Welding control PRC7000 from Bosch Rexroth increases productivity when welding in the automotive sector
With the new functions provided by the welding control PRC7000, Bosch Rexroth allows precision resistance spot welding for greater productivity.
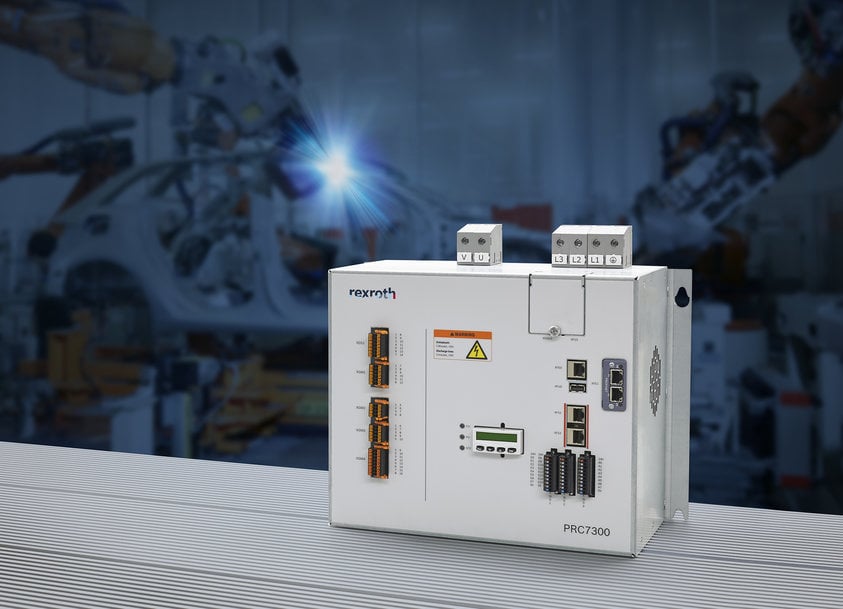
- Vehicle construction increasingly involves combinations of materials
- Welding control PRC7000 from Bosch Rexroth quickly adapts to different sheet thicknesses and material mixtures
- New function allows connections that could not be welded reliably in the past
The trend in vehicle construction is towards increasingly lightweight, safer vehicles. One reason: The less weight needs to be moved, the less energy is required. However, this must not be at the expense of safety. At the same time, designs and forms are becoming increasingly complex. Material combinations are increasingly being used to meet current requirements as regards weight reduction, energy efficiency, crash safety and design. This means completely new requirements when it comes to resistance spot welding. With the welding control PRC7000, Bosch Rexroth offers a solution which adapts quickly to different mixtures of materials and allows unbreakable connections.
Reducing CO2 emissions and fuel consumption is a key aim in the automotive sector. One way of achieving this is to reduce the weight of vehicles. Ever lighter materials such as aluminum, magnesium or fiber-reinforced plastics are therefore used. Lightweight construction is becoming increasingly relevant for electric vehicles too as a reduction in weight increases range and allows smaller batteries to be used.
The aim: Precision spot welding of different materials and sheet thicknesses
“320 parts, 80 different types of metal sheeting and coatings in various thicknesses – this results in around 500 combinations of materials and thicknesses welded together with 5,000 welding spots. This is a typical body in white nowadays. And the complexity is increasing,” explained Timm Bartmann, Head of Sales and Product Management Process Welding at Bosch Rexroth. “Various metals, plastics or composite materials are combined in the process. The use of new combinations of materials makes it possible to reduce the weight of vehicles, to improve designs and to develop innovative products. However, this means that resistance spot welding must be carried out to very high standards.”
The demands are particularly high where different materials have to be welded together, as each material has different welding properties. One example of this are body parts made of aluminum which are increasingly used in modern cars. They are lighter than steel but are also more difficult to weld. Special know-how and techniques are needed here to ensure a safe and stable connection.
“With the new lightweight designs, the use of high-strength steel materials with anti-corrosion coatings has constantly increased in vehicle construction in recent years. Using high-strength steels, components can be designed with thinner walls yet with the same mechanical properties. However, these materials are usually more likely to crack during resistance spot welding,” explained Timm Bartmann.
Another challenge: joining aluminum and steel using resistance spot welding owing to their extreme physical properties. Steel has a high electrical resistance, while aluminum has a low resistance. The welding control PRC7000 from Bosch Rexroth can cope with both of these extremes. Transformers convert the output power of the welding control unit precisely to suit the welding task in hand.
The solution: Perfect connections with a new generation of welding control unit
With the PRC7000, different sheet thickness and material combinations – from steel to aluminum – can easily be welded. To make this possible, the new welding control unit uses adaptive controllers and offers flexible programmability. It also makes perfect welding spots reproducible.
For the first time ever, a leading car manufacturer used resistance spot welding to attach large numbers of aluminum parts to the chassis of a new vehicle. In this case, the main body is made from aluminum and has approx. 2,000 welding spots with different aluminum sheet combinations.
“Due to the many new material combinations, the process windows are becoming smaller and smaller and, despite targeted parameterization of the particular welding task, connections can only be achieved to a limited extent with conventional resistance welding systems. With the PRC7000, unbreakable connections are possible,” said Timm Bartmann. “With the integrated “Adaptive Position Regulation” function, the PRC7000 allows welding of unprecedented quality. Even connections that were not so reliable in the past can be welded now.”
At the “Schweißen & Schneiden 2023” trade fair (from September 11 to 15, 2023 in Essen), Bosch Rexroth will show exactly how this works and all the benefits of the PRC7000 at booth 3A67 in hall 3.
www.boschrexroth.com