www.industry-asia-pacific.com
29
'15
Written on Modified on
Changing CAEs led to major workflow improvements
How EPLAN streamlined order fulfillment Manufacturers upgrading to an advanced, database-centric electrical CAE like EPLAN can reap important strategic benefits over and above making their engineers more productive.
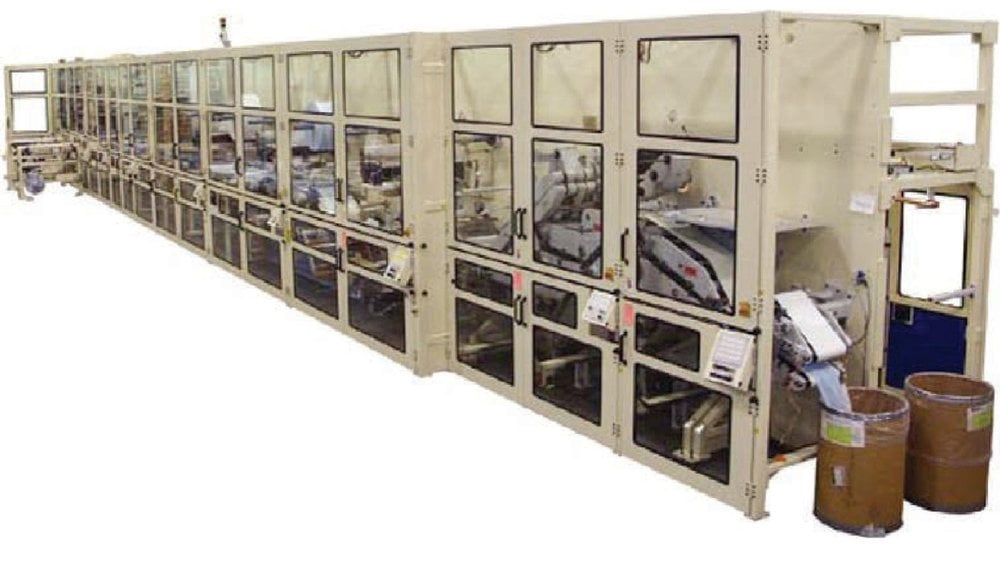
For Joa, EPLAN’s enhanced benefits include a more rational staging of engineering work that helps streamline preproduction and allows the company to raise output without adding engineering staff. For other companies, these higher level benefits can streamline the entire order fulfillment process and improve their competitiveness. Such benefits include:
• Shortened delivery lead times
• More reliable production scheduling
• More efficient workflows and procurement decisions
• Opportunities for standardizing and re-using design content
• Improved collaboration among stakeholders
Schematics produced in just a few hours
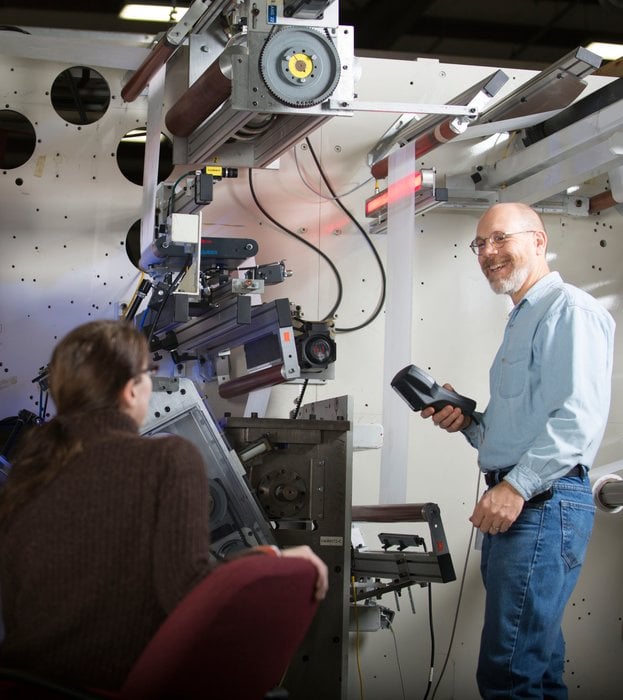
Previous approach favored early code writing
Before Joa adopted EPLAN Electric P8 in 2006, its electrical engineers used an ultra-conservative approach to fulfilling an order. “The electrical engineers didn’t feel comfortable unless they began programming immediately,” said Kevin Zeinemann, Engineering Manager. Software engineers also began writing code as early as possible, but as details of the project changed out of necessity, customers required revisions, and documentation and code needed to be reworked. Joa estimated at least a 30% savings in design time by switching from their current CAD system to EPLAN Electric P8.
Schematics data now leveraged for software generation
Joa discovered the possibilities of a different approach when it added the optional EPLAN Schematics Generator (now part of EPLAN Engineering Configuration One, also known as EEC One) four years later. The ability to automate schematics creation while using the same spreadsheet data to automate software creation has been an enormous time saver. Now, work can be performed in a logical, sequential fashion.
“In the past, it took us hundreds of hours to write the PLC code, but now we can wait until our machines have power for six weeks before we start writing code,” Zeinemann said. “Now we can wait a lot longer into the design process and give the customer more opportunities to make changes, which also gives our mechanical engineers more time to work. Now, our trigger is the lead time necessary for our hardware vendors to supply the start of production.”
Joa also archives templates in EEC One for each basic model. These are configurable for variables like power supplies, Ethernet switches, breakers, supporting terminals and much more.
These basics can be modified for the number of junction boxes, operator stations, sensors and valves – everything needed to generate the machine wiring diagrams. For the drive panels, an electrical engineer with input from the mechanical engineers creates a spreadsheet listing all servo-motor requirements with part numbers, locations and safety groupings.
Exporting .dwg files to expedite enclosure manufacturing
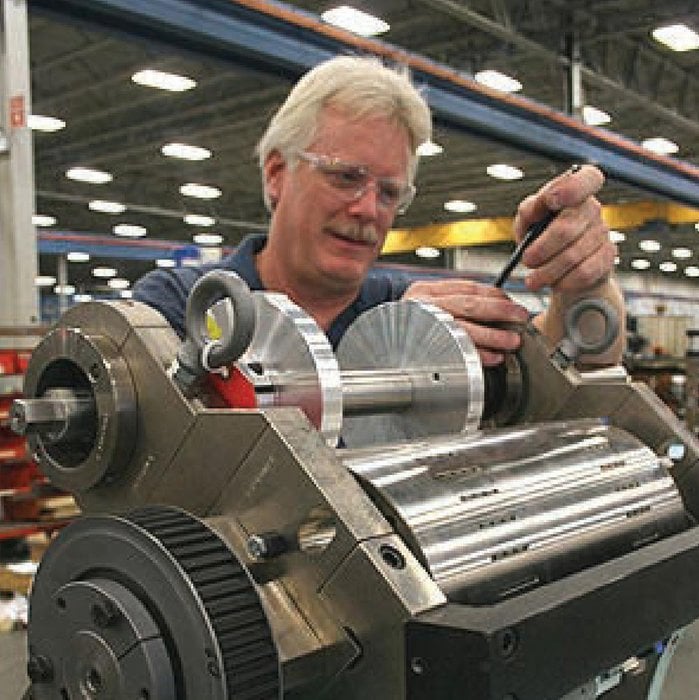
“We take that spreadsheet and import everything into EEC One,” said Engineering Coordinator, Bruce Davey. “This information is tied to another set of EEC One macros with all the variables embedded, which in turn will create schematics for one, two, three, four or five drive panels.”
“Each drive panel contains an average of 50 servo motors control-wise, so we might have 100, 150, 200, 250 motors on a machine,” Davey said. “It used to be a rule of thumb that if 200 pages of schematics were needed, it would take an hour per page to create, so 200 hours. Now, using EEC One, we’re able to do that in four to eight hours, and have great confidence that the results are correct.”
After creation of the schematics, the same I/O configuration data is transferred to the company’s Rockwell Automation RSLogix 5000 to generate the PLC software. Overall, Joa estimates that with both the ability to automate schematics creation with EEC One and the integration to Rockwell Automation RSLogix saved at least an extra 50% on design time.
In that sense, EPLAN also complements the company’s emphasis on modular design and manufacturing
Although Joa was familiar with EPLAN because some of their customers had requested documents in EPLAN format, it wasn’t until the launch of EPLAN’s Electric P8 in 2006 that Joa’s management was convinced to switch. Electric P8 met the company’s desire for a stand-alone CAE technology with a strong database architecture that wasn’t an AutoCad add-on and would integrate well with a Microsoft environment.
“If you understand databases and how a graphical database works, you immediately see the power in EPLAN,” Zeinemann said. “That’s what we’ve continued to do here over the past four to five years, leverage that database and understand how that works.”
Though all machines are custom orders, as much as 80 percent of their content can be based on stored, standardized modules in EPLAN. In addition, upgrading to Electric P8 2.3 provided an effective means to begin sending 2D EPLAN layouts as .dwg files to enclosure manufacturers to expedite production of the cabinets for each order.
The company makes EPLAN documentation available in smart PDF format for mobile devices or desktop computers. Many customers appreciate this flexibility because a complete set – up 1,000 pages – can be carried around by engineers or maintenance staff on a tablet.
“I measure our print packages in inches instead of numbers of pages,” Zeinemann said. “It would take a suitcase to carry a whole set in printed form.”
Eventually, Joa will likely archive all parts data, allowing it to be called up on touch screens throughout the plant.
Summary Curt G. Joa
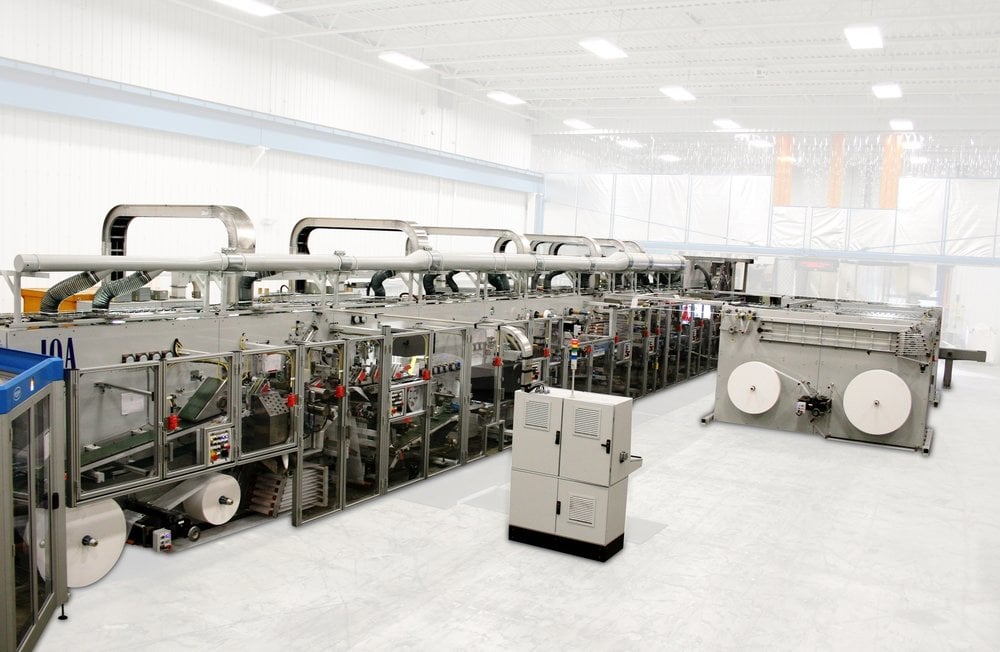
Leveraged EPLAN for huge time savings, workflow efficiencies
Curt G. Joa, Inc. designs and builds large manufacturing platforms used to produce disposable products such as baby diapers, sanitary napkins and incontinence pads. Using EPLAN and its Schematics Generator (now part of EPLAN Engineering Configuration One) to automatically create schematics and help drive its RSLogix 5000 software generator saves Joa hundreds of hours in design time and labor cost for each machine it builds.
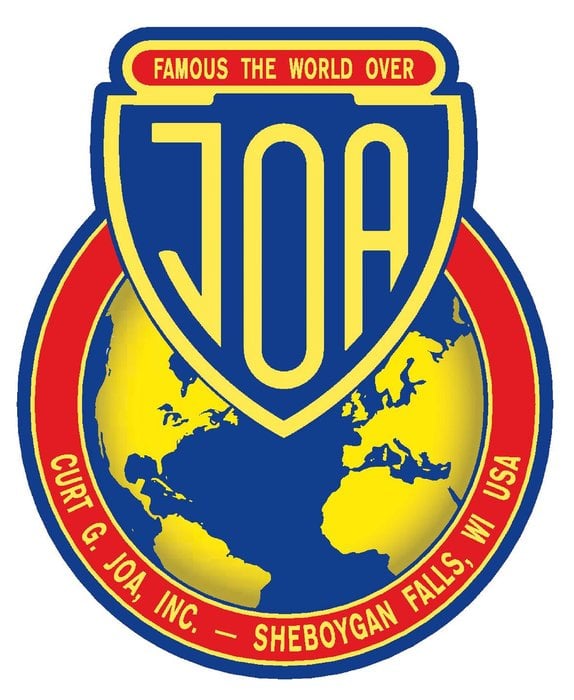
By automating most of the electrical design and software creation, the company can design workflows more efficiently. Less effort is wasted due to shortening design timelines made possible by EPLAN, giving the company confidence it can wait until customer approval of engineering packages is received before the PLC software is written.
Find out more about Curt G. Joa, Inc. at www.joa.com