www.industry-asia-pacific.com
18
'22
Written on Modified on
GRI (Spain) and Toshiba Digital Solutions Successfully Completed Proof-of-Concept in Visual Inspection Using Image AI at the Factory of the World's Largest Wind Power Tower Manufacturer
Toshiba Digital Solutions Corporation and GRI Renewable Industries, one of the world's largest wind power tower manufacturers, today announced details of a successfully completed proof-of-concept project in inspecting the surface and shape of large structures with high accuracy using image AI technology at GRI's Seville Plant in Spain since March 2021.
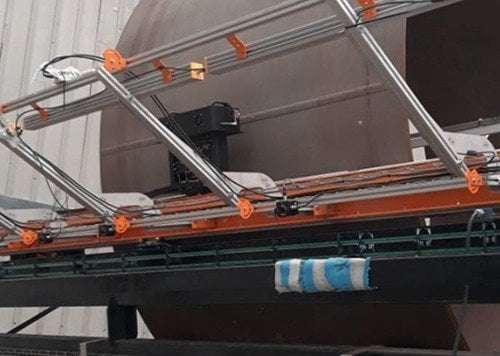
In the field of wind power generation, which makes great contributions to carbon neutrality, GRI manufactures and supplies wind power generation towers to major wind turbine manufacturers and is one of the world's leading manufacturers in terms of both production capacity and sales. With 16 manufacturing facilities in 8 countries including Spain, Brazil, China, U.S.A., Turkey, India, South Africa, and Argentina, GRI is capable of supplying towers of consistent quality to globally active wind turbine manufacturers.
Wind power towers are very large structures (3 to 15 meters in diameter). When performing visual inspection, it is required to inspect both outer and inner surfaces of the towers, as well as the shape of welding. Due to its large size and other issues of variation in quality, it becomes very time consuming for inspectors to conduct visual inspection. And there are not yet any feasible solution available on the market for inspection of such large structures.
Toshiba Digital Solutions is equipped with experiences and capability gained through actual use cases having image AI technology implemented in welding inspection for automotive parts (*1), leveraging the manufacturing know-how and analysis capability accumulated at Toshiba Corporate Manufacturing Engineering Center.
At the GRI’s factory in Seville, Spain, Toshiba Digital Solutions carried out this proof-of-concept project to validate the implementation of its image AI technology in large inspection equipment (*2) for wind power tower’s surfaces and welding. By combining Toshiba's image AI with the inspection equipment co-designed with GRI, the two companies have realized the automation of surface inspection and 3D shape welding inspection on large structures. The solutions are highly evaluated by GRI for the contribution to improved working time of inspectors and improved overall inspection quality.
Toshiba Digital Solutions will continue to expand the scope of such proof-of-concept project, together with its strategic partner Mitsui & Co., Ltd., a shareholder of GRI, aiming to horizontally deploy the achievements to GRI's other factories, and further contribute to the optimization of the entire manufacturing process as a strategic DX partner of GRI. Leveraging image AI inspection solutions as a starting point, Toshiba Digital Solutions is dedicated to solving social issues in the manufacturing industry by accelerating efforts toward smart factories.
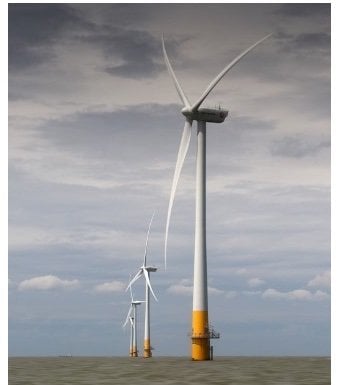
Wind power tower (The above image is for illustrative purposes only)
Figure 1 shows the co-designed large automatic inspection equipment for surface and weld shape inspection.
Towers are placed in the large inspection equipment with an automatic inspection system installed. By using camera and 3D system, surface defects and weld shape defects can be identified automatically, meanwhile defect locations are identified and registered by the system.
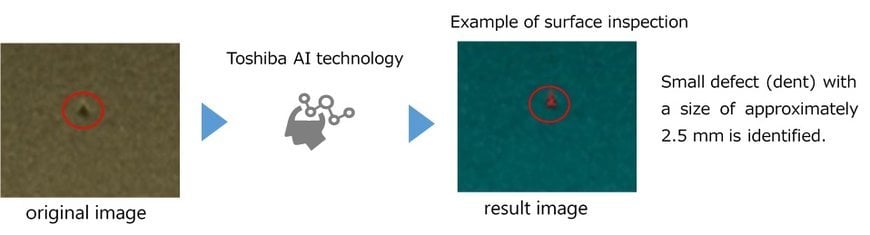
Outer/Inner surface inspection
Toshiba visual inspection package (*3) using Toshiba's proprietary non-defective learning method is adopted in surface inspection for wind power towers. In the proof-of-concept project, defects such as scratches and dents prepared in advance for evaluation were 100% identified.

Weld shape inspection
In weld shape inspection, weld defects such as undercuts and spatters are detected based on the reading of the weld angles and widths. In the proof-of-concept project, weld defects prepared in advance for evaluation which are critical to product quality, were all identified without omission.
www.toshiba.com