www.industry-asia-pacific.com
08
'23
Written on Modified on
Connected, smart, and cutting edge: Affordable telematics for all
By Andrej Lawaetz Bendtsen, head of Connectivity, Danfoss Power Solutions.

A couple of generations ago, the letters GPS were not widely known or understood. Today they are as familiar as ABC. Just 20 years ago, the idea of tracking something on the other side of the world to make informed decisions sounded like a distant goal, but GPS is now everywhere, having become a standard smartphone feature. This same evolutionary change has been taking place in the market for off-highway vehicles and stationary industrial equipment, with significant benefits for end users.
In recent years, telematics systems in the off-highway sector have evolved from simple functions, such as basic fleet tracking, to harvesting data exponentially from machines in the field. As the potential benefits of telematics became evident, it triggered a telematics arms race. Looking for commercial advantage, large original equipment manufacturers sank millions into developing proprietary systems that delivered the data-driven insights required by customers. Lacking the same resources, smaller OEMs were suddenly at risk of being left behind in this high-tech escalation.
Today, the need for offering telematics and connected solutions that smaller OEMs can easily integrate into their machines is driving innovation. Not only does this approach allow smaller companies to keep pace with larger competitors, it also provides them with competitive advantages. Just as smartphones have evolved alongside the growing reliability and prevalence of 3G, 4G, and now 5G, there is ongoing innovation in telematics solutions for off-highway mobile machinery and stationary industrial equipment.
Connectivity in harsh operating conditions
With connectivity demands continuing to ramp up in the off-highway sector, manufacturers face several challenges related to operating environments. Systems and solutions need to be sufficiently rugged to withstand what are often harsh and remote operating conditions. Extreme temperatures, water, vibration, and dust — as well as the physical impact of off-road use — means there is no place for fragile technology.
With this in mind, OEMs should only consider products that are developed specifically for use and proven in these conditions. Connectivity is also unpredictable for machines working at remote sites or facilities. It is therefore essential to have reliable global partners to deliver the best possible connectivity to all corners of the world.
Benefits of connectivity
Just as it was with conventional vehicles, the first element of connectivity enabled in off-road machines was asset tracking, offering the benefit of knowing the location of fleet vehicles at all times. Further machine functionality followed, such as being able to look inside the machine and know what parts are being used and how. The ability to understand where, when, and how a machine is working has revolutionized productivity calculations.
Connectivity solutions have also given greater insight into the rate of work and condition of machines, making it easier to anticipate repair and maintenance needs, or at least properly plan inspection and maintenance. Eliminating unanticipated repairs helps to reduce downtime, which is one of the biggest headaches that fleet managers face, as having machines out of service increases operational costs.
Engineers at OEMs can also leverage the stream of data around machine use. This information can help them to improve designs and systems that make machines more durable and productive for a particular task. The data could help analyze test results for building more rugged systems by automatically processing anomalies.
Putting tools in the hands of OEMs
With the growth of cell networks and the accelerating rollout of 5G, data flowing from machines to the cloud expanded from a trickle to a torrent. Indeed, the information stream has today become so dense that it can quickly become uncontrollable if not managed effectively.
OEMs should therefore seek solution providers that can assist them in focusing on harvesting actionable data from the stream, focusing on data quality rather than just data quantity. Helping OEMs establish what they want to get from the data makes everyday operations more straightforward, faster, and more productive.
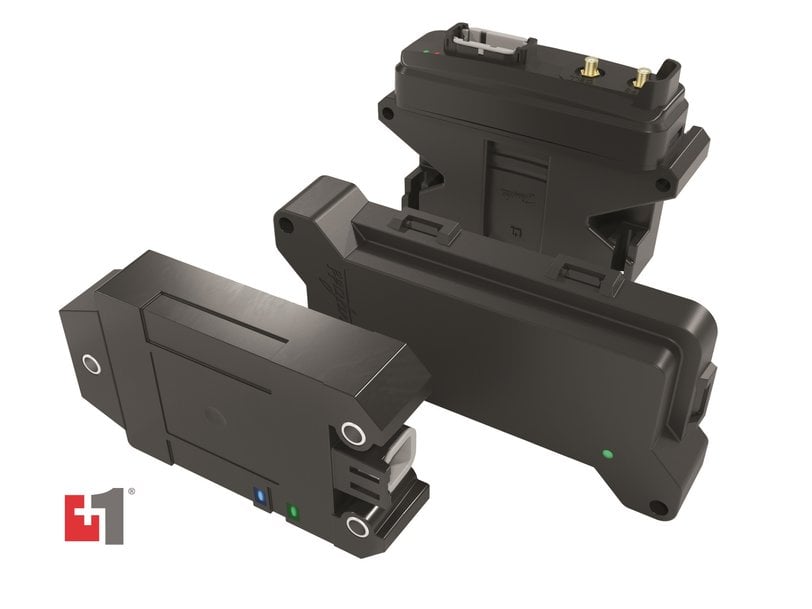
Looking ahead
In one sense, the evolution of connected machines continues as it has since the first GPS was used in the 1970s, relating to hardware, software, and global connectivity. The primary obstacle to an even more data-rich future remains the capacity of the global network.
Regarding hardware, leading suppliers continue to grow their sensor portfolio. The more sensors installed in a machine, the more data can be uploaded to the cloud. Having access to more data enables better optimization, unlocks efficiency gains, and reduces downtime. It can also enhance sustainability by enabling users to track and limit carbon emissions.
Today, off-highway vehicles and stationary industrial equipment can be connected via a cloud-based communication system. However, not all such systems are made equal. OEMs should seek out a solution that combines telematics-enabled hardware, gateway infrastructure, analytical capabilities, third-party applications, and a user-friendly portal, all on a single cloud platform.
By adopting a system of this type, managers can sit in the comfort of their offices and connect to any of their off-highway vehicles, whether they are moving concrete at a nearby construction site or loading timber in a forest 300 kilometers away. Once logged on, the management team can analyze detailed data regarding machine operation and productivity, or upload software updates.
A well-specified cloud-based communication system permits fleet managers to connect from any device and see how many hours their operators have put in on any given task, helping to optimize work schedules. Other benefits include seeing when a machine is operating, as activity outside of normal working hours or during the weekend might be a sign of unauthorized use. This type of system also allows OEMs to collect data about how, when, and where any errors occur on machines in the field.
Danfoss Power Solutions can offer a cloud-based communication system featuring all of these functions. Indeed, the company is continuously evolving its connectivity platform that is customizable and scalable, two attributes required to keep pace with evolving capabilities.
Of course, among the pertinent challenges with any cloud-based system is cybersecurity. This competency may be missing from the skill set of OEMs, particularly small and mid-sized companies, and ensuring protection against cyber threats also entails significant investment. Selecting a solutions provider with proven expertise in this area is therefore of paramount importance.
Towards predictive maintenance
The concept of predictive maintenance has long been the end goal for connected machines as it holds the promise of dramatically reducing repair costs and downtime, the two biggest pain points for machine fleets.
Danfoss Power Solutions has already worked on proofs of concept, collecting application-specific data to develop machine learning algorithms that provide reliable assumptions on product life and behavior. In one such application, the highly intuitive algorithm would predict if a machine requires maintenance 5 hours ahead of time. This development allowed the customer to take its first steps toward predictive maintenance, increasing the reliability and uptime of its fleet. This process is a continuous feedback loop to improve the algorithm with real-time data from the field, thereby increasing the accuracy to 99.8% while reducing the rate of false positives.
And yet, predictive maintenance is only as good as the data collected. To be successful on a large scale, this strategy requires enormous quantities of quality data and significant computer processing power to hold the artificial intelligence algorithms in hyperspace for each connected machine.
Anticipating network potential
Given the progress over the past 10 to 20 years, it would be foolish to limit thinking regarding connected machines. In the not-so-distant future, a massively robust global network could be realized that would make today’s fastest wireless network seem like the first telephone.
With the global data pipeline continuing to widen, development work on products, systems and solutions will continue, helping OEMs to capitalize on opportunities, many of which have not even been imagined today.
Linking connectivity with sustainability
As a final point, it is impossible to overlook the role that connectivity can play in supporting much-needed sustainability initiatives. Unfortunately, the transportation sector is still responsible for 22.3% of total EU greenhouse gas emissions, with heavy‐duty trucks and buses directly accountable for 5.6%. These statistics mean that decarbonizing the transportation sector is critical and a driver for implementing stricter climate protection measures. Current EU regulations state that manufacturers of heavy-duty trucks must reduce their average fleet emissions across the regulated vehicle groups by 15% by 2025 and 30% by 2030.
Creating a sustainable fleet program is one of the most significant contributions that fleet managers can make to achieve carbon reduction targets. To deliver an effective fleet sustainability plan, data that unlocks efficient decision-making is fundamental.
Fleet managers can use telematics to reduce emissions in several ways, such as promoting efficient driving by identifying and reducing unnecessary idling. Telematics can also manage the application of alternative fuels and powertrains in electric vehicles, cut the number of miles driven by optimizing routes, and take care of proactive vehicle maintenance. All of these capabilities demonstrate the positive influence of connectivity on corporate sustainability initiatives.
www.danfoss.com