www.industry-asia-pacific.com
11
'23
Written on Modified on
AMAZING color variety
Plastic has many advantages. One of them is that it can be imbued with any color. Whether pale eggshell, noble royal blue or gaudy orange – there is no limit to the colorful diversity of plastic parts. The coloring process can even take place "at the very last moment", just before injection molding of the actual part. With the dosing system colorDoS from HNP Mikrosysteme, it is also possible to switch between colors in record time. The FAULHABER drive plays a key role in microliter-precise feeding of the liquid colorant.
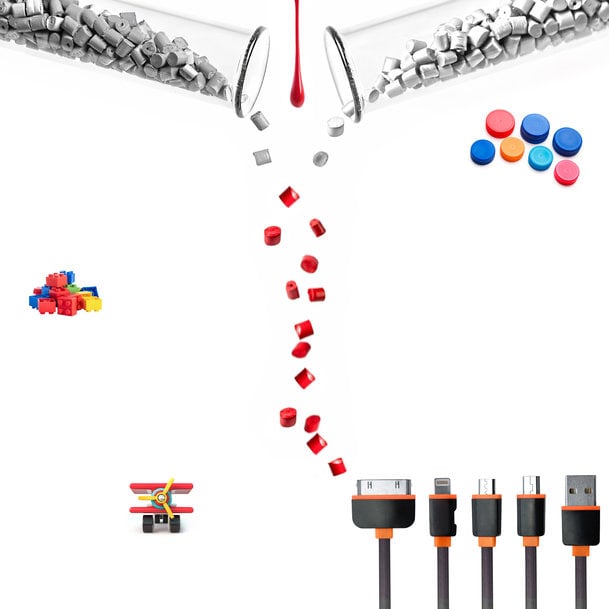
How many injection-molded plastic parts have I seen or physically handled today? Anyone who in the evening has asked themselves this question and tried to count the exact number of parts will end up going to bed very late. Plastic can be found everywhere in our world, and injection molding is the universal, cost-effective production method used to form it into almost any shape: The raw material, plastic granulate, is heated until it is flowable and is then injected into a mold. Remove any burrs and sprues – done.
Even if we decide not to count the exact number of plastic parts and just consider what has caught our eye, the range of colors we have seen during the day is sure to be enormous; the world of plastic is as colorful as the world of flowers and butterflies.
There are various ways of imbuing the neutral raw material with this optical diversity. If parts of identical color are produced in large quantities, it is often preferrable to leave coloring of the raw material to the plastic suppliers from the chemical industry. The granulate then already has the color of the final product. In many sectors and product areas, quantity is less important than the flexible and fast response to customer wishes, also with regard to coloring.
Dosing is key
In this case, the method of choice is to add the liquid colorant to the flow of granulate directly at the feed into the screw conveyor – so-called dosing of the injection-molding machine. In the cylinder, the granulate is simultaneously heated, thoroughly mixed and transported to the mold via the rotating screw. A dosing system is responsible for ensuring that the colorant is uniformly distributed in the granulate. The screw of the injection-molding machine in conjunction with the ram pressure then ensures that the colorant is mixed in thoroughly. Precise dosing is crucial for color quality. Here, the dosed quantities can be extremely small.
"We developed our compact dosing system colorDoS especially for processes where color needs to be changed quickly," explains Olaf Lang from Technical Sales at HNP Mikrosysteme in Schwerin (Germany). "Between 0.02 and 100 grams of colorant can be dosed per shot."
The sophisticated technology of HNPM ensures not only highly precise dosing of the individual colors, but also prevents so-called color carryover. Thanks to the special design of the dosing nozzle and hose couplings, it is possible to switch between different colors quickly, smoothly and without cleaning time.
A micro annular gear pump is responsible for the fine dosing. This is a miniaturized gerotor pump with an external and an internal rotor. The internal rotor has one tooth less than the external annular gear. The chambers created by this setup have a fixed displacement volume. The media are dosed volumetrically. The colorant quantity can be adjusted by changing the speed while maintaining the same dosing time.
Speed determines the color
"The quantity of colorant depends on speed and dosing time," explains Olaf Lang. "The faster the rotors rotate, the more colorant is fed in during the same period time, whereby the speed of the pump is adapted to the dosing time of the injection-molding machine. The cycle time also includes cooling and ejection of the workpiece. Then the pump stops briefly. Colorant dosing is therefore an extremely dynamic process."
Repeatability is an extremely important factor. To ensure that the products always have the same color, the quantity of colorant per shot must always be the same.
A mzr-7245 modular pump is used in the colorDoS. The smallest dosing quantity is 20 microliters per shot. This is less than one drop, but the special geometry of the dosing nozzle ensures that this tiny quantity is delivered with high precision and repeatability. "This is where the quality of the pump drive plays a crucial role. Apart from the motor, the analog Hall sensors too are of particular importance," emphasizes Lutz Nowotka, drive specialist at HNPM. "We have been using micromotors from Schönaich for many years. For colorDoS, we opted for a BX4 series brushless DC-servomotor from FAULHABER."
Precise positioning through Hall sensors
In addition to the high torque of 96 mNm, the strengths of the motor with the designation 3268…BX4 CS also include the small installation space, an extremely long service life and the integrated, high-precision motion control. "The analog Hall sensors enable precise positioning of the drive and therefore also of the rotors at 3000 positions per revolution. As a result, our pump doses with high precision even in the microliter range," explains Nowotka. "Here, good speed control and high torque even at extremely low speeds play a key role. The smallest of motion impulses must be implemented without jolts and jerks."
Via the serial interface, the controller receives detailed information about operation of the drive. Standby current, speed, position, deviation and temperature are captured with the utmost precision; the data is available for in-depth analysis of the device condition. Maintenance requirements can be detected early on when they first appear on the horizon, well before a failure becomes imminent. This ensures consistent dosing of the colorant for each shot as well as reliable operation.
The user also benefits from other advantages of the colorDoS system. Its display control communicates directly with the injection molding machine and indicates e.g. the time remaining until the next container change. The color code management system can be used to store recurring colorant recipes. An alarm manager warns of a low colorant level and stops the injection molding process in the event of a fault. According to HNPM, however, the core component of colorDoS – and other dosing systems – is the in-house designed micro annular gear pump that is driven by a FAULHABER motor