www.industry-asia-pacific.com
20
'15
Written on Modified on
Distributed servo technology bends panels into better shape
Salvagnini simplifies the design of its machines using drive solutions from Kollmorgen
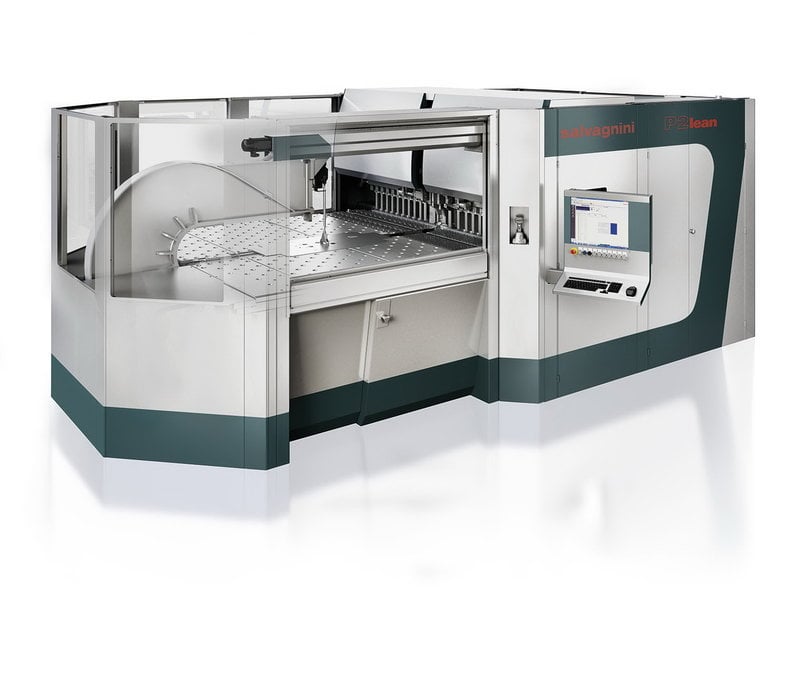
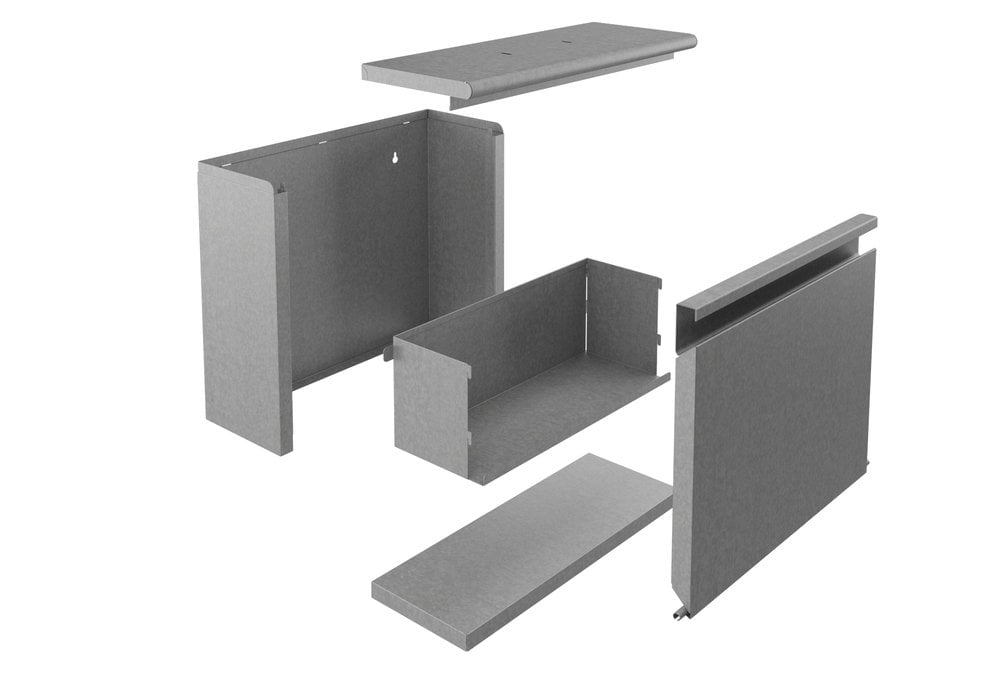
Another first by the Italian machinery manufacturer:
Replacing the central hydraulic pump by a synchronized network of electrically-driven servo actuators.
Each bending machine process cycle starts by the operator laying a metal sheet on the horizontal work surface. The workpiece is aligned to the bending unit fully automatically, by positioning axes under a blankholder. This clamps the panel in place while the bending unit, with its moveable blades, quickly performs any number of upward or downward bends. The precision of the reference position is essential for subsequent manufacturing quality because it is only done once for each workpiece during the processing cycle.
Drives simply placed next to the motors
To drive the built-in positioning units, Salvagnini uses distributed AKD-N series servos from Kollmorgen. With the new product generation, from the drive technology and motion control specialist, it is very easy to install the drives directly where they are required, in close proximity to the motors. One advantage of this distributed architecture comes from the dramatically reduced cost of the cabling for the seven distributed servo axes in the P2lean.
Using a central structure with control cabinet converters, the shielded cable between the motor and the drive and the cable for the feedback system previously could have needed laying up to 10 meters of cable. For the seven positioning axes that would have made a total of 140 meters of wiring (14 wires of 10 meters each). With this solution, using a central AKD-C power supply module in the control cabinet and seven distributed servo drives in two groups with three and four axes, this has now been reduced to only 40 meters. The total length is calculated as follows: two hybrid cables with power supply and feedback between the power supply module and the two nearest drive cables for a total of 20 meters, plus three meters for connecting the three axes in the first group and four and a half meters for a further three axes in the second group, knowing that the average distance between the IP67 devices in the system is not more than one and a half meters. The power supply to the motors then has to be considered. They are also installed not more than one and a half meters from the distributed AKD-N servo drives. Because the Kollmorgen solution is equipped with its innovative single cable connection technology, only 7.5 meters more cable is needed. Considering only the use of the distributed AKD-N servo drives combined with the single cable connection system, this saves 100 meters of cable - by reducing from 140 to 40 meters or roughly 71%.
More efficiency by using less
This careful management of equipment resources produces other improvements that are a direct result of having much shorter cables. They take up less space in the machine and not only that, they are quicker to install. The fewer number of connectors also saves time when connecting - which results in cost savings of 30 percent.
The other benefits of distributed servo technology are not inside the machine itself, - but in the control cabinet. Now that the drive’s heat loss no longer has to dissipate behind closed doors, the cost of cooling the cabinet is reduced. This produces two knock-on effects: firstly a smaller-scale and consequently cheaper cooling system and secondly, improved energy efficiency as a result of the control cabinet’s lower energy consumption. Savings of 30 percent have been estimated by Kollmorgen in real applications.
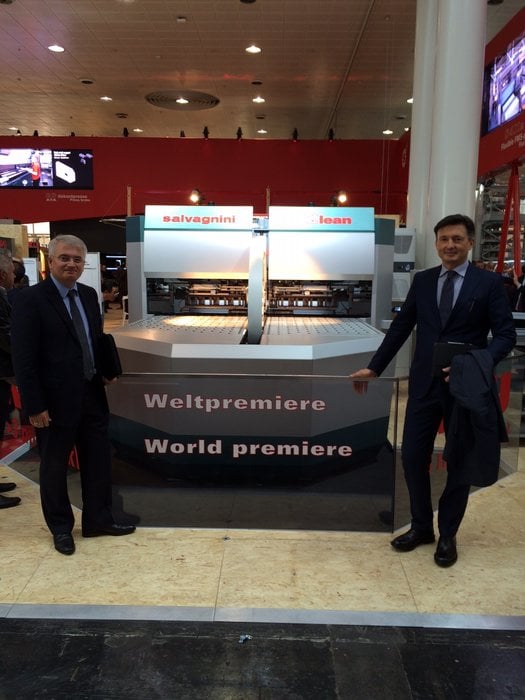
Space-saving, increased energy efficiency and lower installation and assembly costs are three benefits of distributed servo technology embodied by the AKD-N servo amplifiers from Kollmorgen, which also bring tangible cost savings with them. It is interesting to note that this strict management of resources, in this case also incurs lower cost for the hardware. When considering the drive equipment part of the installation, a distributed architecture costs at least 3.5% less than the central control cabinet solution for the smallest Salvagnini machine. For systems with more performance and a greater number of axes, gains of up to 10 percent can be achieved.
Increased energy efficiency
Savagnini are also using Kollmorgen's drive technology in another of their innovative advances. To replace the central hydraulic system, with a main pump and its correspondingly powerful asynchronous motor, they are using three highly efficient servo actuators, driven by Kollmorgen AKM servo motors and by S700 Series servo amplifiers, delivering power only at the moment the process requires it. Resulting from this, energy efficiency is increased, because the system drives only the active bending processes and does not have to keep the entire system with all its bells and whistles ready for operation. Thanks to the standard precision of the Kollmorgen drive axes, the required bending forces can be applied faster and with higher repeat precision, resulting in manufacturing quality improvement.
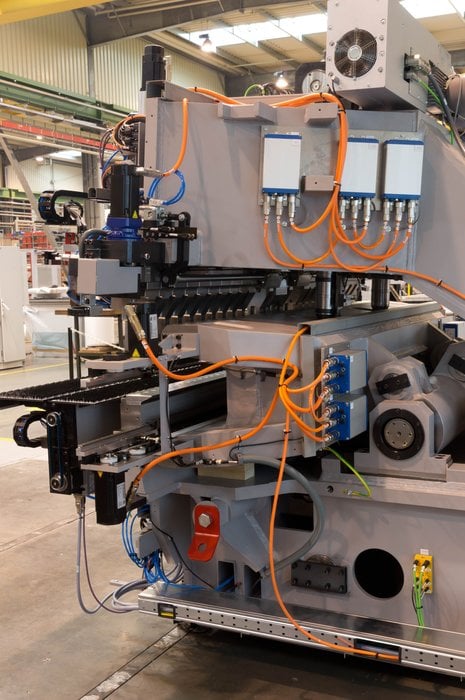
All in all, Savignini has succeeded with the P2lean in developing both an economic, ecological and consequently highly competitive machine for panel bending companies. The distributed servo technology from Kollmorgen adds a valuable contribution to resource efficiency especially in terms of cabling, control cabinet space and cooling.
Author: Fabio Massari, Sales Manager, Kollmorgen, Italy
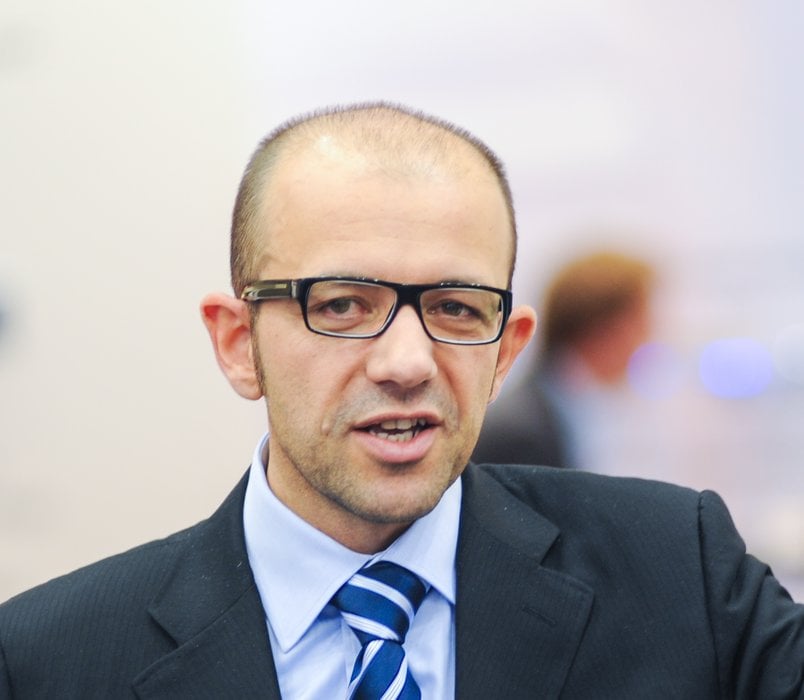
Fabio Massari