www.industry-asia-pacific.com
25
'22
Written on Modified on
WITH THE NEW PGL-PLUS-P, SCHUNK IS INTRODUCING A FLEXIBLE AND ROBUST POWERHOUSE THAT SHINES ABOVE ALL DUE TO ITS INCREASED SAFETY
The pneumatic gripper is the first in the world to have certified safe gripping force maintenance. Those, who are looking for a powerful, yet versatile gripper will be well taken care of by the new PGL-plus-P.
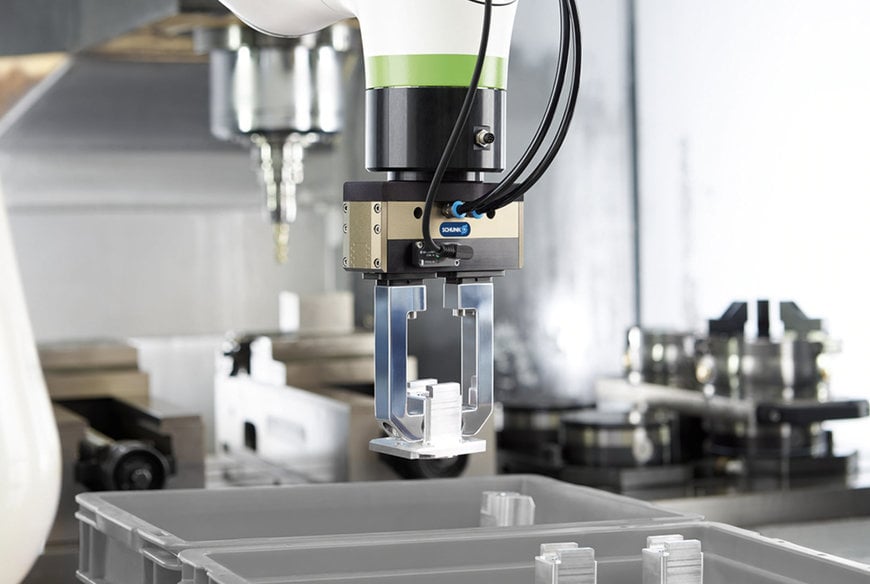
Those, who are looking for a powerful, yet versatile gripper will be well taken care of by the new PGL-plus-P. The pneumatic universal gripper is available in five sizes and offers a unique performance package of stroke, force, and connectivity, making it perfectly suited for handling tasks, where flexibility is required. Due to its long jaw stroke of 10 to 25 mm per finger, users can handle a wide range of parts with just one gripper. This saves investment costs and is particularly interesting for small batch sizes and high part variance, such as in machine loading and assembly. The new gripper has a gripping force of 220 N in size 10 and up to 1300 N in size 25. In addition to its flat design and proven and robust multi-tooth guidance, it also scores with its sealing as standard according to IP 64, which means that it can also do its job without further ado in dirty environments. In combination with an integrated air purge connection, the protection class can be increased to IP 67. Due to the standard H1-compliant lubrication, the gripper can also be used in medical and pharmaceutical applications or in the food industry.
Safety in system designs
With the PGL-plus-P, SCHUNK is pursuing a clear goal: More safety in use while simultaneously providing a wider range of applications. To this end, SCHUNK is offering the pneumatic gripper as the first in the world with the certified, safe GripGuard gripping force maintenance. This reduces the risk of operators injuring themselves during part removal, for example, to a minimum, as uncontrolled jaw movements in the event of a sudden pressure drop are eliminated from the outset. Also, no workpiece gets lost in the event of a failure or an emergency stop. At least 80% of the nominal gripping force is reliably maintained in the event of pressure loss. This saves time and costs when it comes to the CE declaration of conformity according to the Machinery Directive and the risk analysis of the entire system. In addition to the new GripGuard technology, the PGL-plus-P is also available on request with conventional gripping force maintenance via pressure springs.
Sensor systems with the highest accuracy
Another highlight is the already integrated IOL sensor system. It also increases the performance of the gripper and simplifies acquisition, commissioning, and repair by eliminating the need for external sensors. It can be used to monitor the finger position over the entire stroke range. It can also distinguish workpieces with high precision. An important feature for handling a more extensive range of parts. Users can switch between IO-Link and SIO modes. With the "Gripping Point Mode" and "Gripping Range Mode", SCHUNK also offers two sensor profiles for the conceivably easy programming of workpiece positions or areas. The program for the PGL-plus-P is versatile and combinable. This means that the gripper can be individually adapted to almost any application – for example, with conventional sensors instead of the new IOL sensor system, as a precision variant, or as a high-temperature variant for use at up to 130 °C.
www.schunk.com