www.industry-asia-pacific.com
15
'22
Written on Modified on
Robust flexibility – highest levels of productivity and precision for automotive component production
Hammerer Aluminium Industries manufactures aluminum profiles for the automotive industry with highest levels of productivity and precision on Fill SYNCROMILL Q machining centers.
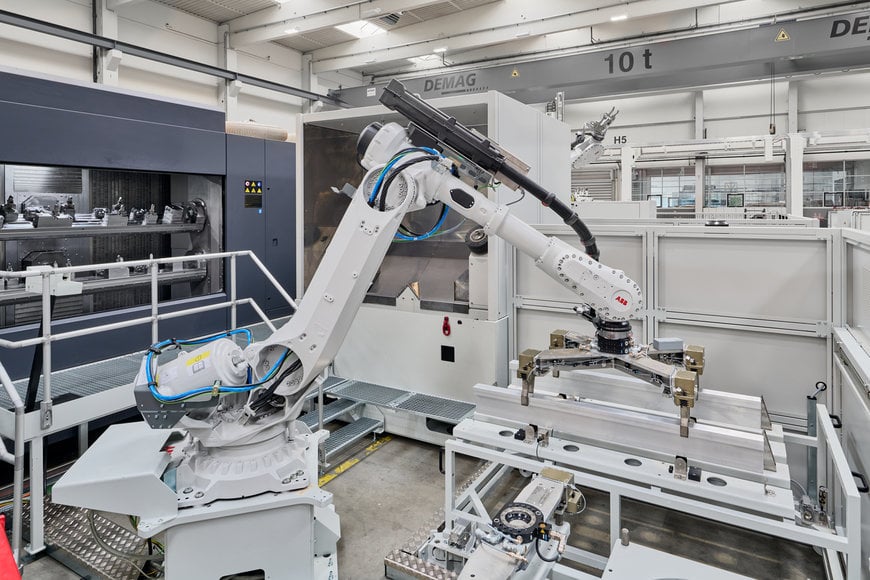
Hammerer Aluminium Industries is producing the structural components for a completely new platform of a premium vehicle manufacturer. The highly precise yet extremely productive machining of the produced extruded profiles takes place on twin SYNCROMILL Q double machining centers from Fill. Embedded in a robot-supported automation solution, the overall solution ensures maximum cost-effectiveness and flexibility for aluminum part production.
Hammerer Aluminium Industries is one of the most important manufacturers of aluminum components for the automotive industry. At its headquarters in Ranshofen, Upper Austria, it produces parts primarily for tier-1 suppliers all over the world, ranging from base plates and frame parts for traction batteries, through to load-bearing structural components.
Machine concept with parallel processing
Per shift, Hammerer Aluminium Industries manufactures 400 to 800 different brackets from 200- to 250-mm-wide extruded profiles produced in-house. In addition, the approx. 1,000- to 2,300-mm-long profile pieces are cut to length in numerous machining operations, milled to shape, furnished with several – some very complex – drilled holes, spindled, and deburred.
Machine engineering company Fill, based in Gurten, Upper Austria, manufactures the SYNCROMILL family of machining centers for the high-precision machining of large-volume workpieces. Available as a single or dual machine, the SYNCROMILL Q machining center has been developed especially for machining elongated workpieces with highest levels of productivity. Two or three machining spindles per machine chamber process the workpieces clamped on four axes in parallel. A laterally positioned tool magazine enables chip-to-chip times of less than 3.9 seconds.
Speed through automation
The system at Hammerer Aluminium Industries consists of one symmetrically designed double dual-spindle SYNCROMILL Q42-63/600 machining center and two standalone automation cells, each with one robot. The system can machine two times two workpieces in parallel. The robot subsequently brings the parts to a brush for deburring and places them in the laser station, where they are provided with a data matrix code (DMC) for traceability. As a dual machine, the system needs only one control cabinet, one hydraulic system, one chip transportation unit and one controller, and it needs only very little floor space.
In addition to high machining capacity, the benefits of the Austrian aluminum profile machining system include high flexibility thanks to its clamping fixtures and robot grippers, which are available as workpiece-specific technology packages in setup carts and can be replaced in less than 30 minutes. “Fill convinced us with a well-conceived solution for combining highest levels of robustness and precision, productivity and flexibility,” explains Hassan Lahchaychi, Manufacturing Technology Group Leader at Hammerer Aluminium Industries, who, as project manager, prepared the production order based on the customer’s performance specification. “The customer-oriented attitude of Fill developers facilitated the joint development of optimal solutions.”
Corporate data
Fill is a leading international machine engineering company based in Gurten, Upper Austria. With sophisticated high-tech systems and custom manufacturing solutions for metal, plastics and wood, Fill makes its customers the best in their fields. The automotive, aviation, sports and building industries all benefit from Fill’s expertise.
Since it was founded in 1966, the company has distinguished itself through enormous innovative strength, strong values and the best jobs. “If you are seeking the best solution, shape your future with Fill” is the guiding principle of the company’s more than 950 employees. “Wir sind 1! We are one!” is their vision and stands for togetherness not only with the team, but also with customers, suppliers and partners. The company is 100 percent family-owned and managed by Andreas Fill (CEO), Martin Reiter (CSO), Alois Wiesinger (CTO), and Günter Redhammer (COO). In 2021, Fill recorded sales of around 180 million euros.
www.fill.com