www.industry-asia-pacific.com
29
'22
Written on Modified on
Bosch Rexroth : Intelligent, sustainable hydraulics save resources
The current shortage of energy and raw materials, but also of skilled workers, is affecting companies worldwide. At the same time, climate protection and decarbonization are becoming increasingly important priorities for industry worldwide.
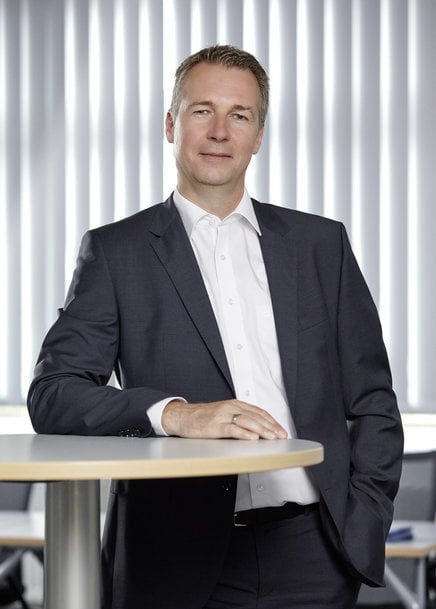
Intelligent, sustainable and safe hydraulic solutions make an important contribution to overcoming these challenges for machine manufacturers and end users of metal forming and sheet metal processing over the entire life cycle.
Software tools and preconfigured construction kits for hydraulic systems simplify engineering and speed up commissioning. By relocating previously mechanical functions to the software, the hardware variety is reduced and concepts can be quickly customized.
Designers parameterize the digital twins of intelligent hydraulic solutions as early as the design phase. On this basis, you can then shorten the commissioning time by transferring the saved settings to the hydraulic modules. Software wizards logically guide technicians through commissioning, even without specific knowledge of fluid technology. In this way, you can achieve stable and efficient controller settings more quickly.
For end users, the focus is on the availability and productivity of their machines and systems. This is where the hydraulics score with their high level of robustness and energy efficiency. Modern hydraulic units and ready-to-install, self-sufficient axles set new standards in terms of performance and energy efficiency with their variable-speed drive. They reduce the energy consumption of the hydraulics by up to 80 percent. Intelligent die cushion controllers for the lower ram recover energy and feed it back into the machine to reduce consumption.
To avoid unplanned downtime, data-based maintenance concepts are becoming more and more important. Networked hydraulics monitor component wear, enable real-time access to current and historical data and analyze it proactively.
Machine learning can be used to derive maintenance recommendations at an early stage from the data obtained, so that end users can replace the affected components in a planned manner. By avoiding unplanned downtimes and making maintenance easier to plan, considerable costs can be saved and productivity increased. The investment required for this is often amortized by avoiding a single unplanned plant downtime.
www.boschrexroth.com