www.industry-asia-pacific.com
16
'15
Written on Modified on
Quality down to the finest detail in the area of blisk and turbine blade machining
Haimer shrinking technology enriches Starrag machining centers with precision.
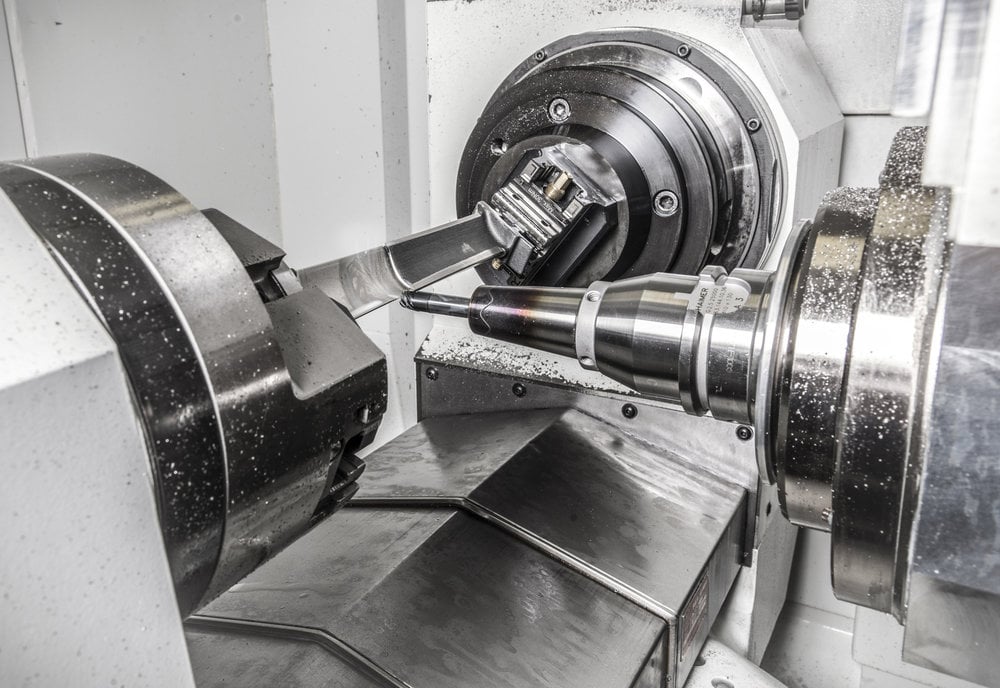
The product brand Starrag is located at the Starrag Group headquarters in Rorschacherberg, Switzerland (more company information can be found in the textbox). The company is mainly focused on the Aerospace & Energy Industry and offers five-axis machining centers capable of high metal removal rates in order to produce highly precise turbine blades, impellers, blisks and other structurally complex parts.
Since the beginning of the 20th century the aerospace industry has been the core market for Starrag machine tools. Even at that time they were able to distinguish themselves from other products and brands through their rigid and robust design and their high technological standard. Therefore it is no surprise that in the 1960’s Starrag was regarded as one of the pioneers in the area of 5-axis simultaneous machining. A know-how-advantage that is clearly visible in their current high quality product portfolio which includes machine types such as the STC and BTP series for titanium machining. Furthermore, machining centers that are specialized in blisk cutting and the LX series are part of the portfolio and were especially designed for the highly precise, efficient and simultaneous 5-axis machining of turbine blades.
Patrick Rutishauser (Head of Application Engineering) explains: “technologically speaking, our machines are of premium quality. They are known for their high performance capacity and precision. Furthermore, we offer our customers additional value regarding the application.” Starrag considers itself to be a technology partner of its end users and is capable of designing and realizing complete processes. “When a customer approaches us with a component he needs 10,000 pieces of, we design the complete system for him and supply the machine including software, clamping fixtures, tool holders as well as peripheral components and machines.”
Such an additional offer is only possible after many decades of experience regarding the development of machine tools, CAM systems and special tools – and because of the application know-how which Starrag is able to acquire during the production of prototype and small series turbine blades. One area Patrik Rutishauser is responsible for: “My tasks include technology and software development for so called Single Blade Applications. In my team, application engineers work hand in hand with CAM-Software developers. This way we can provide our end-users with exactly what they need without taking any detours or wasting time.”
Experiences from the production plant
His co-workers are able to gain important experiences at the CPE (Center of Production Excellence), the Starrag application center in Rorschacherberg, where they test and optimize demanding, and new machining processes. The hall which has a surface of about 2000 m2 is equipped with the new four and five axis Starrag machining centers. There the application team is able to perform various applications ranging from heavy duty cutting of highly solid titanium alloy up to high speed cutting of light metal. Patrik Rutishauser emphasizes: “We work on rotating parts, complex cubic work pieces, as well as free-formed flow surfaces – we do all of this under production conditions. We also produce prototype and small series for our customers. This entails developing a drawing and quality production at reasonable costs in the market.” This is certainly an advantage, as the application specialist suggests, because that way you acquire valuable knowledge about the machine requirements and you can find out more about the integral machining process right down to the smallest detail. “It is different from customer demonstrations where you usually overlook minor details“, Rutishauser explains.
An important detail: tool holding
Starrag has known for a long time that “tool holding” is a very important issue when it comes to high precision machining. After all, they were using a high speed spindle (30,000 RPM’s) at their headquarters in Rorschacherberg even 20 years ago. At that time the cutting tools were usually clamped with Weldon or Whistle-Notch holders and collet chucks which, however, led to many problems because of the insufficient run-out accuracy they provide. At high rotational speeds even small deviations can lead to poor milling results, an inferior surface quality, as well as tool and spindle wear. Also the geometry of these tool holders has many interfering contours which make it impossible to reach deep cavities with minimally clamped tools.
Based on their testing of different tool holding systems, Starrag concluded it was necessary to use shrink fit chucks, which due to their rotationally symmetric clamping body have less interfering contours and a high run-out accuracy. During the initial tests with the new clamping technology, Starrag had to overcome some weaknesses: at that time the chucks were heated up with hot air which was very time consuming and placed great strain on the material.
About 15 years ago, in search of a solution, the Starrag specialists came across Haimer GmbH in Igenhausen who today is the European market leader in the area of tool holding technology. Patrik Rutishauser emphasizes that “Haimer professionalized the shrinking technology. Even back then the company offered a large selection of tool holders and a shrinking machine with an inductive coil and cooling bodies which were very easy to handle for anybody. Until today Haimer has kept on further developing its shrinking technology – tool holders and machines – and at the same time was always able to stay true to its high quality requirements. We constantly evaluate different systems and suppliers, but regarding precision and quality the products of Haimer are simply unbeatable. When it comes to shrinking technology we appreciate the possibility of clamping tools with short projection lengths and of course the slim contours in comparison to other clamping systems“.
Also with Shrink Fit Chucks every single detail is important
It is not without reason why the company philosophy of Haimer is “Quality wins”. Behind this concept there is the idea to only produce in the home town of Igenhausen near Augsburg in Bavaria, where the precision can be kept under control 100% of the time. There, all shrink fit chucks, even the standard ones, are made out of heat resistant steal and are fine balanced (at G2.5 at 25,000 rpm < 1 gmm unbalance). The functional surfaces are machined and ground extremely accurately and the taper tolerance is much more precise compared to the relative norm.
For special machining requirements Haimer is offering special shrink fit chucks. For example, the Power Shrink Chucks are suitable for special high speed or high precision milling applications. The patented design combines a low tendency towards vibrations with a high rigidity and a slim design on top. This special construction makes it possible for the operator to increase the cutting depth and the feed and thus reach a higher cutting volume while still maintaining a good surface quality. The Heavy Duty Shrink Chucks are especially designed for heavy machining with large cutting tools and they feature a reinforced wall thickness at the clamping area, a very rigid outer contour and patented expansion grooves in the clamping bore. This way, high clamping forces which can be compared to those of Milling chucks can be reached. The portfolio of shrink fit chucks is completed with the small Mini Shrink Chucks. These are one-piece shrink fit chucks with an extremely slim design and a 3 degree outer contour – designed for mold making.
Difficult material, high surface requirements
For Patrik Rutishauser this variety of shrink fit holder designs works as an advantage. He explains: “during the blade production made of extrusion profiles there are generally two procedures. First, it starts with a rough cutting process. During this process it is important that the chuck operates with a damping component in order to achieve a high cutting depth and feeds and to remove as much material as possible in one production stage. During the finishing process, however, there aren’t any strong cutting forces. At this point, a high runout accuracy and the balancing quality are of importance. The Haimer Power Shrink Chucks are ideally suited for both processes and if the cutting gets even tougher we simply switch to Heavy Duty Chucks.”
In terms of the shrink fit chuck quality the best is required for Starrag. This is due to the fact that during the roughing and finishing machining of titanium and other hard-to-cut materials, the cutting forces can be very aggressive on the interface between the machine spindle and the tool holder. “In the end, the key element is the part quality. It has to be perfect starting from the very beginning, because even the titanium blanks cost a small fortune. We are convinced that the tool holder quality is absolutely essential for the part quality”, Patrick Rutishauser explains. This is especially true regarding the surface quality, which constitutes an important factor. This is due to the fact that the turbine blades need a very precise structure in order to be very energy efficient. Nowadays you can get the desired structure through milling and without any additional regrinding. At the moment Starrag is capable of achieving a surface quality of Ra=0,8 µm – 0,4 µm.
High-end-shrinking machines ensure fast and easy tool clamping
In order to shrink tools Starrag has a Power Clamp Profi Plus NG in its CPE (Centre of Production Excellence) with which you can shrink all HSS and solid carbide tools with shank tolerance h6 and diameter 3mm up to 50mm within a matter of seconds. It is equipped with a patented double coil technology which means that the coil adapts itself to the length and diameter of the shrink fit chuck. During the shrinking process only the shrinking area is heated which reduces the heating and cooling time (via contact cooling) significantly. In addition there is a High-End solution for professional shrinking and cooling: a Power Clamp Premium machine that offers a spacious work surface, easy handling and linear guided cooling bodies with temperature monitoring. The machine at Starrag has an integrated length presetting – holding lengths exactly within 0.02mm – since tools always have to be shrunk to a precisely defined overhang length.
“Haimer shrink fit chucks are part of our standard equipment, because they offer the best conditions for process reliable cutting which people expect from us”, Patrik Rutishauser explains. “We don’t just use these products at our CPE, but we also sell them together with our own systems. Therefore it is important that the quality of the products always remains high. With Haimer we feel secure. I can’t remember a single incident where a tool holder was the reason for a customer complaint.”
The right machine tool for each application
The Starrag Group (about 1617 employees and around 390 Mio. CHF turnover in 2014) is one of the leading machine tool manufaturers and combines the brands Marken, Berthiez, Bumotec, Dörries, Droop+Rein, Heckert, Scharmann, SIP, Starrag, TTL and WMW. On different locations a broad range of machines for milling, drilling and grinding metal work pieces, composite material and ceramics is being developed. Each brand has its own specialties. The complete offering ranges from small high speed machining centers from Bumotec (suited for cutting components in the watch, medical, and computer industry) up to the Gantry machines from Droop-Rein which are many meters long and can fill an entire hall (suited for working on big, heavy work pieces). Their customers include internationally active companies that belong to the three target markets Aerospace & Energy, Transportation & Industrial Components and Precision Engineering. The portfolio of machine tools is completed by their technology support and general service and allows the customers to make substantial progress.
As a long-time partner of the aircraft industry the Starrag Group has the necessary competence to come up with precise turnkey solutions for the production of turbine elements. One standard element of such complete systems is the Haimer shrinking technology. Pictures: Starrag
Starrag uses Haimer Power Shrink Chucks for demanding roughing and finishing processes. Picture: Haimer
Because of the reinforced wall thickness in the clamping area and other constructive features the Haimer Heavy Duty Shrink Chucks are able to reach very high clamping forces and can be used for roughing processes with big tools.
Patrik Rutishauser, Head of Application Engineering, is convinced of the Haimer shrink fit chucks and machines: “Haimer professionalized the shrinking process.”
In order to shrink tools Starrag has a Haimer Power Clamp NG (left) at its CPE and a Power Clamp Premium. Both machines are equipped with a patented double coil which adapts itself to the length and diameter of the shrink fit chuck.
High-End solutions for professional shrinking and cooling: the Haimer Power Clamp Premium offers a spacious working area, easy handling and linear guided cooling bodies with temperature monitoring. Starrag has the optional length presetting integrated into its machine.
Close to the shrinking station you can find the Haimer balancing machine Tool Dynamic Preset, a combination solution to balance and measure tool holders and tools. For tools produced by Starrag itself, especially multi-stage tools, this machine is being used all the time.