Digital Manufacturing Enables Choice of 40,000 Models in a Five-day Delivery Window
Mitsubishi Electric's Nagoya Works Shinshiro Factory, located in Shinshiro, Aichi Prefecture, Japan, has manufactured three-phase motors since its establishment in 1974. At this factory, they significantly overhauled the manufacture of a key product range, the SF-PR series. By utilizing e-F@ctory based Digital Manufacturing processes and concepts it is now possible for customers in Japan to choose from 40,000 models available in a five-day delivery window, or for those prepared to wait 15 days, the choice expands to 2.3 billion different product variations covering the majority of customer’s needs and applications. Made entirely in Japan, from material procurement to parts processing and assembly, the number of product variations and the short delivery window demonstrates the factory’s capabilities for flexible, high-quality production with shortened lead times and improved productivity.
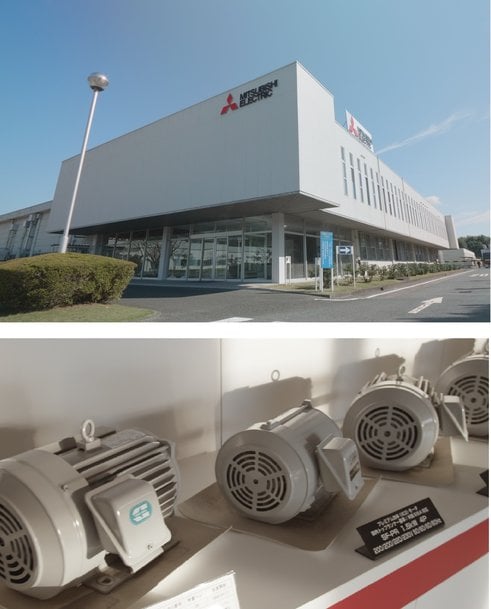
Mitsubishi Electric's Nagoya Works Shinshiro Factory has manufactured three-phase motors since its establishment in 1974.
“Our target was to tackle the long manufacturing lead time,” said Hiroyuki Akita, General Manager of Nagoya Works’ Shinshiro Factory, Mitsubishi Electric Corporation
“With e-F@ctory, we were able to increase productivity by reducing the time we need for complex procedures like preparing the set-up for the winding process and also the winding process itself,” Hiroyuki Akita continued.
e-F@ctory helped the factory to increase productivity by reducing the lead time for complex procedures like the winding process and its preparation.
“We wanted to determine where each process began and ended to measure the work time,” explained Noboru Shirakura, Senior Manager in charge of Manufacturing Engineering at the Shinshiro Factory. “Each worker's movements are basically lifting up the tool and placing it back again, so we measured the work time by attaching sensors to the tool holder.”
“We wanted to determine where each process began and ended to measure the work time,” explained Noboru Shirakura, Senior Manager in charge of Manufacturing Engineering at the Shinshiro Factory
The work time was measured by attaching sensors to the tool holders
“Our competitive advantage would rely on the automation of the shaft machining process and how much time we can reduce in this process,” said Hiroyuki Akita.
Noboru Shirakura added, “The bottleneck in the shaft line was the final grinding process. We wanted to shorten this process. So, we replaced part of it with turning in the preceding process.”
To reduce the machining performed by the grinder, data captured by the real time e-F@ctory process is fed back from the grinder to the NC lathe to stabilize the machining accuracy
The final grinding process (right) was the bottleneck in the shaft production line. Closer integration with the preceding turning process helped to reduce the bottleneck (left).
“We are currently trying to deal with tool wear in machining equipment. Determining the optimal setting will help us manage tool life and improve efficiency,” Noboru Shirakura explained.
With a tool wear diagnosis system, data can be automatically collected to determine the optimal wear value, or tool life.
With a tool wear diagnosis system, data can be automatically collected to determine the optimal wear value, or tool life.
e-F@ctory can be linked to the software platform "Edgecross" to easily collect and leverage data from machines of different brands or even older machine tools. This helps not only to visualize machine tool data and improve productivity, but also introduce a low-cost system in a short period of time.
“The three-phase motor is a mature product, so to be competitive in the market we would need a wide lineup and short delivery time, and in this aspect, e-F@ctory plays an essential role. Without e-F@ctory, we would not be able to provide products in such a short delivery time,” Hiroyuki Akita concluded. “By utilizing data for production, we now see new opportunities in this mature market. We will be able to create new services.”
There is no end to making improvements in manufacturing. And there is no end to business development.