www.industry-asia-pacific.com
14
'15
Written on Modified on
Jungheinrich Unveils Totally New Combi Stacker
Two-shift operation with a single battery / New synchronous reluctance motor / Lower energy consumption, thanks to intelligent lightweight design / Vibration damping system results in enhanced performance and safety on uneven floors
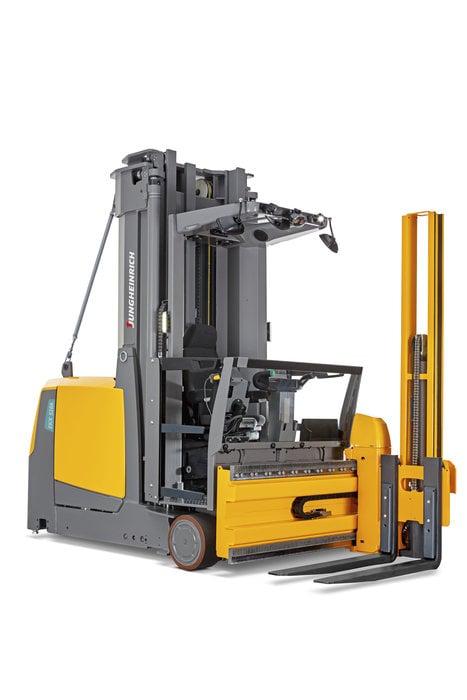
Efficient and Economical, with Just One Battery for Two Shifts
The truck is equipped with state-of-the-art control technology, completely new motor technology and an efficient energy management system. Its intelligent lightweight design makes use of high-strength steels, resulting in a weight reduction of 150 kilograms. “This means we can guarantee the efficient and economical operation of the stacker over two shifts with a single battery charge,” states Dr Klaus-Dieter Rosenbach, Jungheinrich Board of Management member in charge of Logistics Systems Business.
For two-shift operations this eliminates not only the need for extra batteries, but also for charging stations and other expensive equipment, while at the same time reducing manpower requirements. Rosenbach continues: “This is not a mere promise of two-shift operation without changing the battery – we also back up this claim vis-à-vis the customer.” In other words, if a battery fails to hold a charge for two full shifts, Jungheinrich will replace it free of charge.
Economical Motors: 93 Percent of Energy Converted into Output
Completely new motor technology developed by Jungheinrich is at the core of the EKX 514-516. This consists of a synchronous reluctance motor which has been used for the first time in this vehicle – a motor which combines the high performance and energy efficiency of synchronous motors with the cost advantages and low maintenance requirements of three-phase AC asynchronous motors.
According to Rosenbach the motor’s efficiency factor of IE31 is the highest achievable in forklift operations. The new motor technology converts around 93 percent of the energy consumed into actual output, cutting energy losses by half. “This means that energy consumption has been reduced by a further 15 percent compared to the previous model,” remarks Rosenbach. “And this, despite the vehicle’s much higher performance,” he adds.
Reaching Great Heights Smoothly and Safely, Thanks to Vibration Damping
For the first time Jungheinrich is also equipping this model series with a patented vibration damping system. The optional Floor Pro module reduces lateral oscillations of the mast and driver’s cab which are caused by uneven floors or other floor types not designed for narrow-aisle forklifts. “This system provides the user with the opportunity to travel more smoothly and up to 30 percent faster on substandard surfaces,” explains Rosenbach. In addition the system is easy on loads and vehicle and helps reduce the level of maintenance. The goal is to allow narrow-aisle trucks to work safely and efficiently even on floors that were originally designed solely for reach trucks – even at lift heights of 10 metres.
The new EKX 514-516 is fitted with a number of different modules for process integration, including RFID technology, redundant height and distance measurement and the Jungheinrich Logistics Interface. If the optional Jungheinrich warehouse navigation system with semi-automatic target approach is added, throughput can be enhanced by up to 25 percent. Dr Rosenbach concludes: “By combining intelligent assistance systems with high-performance synchronous reluctance motors, Jungheinrich has made great strides in further optimising energy efficiency – putting us in great shape to meet the future challenges of Intralogistics 4.0.”
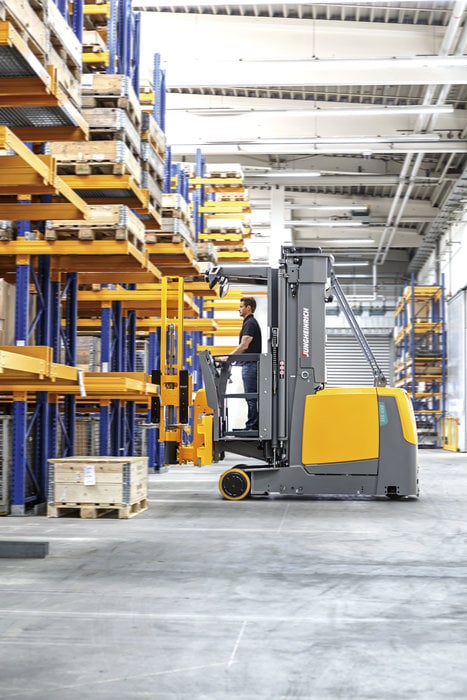