www.industry-asia-pacific.com
14
'23
Written on Modified on
Dürr Systems EcoQPower takes paint shop energy efficiency to a new level
EcoQPower uses energy flows in a completely new way to make automotive paint shop operations as energy efficient as possible. Dürr’s innovative system allows plant operators to move away from gas, a fossil fuel, towards climate-neutral production through electrification.
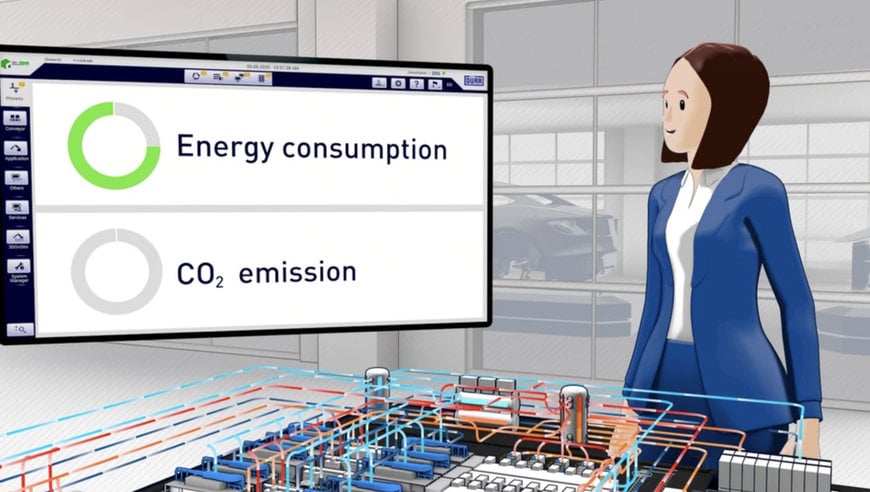
High energy prices, uncertainty about gas supplies, and climate targets, which require carbon-neutral production, pose significant challenges for paint shop operators. Dürr is meeting these challenges with EcoQPower, a new solution for optimizing paint shop energy consumption independently of production conditions. EcoQPower is based on a comprehensive analysis of paint shops’ individual heating and cooling requirements. By intelligently networking all components, their efficiency increases substantially, and almost no energy is left unused. “EcoQPower is a milestone in energy efficiency. Even in climatically ideal locations for paint shop operation, we are achieving energy savings in the double-digit percentage range. This is equivalent to the amount of energy needed to paint 13,000 to 20,000 cars,” says Dietmar Wieland, Senior Manager of R&D at Dürr.
Spotlight on the energy supply of the entire paint shop
Many individual adjustments have been made on the path to the sustainable paint shop, from products and layouts to digitalization, to keep increasing the energy efficiency of paint booths, ovens, and ventilation concepts, among other things. Instead of continuing to optimize individual elements, EcoQPower looks at the paint shop collectively, including the plant operator’s energy input. To get the most from all available energy sources, the energy flows for the supply of all the paint shop’s process steps are networked.
Intelligent network for energy flows
Getting the networking right is the decisive factor and requires a high level of expertise. It is comparable to the human nervous system, via which the body absorbs information and controls a wide range of mechanisms. Figuratively speaking, the networks in the paint shop form the “nervous system,” which redirects the heating and cooling flows from one process area to another. What does this mean? Instead of supplying each process area – for example, paint booth, oven, or pretreatment zone – with energy individually, often wasting energy in the process, each process area only receives the exact amount of energy it needs.
Identifying and using sources of waste heat
When electrifying processes, the temperature level at which heat needs to be provided is relevant for heat pump integration. Until now, there was one level for all processes which was geared, for example, towards the intermediate oven temperature of 80°C. However, the high-temperature water for heating is also used to operate ventilation systems which heat the room air to around just 21°C. This is exactly where EcoQPower comes in. Each process receives not only the right amount of energy but also the required temperature level, making it possible to exploit waste heat sources that previously went unused. For this, Dürr developed software that determines heating and cooling requirements in the form of a source/sink profile. This profile also considers the climatic site conditions and general framework data, such as production capacities, vehicle types, and available energy sources which can be incorporated, such as geothermal or solar thermal energy. Since each process has different requirements, for example, for the temperature level of heat and cold, Dürr clusters the various levels to combine them economically. Recognizing which waste heat sources can be used for what makes it possible to take advantage of synergies from the processes and to select and exactly size the right hardware components for the intended purpose, whether heat pumps, hot and cold water tanks, or a cooling tower.
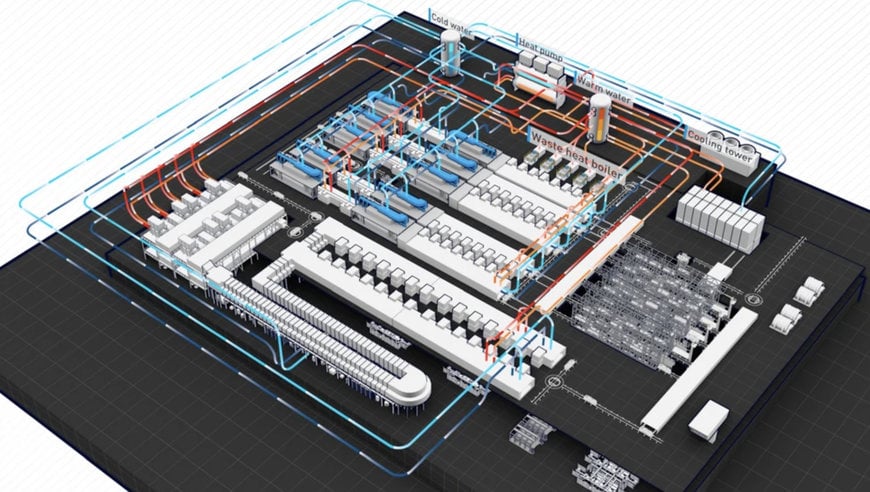
Keeping operating costs under control
EcoQPower also takes a different approach to energy supply, which until now was centrally organized for car plants. For optimal energy solutions, the cold and heat is generated decentrally within the paint shop using electricity, recovered there again, and distributed yet again to the components via intelligent networking. “EcoQPower improves each new plant’s energy efficiency, mostly in combination with specific energy-saving products, such as our electric oven EcoInCure and the electric exhaust air purification system Oxi.X RV. We are using these in our first project with EcoQPower in a new, fully electrified paint shop for a German car manufacturer. In doing so, we are minimizing energy consumption so significantly that it offsets most of the additional costs of switching to this more expensive energy source of electricity,” explains Dietmar Wieland. When a paint shop is electrified following the EcoQPower concept, its high energy efficiency not only helps to become independent from gas and keep operating costs under control but also to operate entirely carbon neutrally using green electricity.
www.durr.com