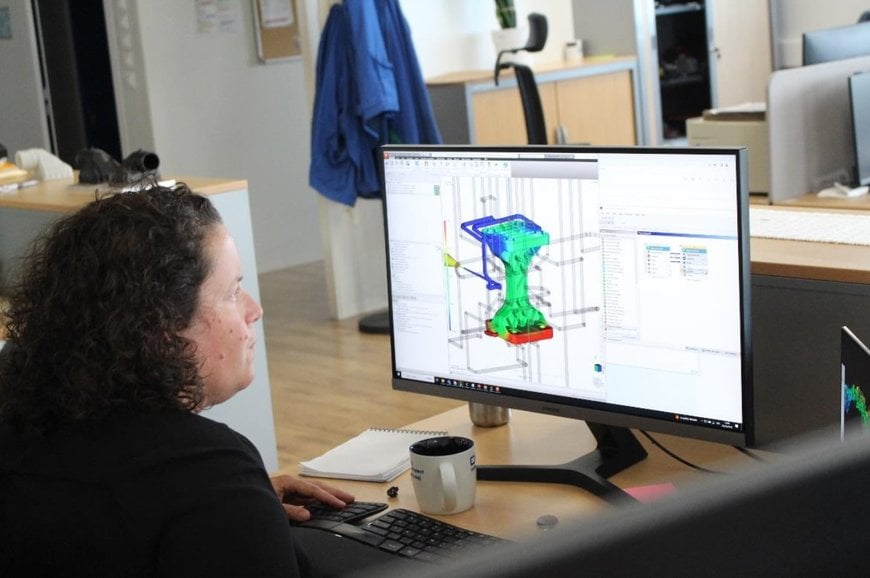
DOMO Chemicals presents a new optimized workflow simulation tool for predicting the effects of water and glycol-based coolants on heating, sanitary and automotive parts for their entire lifespan.
- THERMOFIP is a joint initiative focused on expediting the introduction of innovative lightweight components in the fields of mobility cooling and water management.
- THERMOFIP offers unparalleled opportunities for optimizing parts, leading to a substantial weight reduction of approximately 20% for the targeted components.
- THERMOFIP provides predictive simulation which reduces the number of design cycles of complex parts and limits waste generation during the prototyping phase.
This THERMOFIP workflow enables the prediction of parts resistance evolution after aging, supporting designers in shaping the right geometries for their new parts without the need for numerous tests.
Along with automotive applications, the THERMOFIP project also delivers prediction capabilities for heating and sanitary applications, which routinely come into contact with water and coolant as well.
Key application examples for polyamide 66 glass fiber compounds in the automotive space are under the hood parts in contact with coolant. Not only is this the case for internal combustion engine vehicles, but also battery electric and hybrid vehicles, and even fuel cell vehicles.
In response to the need to reduce CO2 emissions and the resulting changes in engine architecture, accurate predictive simulation technology is becoming a must-have in the plastics industry.
The interactions between the compound’s main ingredients (polyamide and filler) and the main components of the coolant, water and ethylene glycol, are complex. They include plasticization, which significantly decreases the compound’s glass transition temperature and hence mechanical properties in standard operating conditions. They also include chemical degradation, through hydrolysis of the polyamide chains, and the coolant concentration, which can vary from one side of the part to another. This results in different mechanical performance levels of the material in different points of the part geometry and in time.
Additionally, the consequences of fiber orientation also need to be considered. Due to all these variables, it has been very difficult to predict local levels of performance of such parts through simulation – until now.
By optimizing the simulation and use of fiber-reinforced plastic parts exposed to water and glycol-based coolants, THERMOFIP provides a true game changer for players in the automotive cooling segment and plumbing industry. This outcome is just as important for material suppliers as it is for the companies designing the parts and the carmakers using them. On top of being able to simulate the behavior of static parts, THERMOFIP opens the way for simulating active components in their different positions with the related local stress effects.
“When calculating the final mechanical properties of a part made of glass fiber-reinforced polyamide resin, integrative simulation offers the advantage of also taking the forming process into account. This opens new possibilities for parts optimization with a significant weight reduction of around 20% for the targeted parts,” said Gilles Robert, Senior Materials Expert at DOMO.
“Within the THERMOFIP project, we have created a kinetic model to simulate how coolants influence the progressive embrittlement of materials, in order to find new ways of making even lighter parts,” Robert added.
The new prototype simulation chain, designed in collaboration with Hexagon and Arobas Technologies, allows the local degradation of parts to be predicted. Several models are now enabling the prediction of material degradation levels caused by aging, which can then be used to anticipate the mechanical performance of coolant-exposed polymers. The study also includes the evolution with aging of material mechanical behavior for different fiber orientations.
The simulations have been validated by empirical testing. One example is the test run on the Localized Strain Demonstrator, designed and molded by DOMO Chemicals. The target pursued was to exclude failures in proximity of the metallic inserts. Results show a high correlation between experiments and simulations.
THERMOFIP is the last addition to DOMO's established MMI simulation offering, which already combines high quality Mechanical - Material modelling and Injection molding simulation.
SOGEFI Filtration module case study
A first case study was performed on a SOGEFI Filtration oil module made of a glass fiber reinforced TECHNYL® solution.
Simulation results reveal a few interesting trends and a good level of correlation between test and simulation. A key point is that failure does not happen on the oil module where hydrolysis is the most intense. It happens where an unfavorable combination of local stress concentrations, fiber orientation and hydrolysis can be found. This illustrates why a complex workflow taking several parameters into account is needed to predict failure in such complex parts.
The results obtained in this first phase of the project are very encouraging, showing good correlations between experiments and simulations.
The next steps of the project are to extend the model to other commercial coolants. The material database will be expanded to include new materials and, more importantly, more case studies must be undertaken to prove that this new technology can change the way polyamide parts in contact with coolant are designed.
www.domochemicals.com